What is a "cold solder joint"
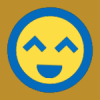
re510
Posts: 29
The reason i'm asking is that i have a mid 90's 5-ch carver and the front right channel has a very slight static buzz sound but only on this channel i did some trial and error and discovered is is the amp and it is only that channel. So my question is what sound does a cold solder usually yield? and can you identify it by looking at the solder joint? and do you have to remove the old solder or just re-heat and apply new. thanks
System:
Toshiba 51h83 HDTV
Yamaha HTR-5660
Carver AV-405
Pioneer DV-578A-S
Comcast HD cable
RT1000i's
RT35i's
CS400i
F/X300i's
SVS PCi 20-39
Toshiba 51h83 HDTV
Yamaha HTR-5660
Carver AV-405
Pioneer DV-578A-S
Comcast HD cable
RT1000i's
RT35i's
CS400i
F/X300i's
SVS PCi 20-39
Post edited by re510 on
Comments
-
A cold solder joint is typically a joint where maybe the soldering iron wasn't hot enough or enough heat wasn't applied for the solder to melt and really form a good bond. Or maybe the surface being soldered wasn't nice and clean and contaminent free. You may need a magnifying glass but usually you can wiggle the joint and notice a 'crack' in the solder joint. Sometimes it is very noticeable and sometimes they are hard to find. But they can cause static noises and/or intermittant cutouts, etc. It is best to suck the old solder out, clean really well then resolder although you can sometimes just remelt the existing solder or add a little new and get away with it but the problem will sometimes return.
It's hard to say if that's what you've got. They tend to be a little more intermittant unless it's a really bad joint.
It may be more likely to be something like a capacitor or a transformer? I don't know.....I'm not an electronics expert. I just know a little about soldering and finding solder related problems.2 channel - Willsenton R8 tube integrated, Holo Audio Spring 3 KTE DAC, audio optimized NUC7i5, Windows 10 Pro/JRiver MC29/Fidelizer Plus 8.7 w/LPS and external SSD drive, PS Audio PerfectWave P3 regenerator, KEF R3 speakers, Rythmik F12SE subwoofer, Audioquest Diamond USB cable, Gabriel Gold IC's, Morrow Audio SP5 speaker cables. Computer - Windows 10/JRiver, Schiit Magni 3+/Modi 3+, Fostex PMO.4n monitors, Sennheiser HD600 headphones -
Originally posted by re510
The reason i'm asking is that i have a mid 90's 5-ch carver and the front right channel has a very slight static buzz sound but only on this channel i did some trial and error and discovered is is the amp and it is only that channel. So my question is what sound does a cold solder usually yield? and can you identify it by looking at the solder joint? and do you have to remove the old solder or just re-heat and apply new. thanks
Taking a stab from my electronics class days. It's basically when the heat applied to the solder isn't enough for it to flow properly. Solder has flux in it which makes it "flow over" the solder joint to join the two surfaces. It needs to reach a certain temp range to properly bond the two surfaces. Usually, NOT always you can see a cold solder joint because it tends to look "duller" or pale in comparison to a reg solder joint which tends to be shiney. However with most older equipment the solder has lost it's shine.
Please other correct me if this is incorrect.
H9"Appreciation of audio is a completely subjective human experience. Measurements can provide a measure of insight, but are no substitute for human judgment. Why are we looking to reduce a subjective experience to objective criteria anyway? The subtleties of music and audio reproduction are for those who appreciate it. Differentiation by numbers is for those who do not".--Nelson Pass Pass Labs XA25 | EE Avant Pre | EE Mini Max Supreme DAC | MIT Shotgun S1 | Pangea AC14SE MKII | Legend L600 | BlueSound Node 3 - Tubes add soul! -
Both answers are correct... good job
When the parts/solder pads the solder is "connecting" to aren't warmed up enough, the solder doesn't properly bond to the surfaces. You can also get a cold solder joint if you jiggle around the parts you're soldering while the solder is cooling down. You get a bad connection, so the resistance between the parts shoots up, and it doesn't take too much to kill the connection and at least make it intermitent (did I spell that correctly), or even break it apart.Brian Knauss
ex-Electrical Engineer for Polk -
I had this problem with my guitar amp [Fender Blues Deville] a couple of years ago. It would cut out intermittently and I couldn't figure it out so I took it to a tech and he said it had cold solder joints. He fixed it by redoing most of the joints and I haven't had a problem with it since. Until then I had never heard of such a thing as cold solder joints. The tech explained it to me the same way that it has been described here.2 Channel:
Amp/Parasound Halo A23
Pre/Carver C-1
Tuner/Carver TX-11a
CDP/Jolida JD 100A
Turntable/AR XB-Shure V15 III -
I've seen a lot of cold solder joints and the guys making them don't even realize they're doing it because no one showed them how to solder properly.
My line of work deals a lot with multiple strand wires using a horizontal twisting of the wires to mate them. The proper way to solder them together is to apply heat to the wires from the bottom until they are so hot that when you touch the solder to the top of the wire it "seaps" right down into and through every strand and pore of the wires. It's the wire that melts the solder, not the soldering iron or gun tip. The solder joint is very complete, strong and shiney.
In a cold solder situation the soldering tip is placed against the top of the wires and solder is touched to the hot tip, melting the solder down and over the wires. The wires are connected but in a very poor manner. Its not complete, not really strong and dull in appearance.
It takes more time and patients to do a hot solder joint than a cold one but it's a far superior solder joint. -
Really? We have to have SPAM in a solder thread!
Nice description from the "shop-boys" above. Electrical shop, wood shop, printing--I slept through almost all of that. I woke up later in Algebra and Science classes. lol But hey, if I didn't have a top notch shop guy doing my repair work in the state capital, I'd be in bad shape.
cnhCurrently orbiting Bowie's Blackstar.!
Polk Lsi-7s, Def Tech 8" sub, HK 3490, HK HD 990 (CDP/DAC), AKG Q701s
[sig. changed on a monthly basis as I rotate in and out of my stash] -
...But hey, if I didn't have a top notch shop guy doing my repair work in the state capital, I'd be in bad shape.
cnh
I love the smell of rosin flux in the morning! ;-)
Seriously, cnh, this stuff is way more fun when one has a little sweat equity in the final product. Way more fun...
I was thinking about this reading through this thread. Soldering is sort of like foreplay - it's not at all difficult to do, but it has to be done properly in order to acheive the intended result!
This probably won't add much to the discussion but I wanted to (re)iterate a couple of points about soldering.
1) Solder provides no substitute for a good, tight, solid mechanical connection! The wires or wire and tie point being soldered need to be in tight physical contact (heh, again, the foreplay analogy may apply...). A pair of needlenose pliers and or hemostats (I am a big fan of the latter) is (are) invaluable.
2) Heat the joint, not the solder (like, oh, wow, man...). No, not that joint; the mechanical joint. Hold the tip of the iron to the joint being soldered and touch the solder to the joint, not to the iron. The hot joint will melt the solder and it will flow and engulf the joint properly. Hot solder "flowing" onto a cold joint will give you a greyish blob of solder that's not well adhered to the joint - that's the qintessence of a cold solder joint.
3) Try to protect the joint from mechanical stress (wiggling/vibration) while it cools. That's the other thing that typically causes a poor solder joint.
4) Use enough heat, but not too much! The modern, variable and temperature-controlled soldering stations are great.
5) for sensitive components - a heat sink is your best friend. That pair of click-lock hemostats I mentioned above can also make a dandy heatsink when soldering a semiconductor.
I'll bet there are YouTube tutorials on how to solder (probably on foreplay too, come to think of it...). The little photos and instructions that can be found in the front of every old Heathkit or EICO kit instruction manual are good too. -
Great post mhardy
I had a few chuckles.
-
:-P I realized I could've gone even further down the "foreplay" road... but even I have some scruples.
Oh, and speaking of soldering and of Foreplay (in the hifi context, of course)...
http://www.bottlehead.com/store.php?crn=220&rn=430&action=show_detail -
Those are beautiful amps! What is the power rating?
Actually I do own a soldering iron and have even used it once or twice in "desperation". Unfortunately, every time I break it out I probably need a Valium because I "SO" expect to F-up whatever I'm trying to fix! lol I find it to be unbearably "stressful".
It's kind of like people who think working on a car engine is "relaxing": I don't get that either. Now, painting, drawing, writing, playing a musical instrument, working on a film or video, I can understand.
cnhCurrently orbiting Bowie's Blackstar.!
Polk Lsi-7s, Def Tech 8" sub, HK 3490, HK HD 990 (CDP/DAC), AKG Q701s
[sig. changed on a monthly basis as I rotate in and out of my stash] -
+1 on the first part, will add gardening to the second part.humpty dumpty was pushed
-
Those are beautiful amps! What is the power rating?
Actually I do own a soldering iron and have even used it once or twice in "desperation". Unfortunately, every time I break it out I probably need a Valium because I "SO" expect to F-up whatever I'm trying to fix! lol I find it to be unbearably "stressful".
It's kind of like people who think working on a car engine is "relaxing": I don't get that either. Now, painting, drawing, writing, playing a musical instrument, working on a film or video, I can understand.
cnh
When you're more ambulatory... get yer butt down to MA later this summer and we'll do some DIY or a rehab!
Come on a Saturday before 2pm and we can do a dump junket. -
That's a very generous offer there, Mark, and I might just take you up on that as soon as I get a better idea of how much longer my surgeon wants me to crutch around with this Darth Vader boot on my left leg. lol
It would also give me a chance to visit my son in Boston. He did come up just after the surgery to check me out for a few days after my wife left for three weeks in China (work related)!
Thanks!
cnhCurrently orbiting Bowie's Blackstar.!
Polk Lsi-7s, Def Tech 8" sub, HK 3490, HK HD 990 (CDP/DAC), AKG Q701s
[sig. changed on a monthly basis as I rotate in and out of my stash] -
Ayuh. Yah can get ta Boston from heah ;-)
-
Hell, I was just gonna say; A solder joint that's had time to cool off...
-
Thanks to teh webs, here's an OK if somewhat goofy tutorial on PCB soldering from the wonderful folks at Make magazine.
http://blog.makezine.com/2007/01/05/soldering-tutorial-pdf/
... and, by brute force, I've attached a quick semi-pictorial guide to PCB soldering from a Heathkit manual.
Here's a helpful - I hope - description and graphic on point to point soldering from an EICO manual (courtesy of the EICO Yahoo group): -
mhardy6647 wrote: »I love the smell of rosin flux in the morning! ;-)
Seriously, cnh, this stuff is way more fun when one has a little sweat equity in the final product. Way more fun...
I was thinking about this reading through this thread. Soldering is sort of like foreplay - it's not at all difficult to do, but it has to be done properly in order to acheive the intended result!
This probably won't add much to the discussion but I wanted to (re)iterate a couple of points about soldering.
1) Solder provides no substitute for a good, tight, solid mechanical connection! The wires or wire and tie point being soldered need to be in tight physical contact (heh, again, the foreplay analogy may apply...). A pair of needlenose pliers and or hemostats (I am a big fan of the latter) is (are) invaluable.
2) Heat the joint, not the solder (like, oh, wow, man...). No, not that joint; the mechanical joint. Hold the tip of the iron to the joint being soldered and touch the solder to the joint, not to the iron. The hot joint will melt the solder and it will flow and engulf the joint properly. Hot solder "flowing" onto a cold joint will give you a greyish blob of solder that's not well adhered to the joint - that's the qintessence of a cold solder joint.
3) Try to protect the joint from mechanical stress (wiggling/vibration) while it cools. That's the other thing that typically causes a poor solder joint.
4) Use enough heat, but not too much! The modern, variable and temperature-controlled soldering stations are great.
5) for sensitive components - a heat sink is your best friend. That pair of click-lock hemostats I mentioned above can also make a dandy heatsink when soldering a semiconductor.
I'll bet there are YouTube tutorials on how to solder (probably on foreplay too, come to think of it...). The little photos and instructions that can be found in the front of every old Heathkit or EICO kit instruction manual are good too.
I was just browsing for relevant posts for my project and I happened to stumble upon yours. Thanks for the useful points!
george -
The reason i'm asking is that i have a mid 90's 5-ch carver and the front right channel has a very slight static buzz sound but only on this channel i did some trial and error and discovered is is the amp and it is only that channel. So my question is what sound does a cold solder usually yield? and can you identify it by looking at the solder joint? and do you have to remove the old solder or just re-heat and apply new. thanks
It is simply a saying for a bad solder connection. As in one that has air bubbles inside of the outer layer, or a poor connection where the solder didn't flow into the joint.
george -
This is a cold solder joint...Make it simple...Make it better!
-
Reported- Not Tom ::::::: Any system can play Diana Krall. Only the best can play Limp Bizkit.