DIY Acoustical Treatments

nikolas812
Posts: 2,915
I bought some Owens 703 acoustical rigid fiberglass a long time ago to make some acoustical asorbers but have never got around to it. So today while I was out and by Lowes I decided to pick up the necassay lumber and hardware and give it a go. Just incase anybody is interested I will post the link that I got the idea from and I will post a couple pics of the process. I managed to get four of them framed up today. There is supposed to be a total of six 24"x48" panels. But I cut my first four boards wrong so I will have to pick up one more 8 foot 1x4 tommorw.:o
You will need 6 sheets of 24"x48"x2" Owens 703 acoustical rigid fiberglass. $99.99 shipped to my door.
10 eight foot 1x4's $40.00
One box of 2-1/2" wood screws. $5.00
You'll need 60 yards of fabric also. I got two different colors Black and a Maroonish color for $57.00 at a fabric store. The fabric I got comes in a 60" width so I can cut it in half to make it work. So in realality I only needed 30 yards. Make sure you get the fabric part right as I almost didn't and almost ended up spending twice the amount I should have.
I used to power drills. One too drill a pilot hole and one to do the screwin. You will have to drill pilot holes ot the wood will split.
I cut the longest side boards just a hair under 4ft so when I put the end boards on it will hold the fiberglass in place.
I essentialy just built a box frame around the fiberglass. I cut 12 4ft boards and 12 2ft and 1- 1/2" boards for the ends.
I layed all the fiberglass sheets on the floor and layed the boards out in there postitions and drilled my pilot holes one at a time. One piolt hole and then one screw. This was so I could make sure all the boards were flush and even.
So thats all I have done for now. Tommorw I will get another board and finsh framing them up. And attempt to wrap them in fabric.
Here is a link to where I got the idea
http://www.audioholics.com/tweaks/do-it-yourself-diy-topics/diy-absorbers-for-the-less-than-handy-man-part-1
And here are some pics
http://
http://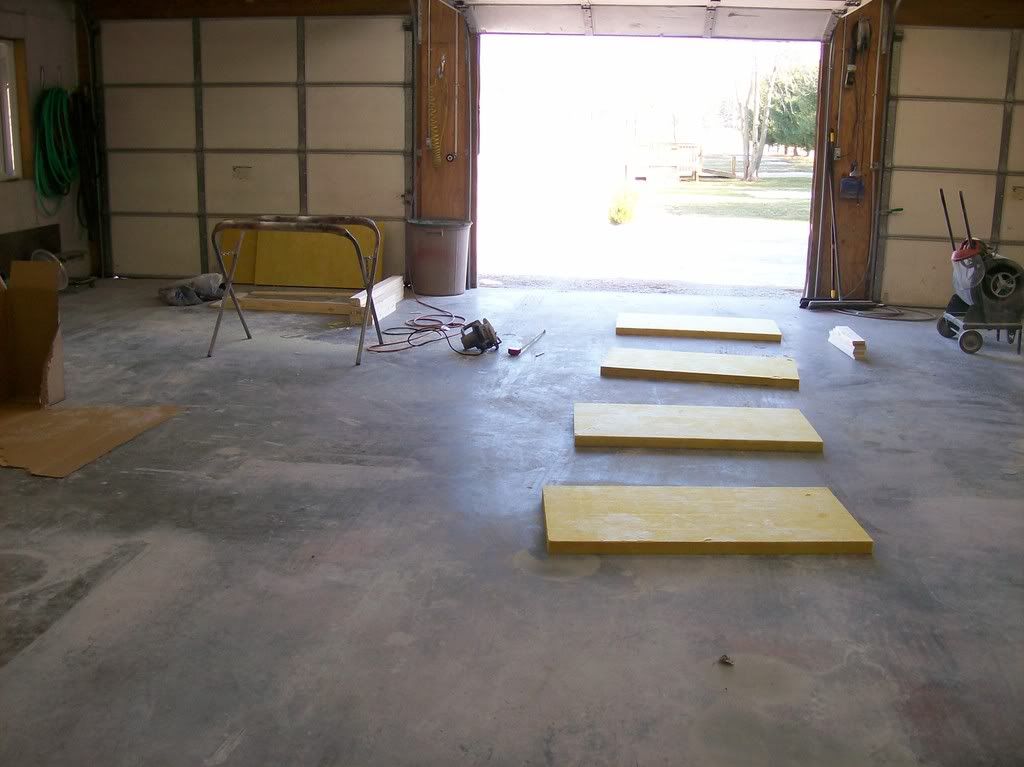
http://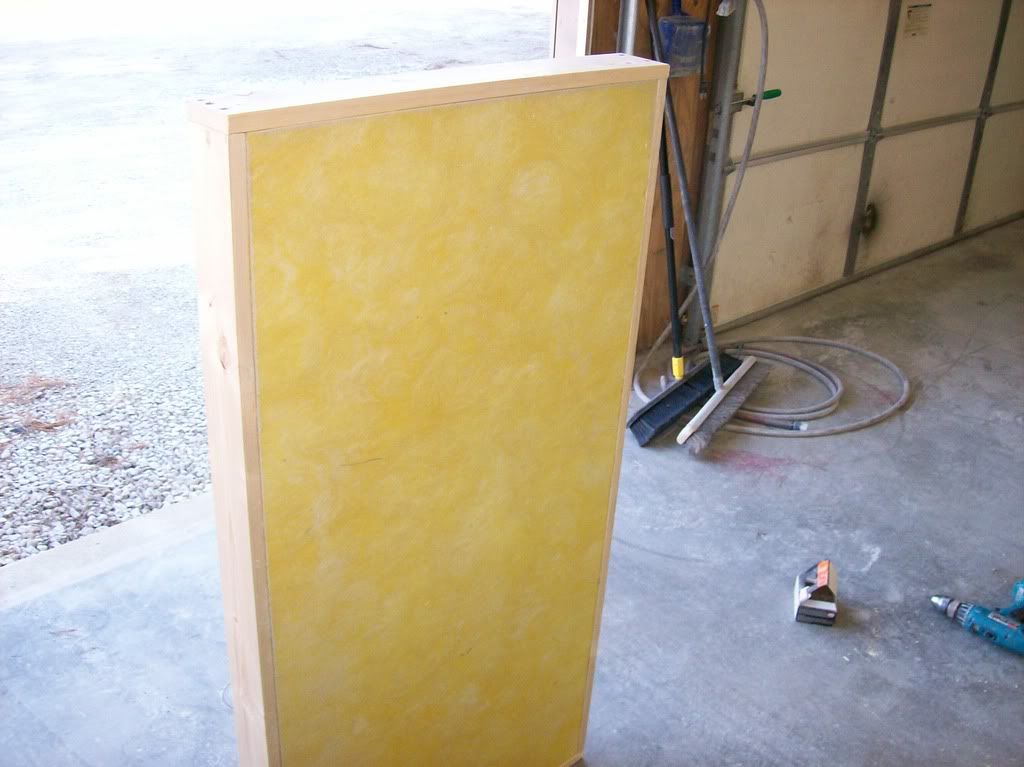
http://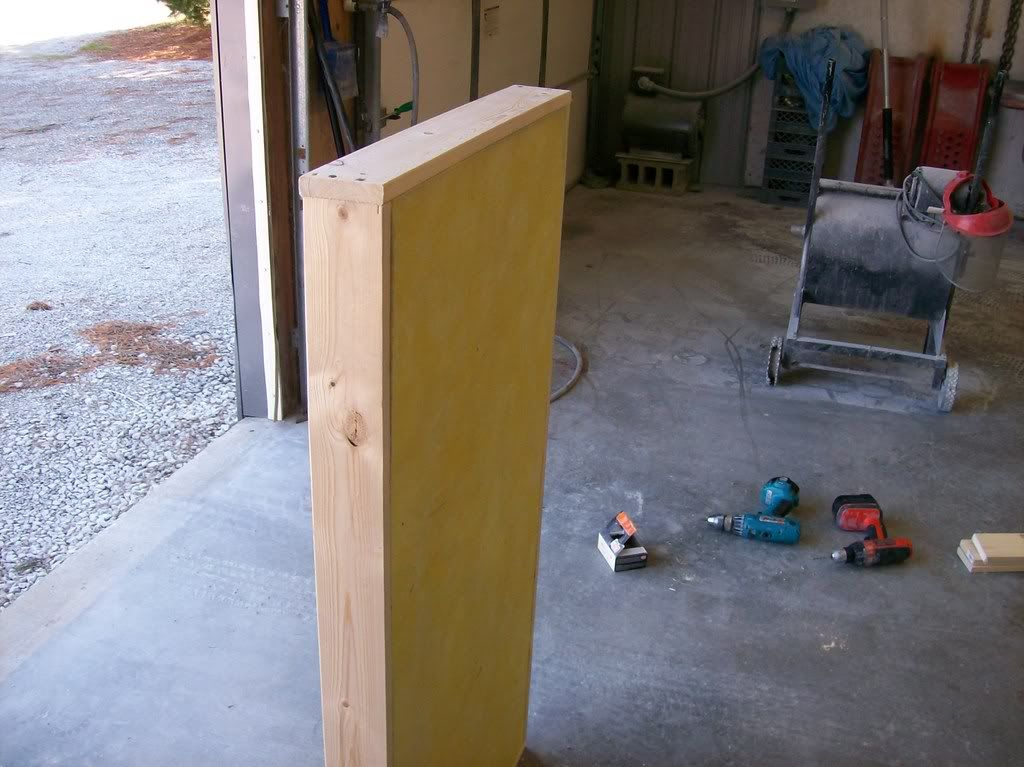
http://
http://
You will need 6 sheets of 24"x48"x2" Owens 703 acoustical rigid fiberglass. $99.99 shipped to my door.
10 eight foot 1x4's $40.00
One box of 2-1/2" wood screws. $5.00
You'll need 60 yards of fabric also. I got two different colors Black and a Maroonish color for $57.00 at a fabric store. The fabric I got comes in a 60" width so I can cut it in half to make it work. So in realality I only needed 30 yards. Make sure you get the fabric part right as I almost didn't and almost ended up spending twice the amount I should have.
I used to power drills. One too drill a pilot hole and one to do the screwin. You will have to drill pilot holes ot the wood will split.
I cut the longest side boards just a hair under 4ft so when I put the end boards on it will hold the fiberglass in place.
I essentialy just built a box frame around the fiberglass. I cut 12 4ft boards and 12 2ft and 1- 1/2" boards for the ends.
I layed all the fiberglass sheets on the floor and layed the boards out in there postitions and drilled my pilot holes one at a time. One piolt hole and then one screw. This was so I could make sure all the boards were flush and even.
So thats all I have done for now. Tommorw I will get another board and finsh framing them up. And attempt to wrap them in fabric.
Here is a link to where I got the idea
http://www.audioholics.com/tweaks/do-it-yourself-diy-topics/diy-absorbers-for-the-less-than-handy-man-part-1
And here are some pics
http://

http://
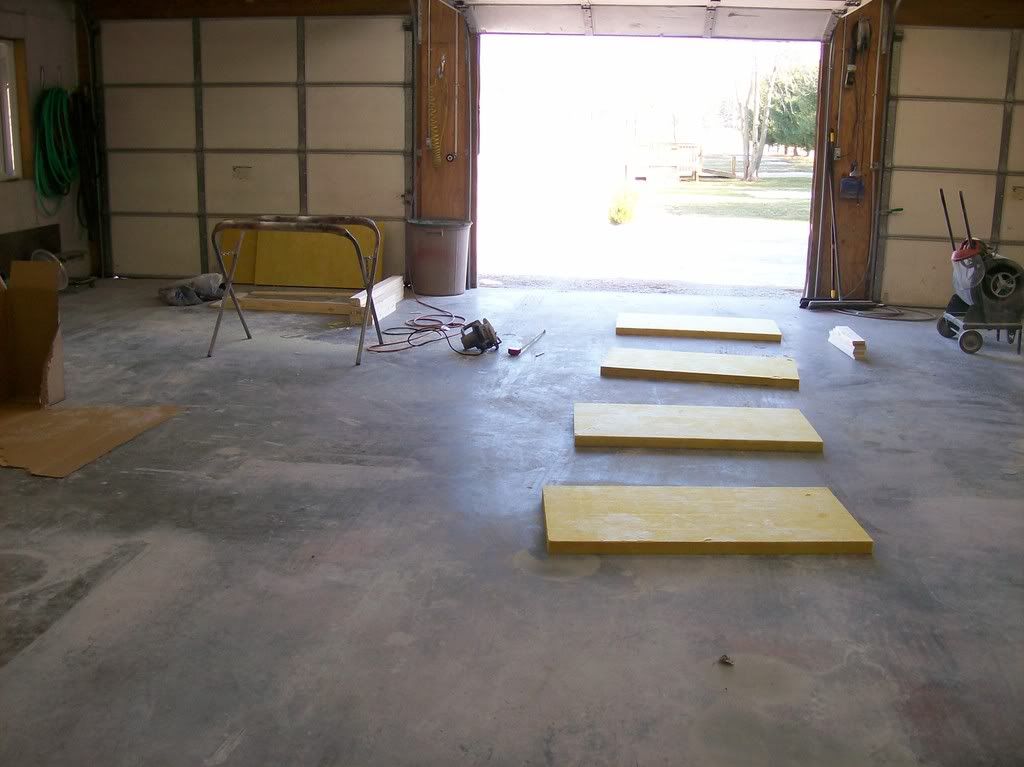
http://
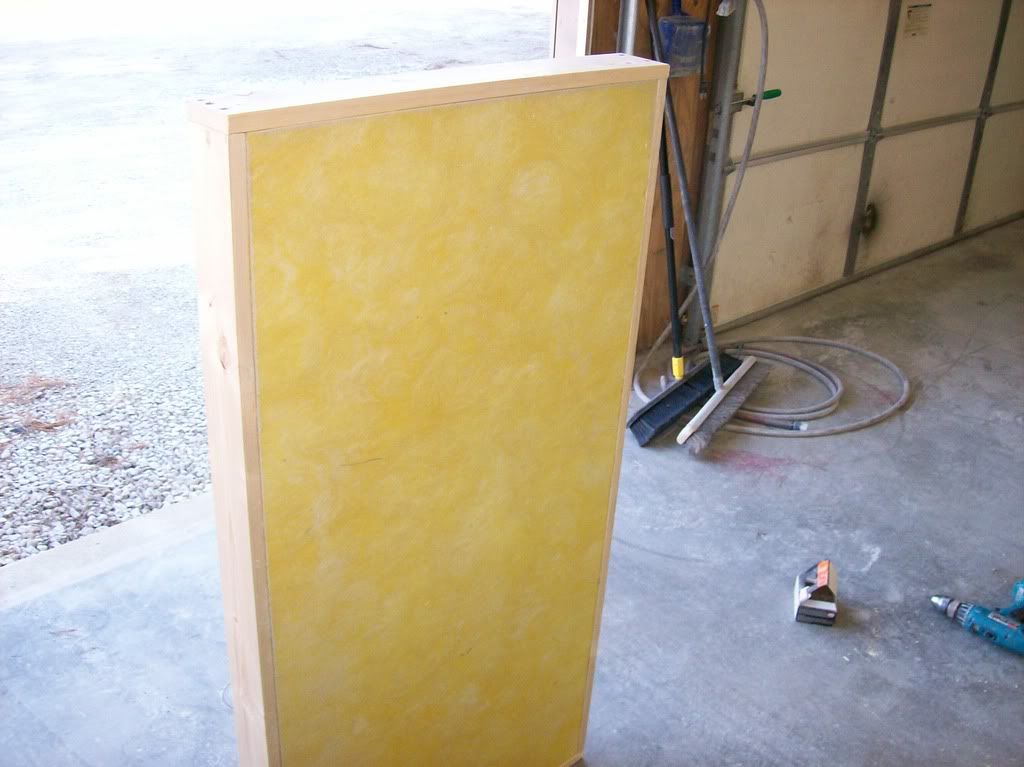
http://
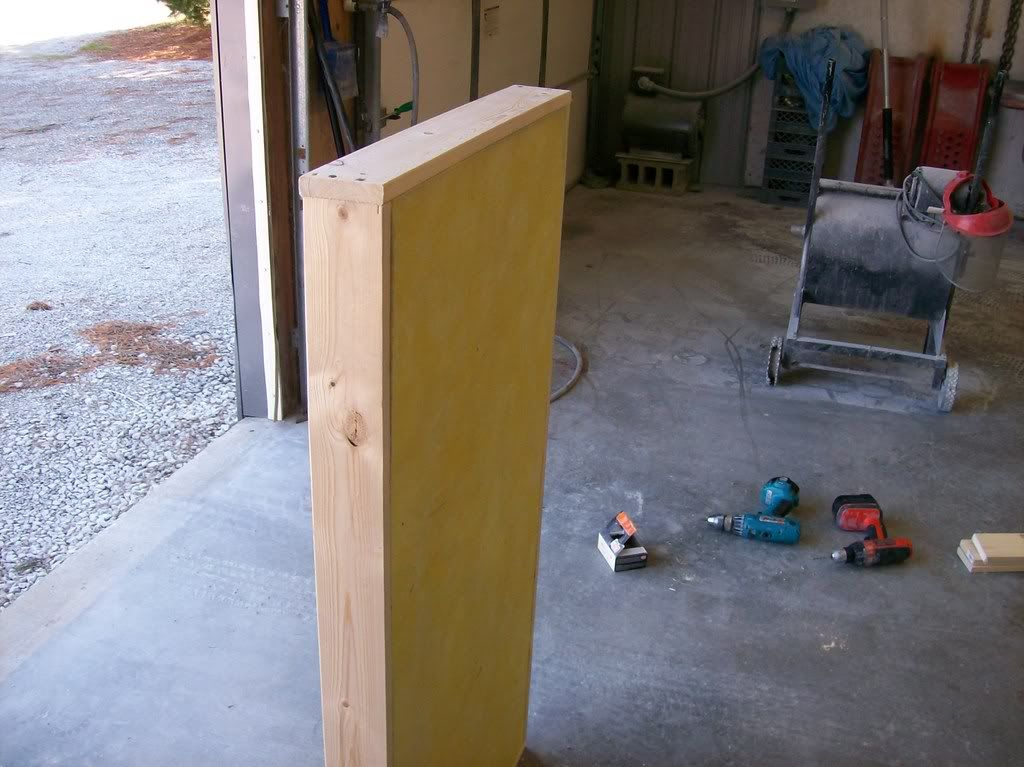
http://

http://

Post edited by nikolas812 on
Comments
-
Lookin good, and that's a heck of a nice workshop. Btw, what's that green stuff outside?
JoeAmplifiers: 1-SAE Mark IV, 4-SAE 2400, 1-SAE 2500, 2-SAE 2600, 1-Buttkicker BKA 1000N w/2-tactile transducers. Sources: Sony BDP CX7000es, Sony CX300/CX400/CX450/CX455, SAE 8000 tuner, Akai 4000D R2R, Technics 1100A TT, Epson 8500UB with Carada 100". Speakers:Polk SDA SRS, 3.1TL, FXi5, FXi3, 2-SVS 20-29, Yamaha, SVS center sub. Power:2-Monster HTS3500, Furman M-8D & RR16 Plus. 2-SAE 4000 X-overs, SAE 5000a noise reduction, MSB Link DAC III, MSB Powerbase, Behringer 2496, Monarchy DIP 24/96. -
joeparaski wrote: »what's that green stuff outside?
Joe
Coming soon to an area near you.......keep your eye out.:)
What kind of frequencies would those absorb?
Thanks,
MikeModwright SWL 9.0 SE (6Sons Audio Thunderbird PC with Oyaide 004 terminations)
Consonance cd120T
Consonance Cyber 800 tube monoblocks (6Sons Audio Thunderbird PC's with Oyaide 004 terminations)
Usher CP 6311
Phillips Pronto TS1000 Universal Remote -
No green grass in Canada I take it?
:D
Thanks. Thats only half the shop. I think iit is around 4000 sq.ft total. Its a our body shop right next to our home. So I don't even have to drive to work.:D -
Those look real good. Nice work.
-
Midnite Mick wrote: »Coming soon to an area near you.......keep your eye out.:)
What kind of frequencies would those absorb?
Thanks,
Mike
Gosh... I can't remember exactly. But its mainly for high frequency's. I think it is something like 100k-500k. The farther you can space them form the walls the lower they will absorb. Which is the reason for 1x4's and not 1x2's. the fiberglass is only 2 inches thick but by using 1x4's it will space them off the wall two inches.
I live in a trailer and the clap test is amazingly bad. I am having a really bad problem with the highs smearing together at higher volumes. I am in the process of turning my old bedroom into a dedicated listening room
(9'-1/2'x16') I just took down my bed and thats when things got real bad. I am hoping this solves most of my problems. I would like to think of this project as Stage One. I honestly have know clues whats going to happen or it will make anything better. I will have to just wait and see. -
BaggedLancer wrote: »Those look real good. Nice work.
Thanks.
I can't wait untill I get them wrapped in the fabric I bought. They should look sweet. -
4 inches is going to be about 800 hz & up.Gallo Ref 3.1 : Bryston 4b SST : Musical fidelity CD Pre : VPI HW-19
Gallo Ref AV, Frankengallo Ref 3, LC60i : Bryston 9b SST : Meridian 565
Jordan JX92s : MF X-T100 : Xray v8
Backburner:Krell KAV-300i -
Rough formula: (1100/size in feet)/4=Lowest freq absorbed.Gallo Ref 3.1 : Bryston 4b SST : Musical fidelity CD Pre : VPI HW-19
Gallo Ref AV, Frankengallo Ref 3, LC60i : Bryston 9b SST : Meridian 565
Jordan JX92s : MF X-T100 : Xray v8
Backburner:Krell KAV-300i -
4 inches is going to be about 800 hz & up.
This is where I got my info.
Heres a link to the whole page.
http://www.ethanwiner.com/acoustics.html
MIDRANGE AND HIGH FREQUENCY ABSORBERS
Without question, the most effective absorber for midrange and high frequencies is rigid fiberglass. Owens-Corning 703 and 705, or equivalents from other manufacturers, are the standard absorbing materials used by professional studio designers. Besides being extremely absorbent they are also fireproof and, when applied to a wall, can even **** the spread of heat. Rigid fiberglass is available in panels 2 by 4 feet and in thicknesses ranging from 1 to 4 inches. Larger sizes are available, but 2 by 4 is more convenient for most studio applications, and can be shipped more economically. As with all absorbent materials, the thicker it is, the lower in frequency it will absorb to. That is, 703 fiberglass one inch thick absorbs reasonably well down to 500 Hz. When two inches thick, the same material is equally absorbent down to 250 Hz. See the sidebar Measuring Absorption for more information about how these measurements are made.
For a given thickness, 703 is about twice as absorbent as acoustic foam at the lower frequencies, and it generally costs much less. Even better for low frequencies is 705-FRK, which is much more absorbent than 703 at 125 Hz and below. FRK stands for Foil Reinforced Kraft paper. This is similar to the paper that grocery bags are made of, but with a thin layer of metal foil bonded to one side. The FRK paper was not intended for acoustic purposes, but to serve as a vapor barrier in homes. It just happens to be good acoustically too. Be aware that the paper reflects mid and high frequencies when installed with that side facing the room; this may or may not be desirable for a given application. 705 is also available without a paper backing. Top
Although 703 and 705 fiberglass panels are more effective than foam of the same thickness, they are usually covered with fabric for appearance, and to prevent the glass fibers from escaping into the air. This adds to the expense and difficulty of building and installing them. (In practice, fiberglass particles are not likely to escape into the air unless the material is disturbed.) A comparison of 703, 705-FRK with the reflective paper exposed, and typical foam is shown in Table 1 below. Note that foam panels sold as acoustic treatment are often sculpted for appearance, and to better absorb sound arriving at an angle. Removing some of the material reduces foam's effectiveness at low frequencies. If rigid fiberglass was compared to solid foam panels of the same thickness, the disparity in low frequency performance would likely be less. However, not having a sculpted surface would then reduce foam's absorption at higher frequencies.
Material
125 Hz 250 Hz 500 Hz 1000 Hz 2000 Hz 4000 Hz NRC
Owens-Corning 703 0.17 0.86 1.14 1.07 1.02 0.98 1.00
Owens-Corning 705-FRK 0.60 0.50 0.63 0.82 0.45 0.34 0.60
Typical sculpted acoustic foam 0.11 0.30 0.91 1.05 0.99 1.00 0.80
Table 1: Absorption coefficients of 703, 705-FRK, and a popular brand of sculpted acoustic foam at different frequencies. All material is two inches thick and applied directly to a wall. This data was obtained from the respective manufacturer's published literature.
It's not difficult to understand why 705 fiberglass is so much more absorbent than typical sculpted foam at low frequencies. Besides the fact that sculpted foam has about half the mass of solid foam due to material being removed to create the irregular surface, another consideration is density. According to test data published by several manufacturers of rigid fiberglass and rock wool, the denser types absorb more at low frequencies. The data published by Johns-Manville for their line of rigid fiberglass shown below is one example. Acoustic foam has a density of less than 2 pounds per cubic foot (pcf) compared to 705 fiberglass which has a density of 6 pcf.
My own tests in a certified acoustics lab confirm this, showing denser types of rigid fiberglass absorb as much as 40 percent more than less dense types at 125 Hz and below. More recently I performed THIS series of measurements in my company's test lab, which shows the relationship between density and low frequency performance even more conclusively. Regardless of the reason, there is no disputing that for a given panel size and thickness, 705-FRK is substantially more effective at low frequencies than the same thickness of typical acoustic foam. However, it is important to understand that a material's density is but one contributor to its effectiveness as an absorber. Obviously, if the density is made too high the material will reflect more than it absorbs, so it's a mistake to conclude that higher densities are always better. For this reason, test data must be the final arbiter of a product's effectiveness. Top
As the data above clearly shows, 6 pcf rigid fiberglass panels absorb substantially more at low frequencies than less dense 3 pcf material.
One important way to improve the low frequency performance of any absorbent material - besides making it thicker - is to space it away from the wall or ceiling. For a given material thickness, increasing the depth of the air gap lowers the frequency range it absorbs. For example, 703 that is two inches thick and mounted directly against a wall has an absorption coefficient of 0.17 at 125 Hz. Spacing the same material 16 inches away from the wall increases that to 0.40 - a nearly three-fold improvement. Of course, few people are willing to give up that much space in their rooms! And even very thick (four inch) 705-FRK with a one-foot gap will not absorb the lowest frequencies as well as a purpose-built bass trap which is optimized for that purpose. Bass traps, absorption coefficients, and spacing of absorbent material will be described separately and in more detail later. Top
I also managed to get the four I had framed up completely done. They turned out pretty good for a first timer.
The camera wouldn't work right in the room for some reason.
They a just temporally in these spots until they are all finished and ready to be hung in the final resting spots.
Just by placing them in these spots around the room made a totally different sound when I clapped my hands. Not only did it stop echoing but it sounds totally different.
http://
http:// -
Oooo not feeling the red.
I think the color of the walls would have been better. Leave the focus on your gear...not your acoustic panels. -
Ahh... you're right. I was thinking bass standing waves, but it's a bit different for the higher frequencies.Gallo Ref 3.1 : Bryston 4b SST : Musical fidelity CD Pre : VPI HW-19
Gallo Ref AV, Frankengallo Ref 3, LC60i : Bryston 9b SST : Meridian 565
Jordan JX92s : MF X-T100 : Xray v8
Backburner:Krell KAV-300i -
BaggedLancer wrote: »Oooo not feeling the red.
I think the color of the walls would have been better. Leave the focus on your gear...not your acoustic panels.
It really looks a LOT better in person. I can't get the damn camera to work with them in the room. The outdoors pictures makes them look pink and the indoor pics makes them look like a dry blood red when actually it is neither of those colors.
Also they are the same color as my carpet. My drapes are black and the blinds are a camel color. so the black treatments match the drapes and the maroon treatments match the floor. When I am done I think it will look really nice.
When the room is completely done I will post better pictures so you can see the whole room and how everything works together. I hope.:(
I'm no interior decorator by no means.:D
I think it will come together though.
I have had a little time to listen to some music at low to mid volumes with them were there at now. It's MAJOR!. So far from what I am hearing . Everything is better. Everything. Its a totally different sound.
I can't wait to get the room completed now. I think its going to go to a whole other level.:) -
Ahh... you're right. I was thinking bass standing waves, but it's a bit different for the higher frequencies.
Did you go to the link?
I thought is was a pretty good read. I couldn't understand a lot of it though.:o But I took some in. -
Wanna paint my 2 Jolidas? I wanna make them blood red.
Kidding, partially. I might get them powdercoated at work. -
Can you strip your Jolidas down to nothing but the chassis? Or just the parts you want painted?
I wouldn't want to be responsible for them if you couldn't. Not to mention all the extra time involved in masking everything off.
Also I have a PPG mixing station. So if you see a car with a color you like. I can make the paint. I just need the paint code which is usually on or around the door. I also have a ton of colors already mixed. If you can give me idea of what color you had in mind I could give the cans a shake pop the lid and take a pic. If you like what you see... those colors I could do for free.
I would have to charge you something though. It wouldn't be much. But our booth is heated and cost money to run. I usually spray at 85 degrees and bake the paint at 140 degrees.
If you are serious please let me know. And I can give you particulars and answer any questions you might have.
Edit: By the way. Powder coating would be nice.... and durable. But I don't think they could make it as slick as I could. It would be done like a show car. There would be three coats of a clear and it would get wet sanded and buffed. It would look like a piece of glass when I was done.
Just let me know