Teac X-1000r R2R Adventures

SCompRacer
Posts: 8,520
Cue the bells and whistles...most Teac guys claim the X1000r was made much better than the X2000r. Black ones are way cool but the black VU meters are harder to see.
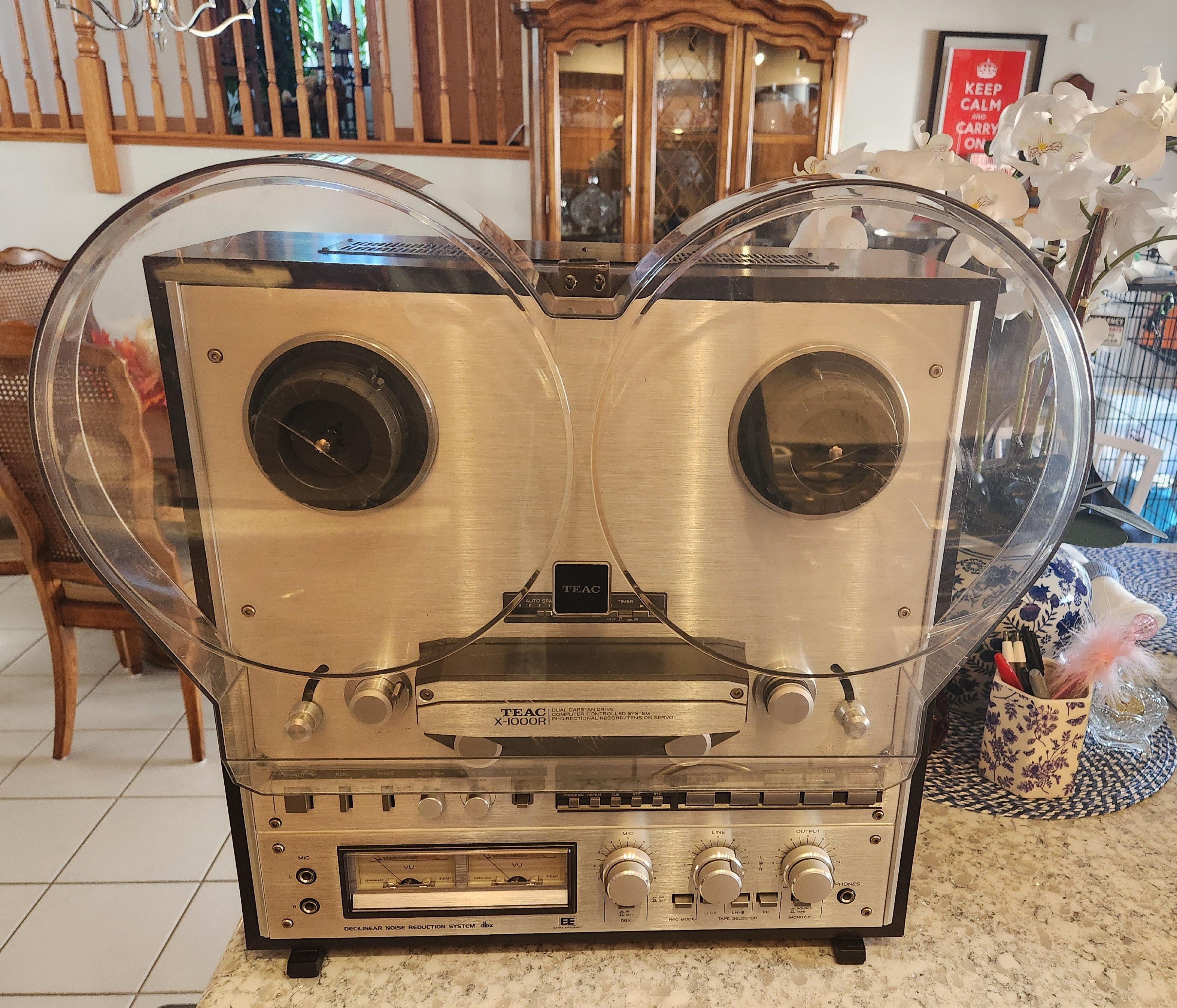
I’m getting braver. Teac X-1000r. Near excellent condition, heads have some wear but far from wore out. One weakness of these decks is the capstan motor, EM1446. Teac went to DC motors in the X series. That means brushes and commutators. When the brushes get thin, you may lose brush tension and the brush doesn’t touch the commutator. It also means if your belt gets gooey and the capstan motor freezes, the motor burns out. One of my fav ebay ads read “Teac X1000 purchased in estate sale. We plugged it in and pressed play and smoke came out of vents….still in excellent condition but needs work.”
Pioneer 901/909 used the same motor, but Pioneer added a sensing circuit that protects the motor in a high amperage condition. Teac may have said, we saved a few bucks not adding that circuitry, so you just may have to buy yourself a motor.
The new capstan motor supply was exhausted ~ 2021. Only used are available for big money, ~ $250-$350+. Most being in the ‘like a box of chocolates, you never know what you're gonna get’ category. (Although one reputable seller opens them up to show brushes and provides scope pattern of tachometer). He is in the higher price range but less of a gamble.
If you’re handy, and brave, unstable, you can get brushes that are close in size, file the ends flat and conductive epoxy them in. Size is ~ 3mm x 3mm x 4mm.
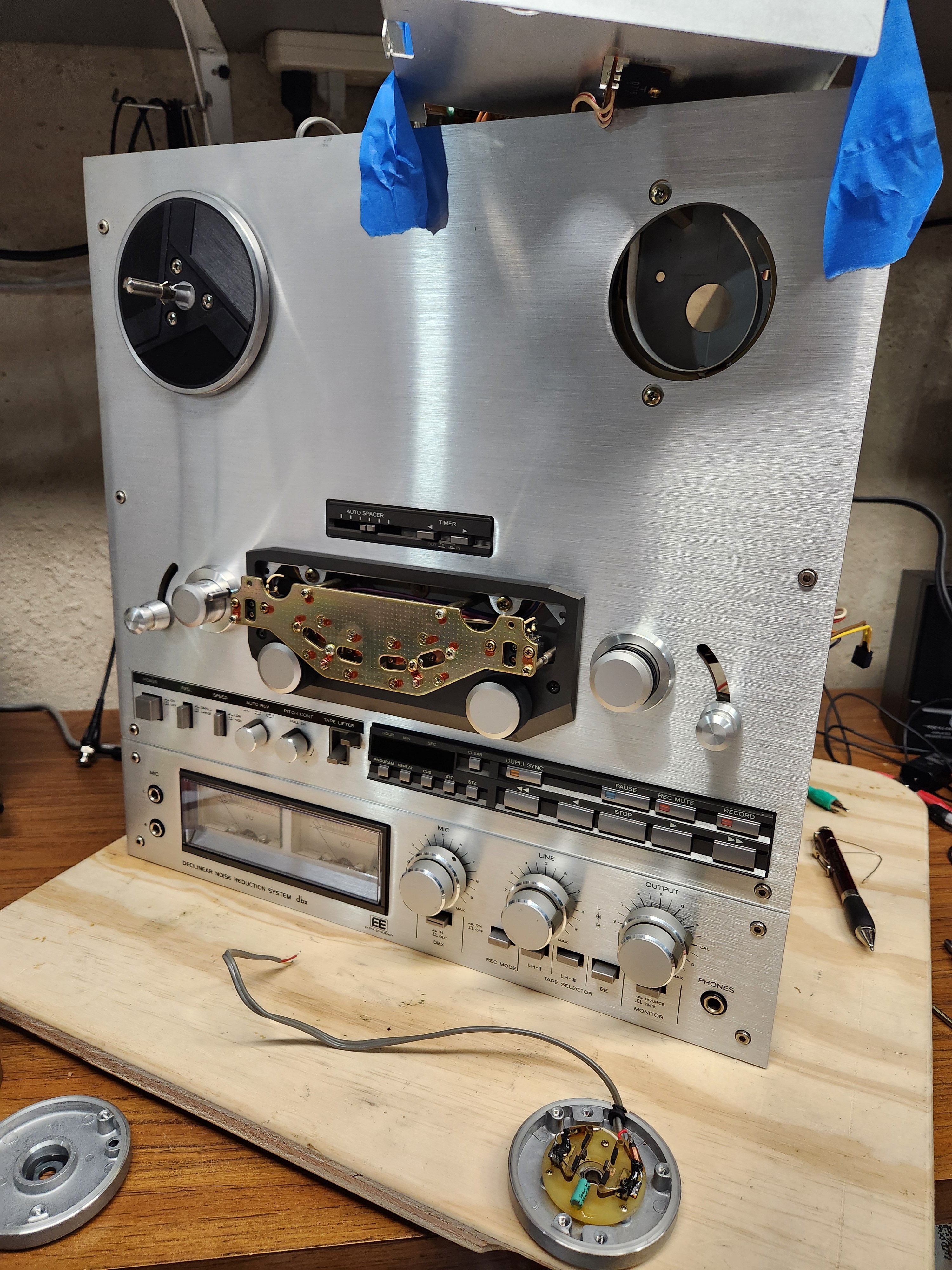
Did I mention these were small motors?
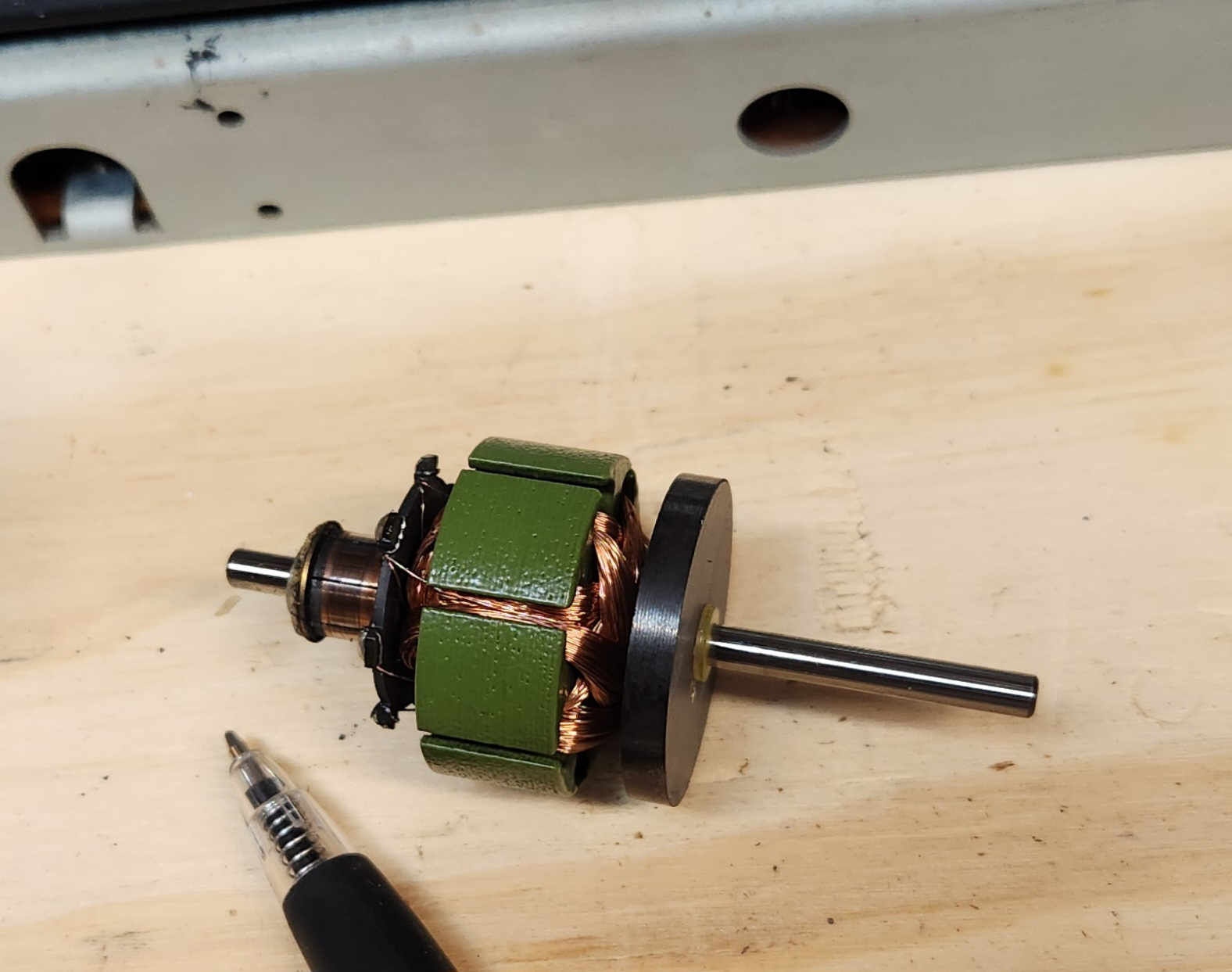
The old paper clip trick. If you pull armature out without spreading brushes, you will bend/destroy the brushes/holders. Maybe the plastic nubs too. You must remove brush end and armature in one piece.
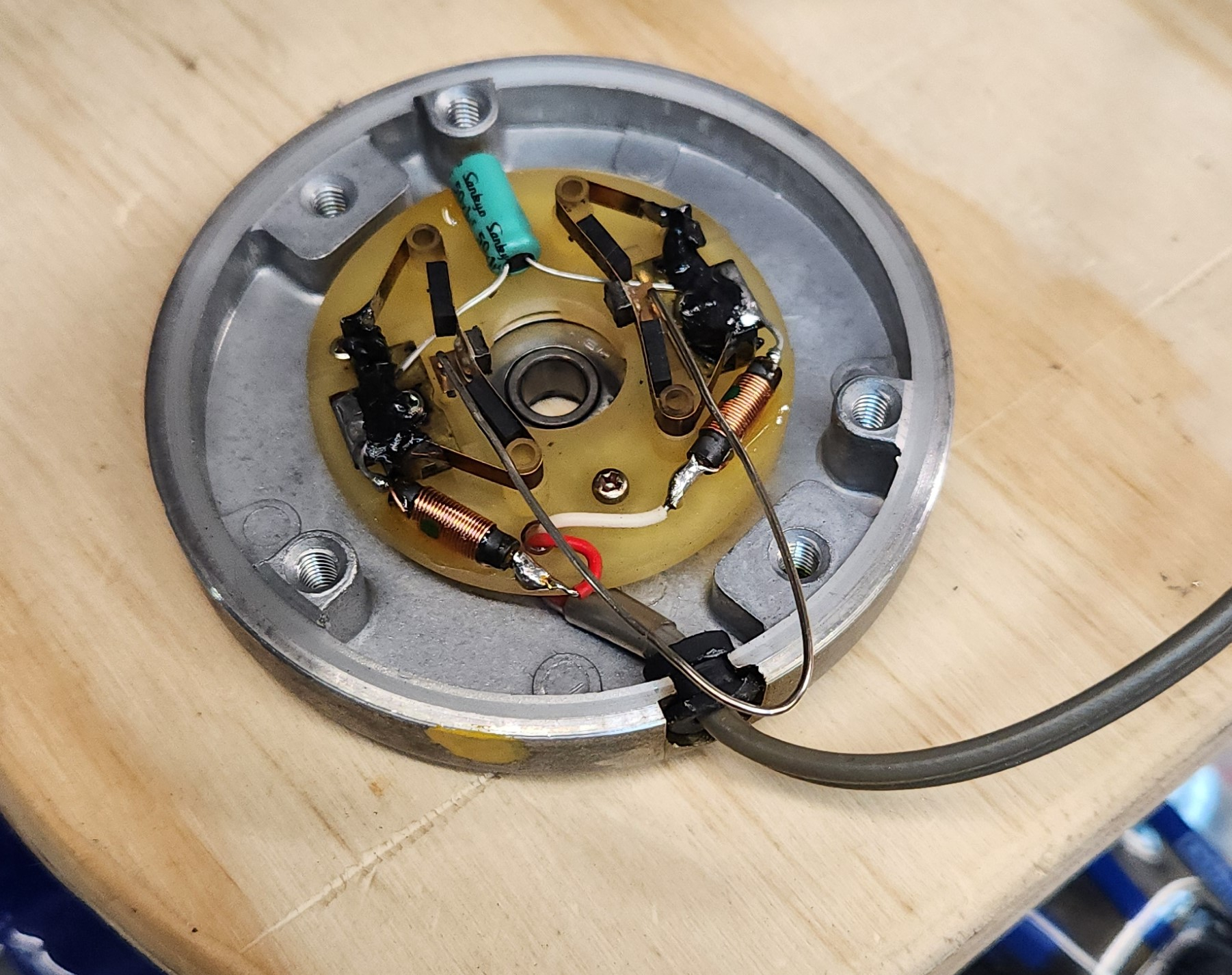
One brush little thinner than the other. The bottom is thinner, taper wear.
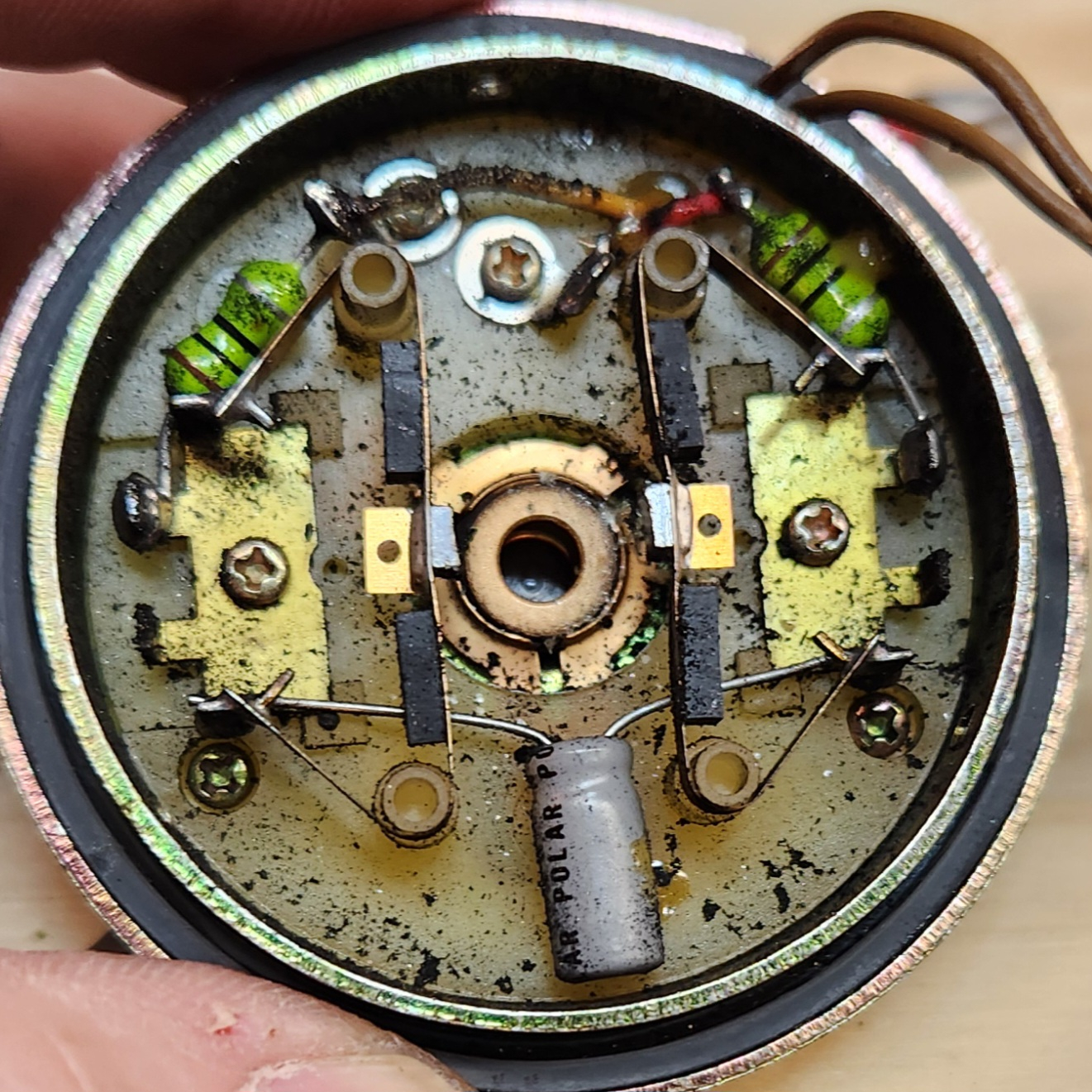
Trying an acetone soak but that is cured epoxy.
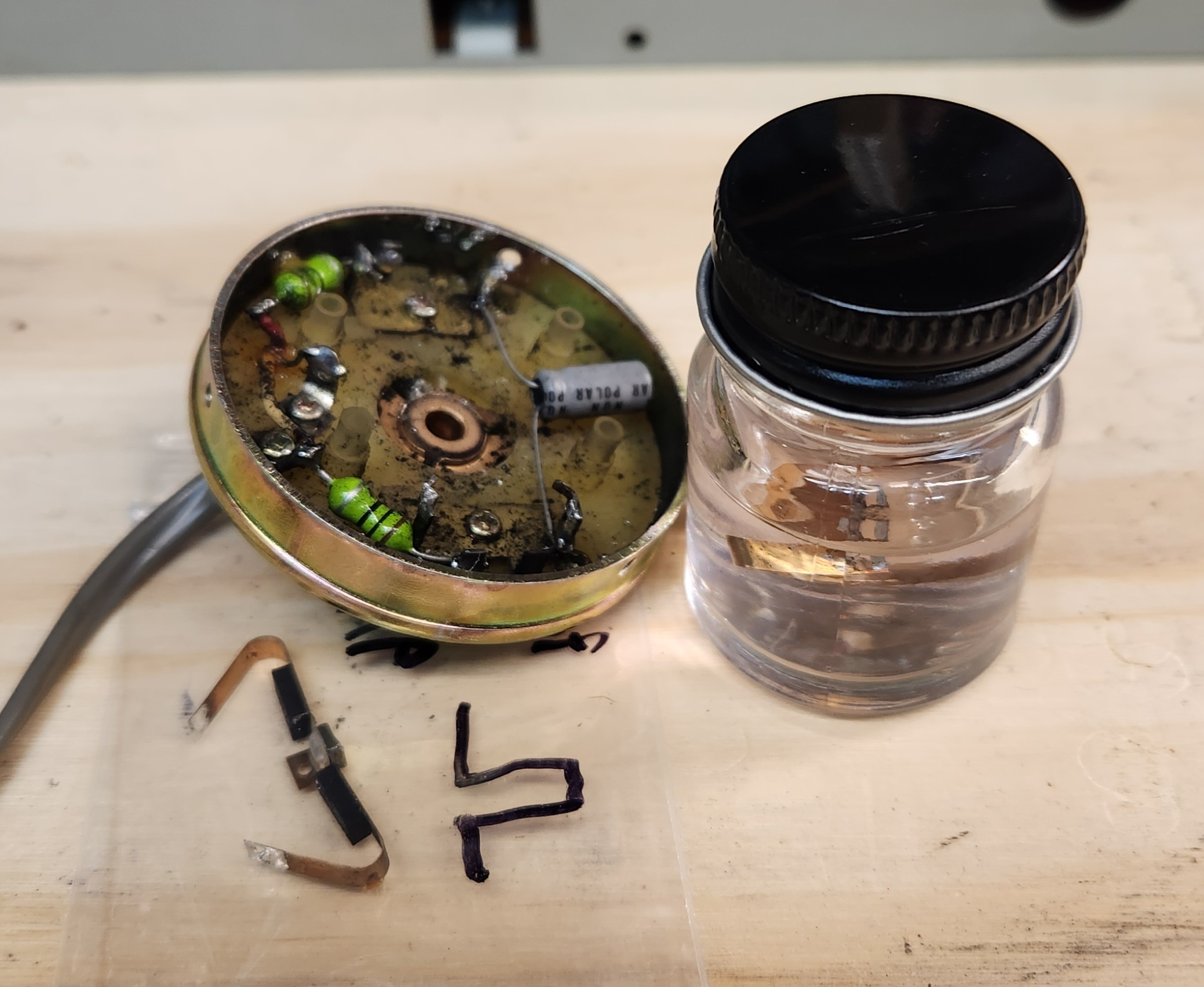
Take a look at the reel motor brushes. They are like new. The only reason I can think of for the worn capstan brushes is 1) motor was replaced. 2) Leaving the unit powered on, not playing a tape but the tape tension is holding the R and L tension arms up. With tension arms up, the capstan motor runs, even when tape not playing. Add some slack in tape, tension arms fall, capstan motor does not run.
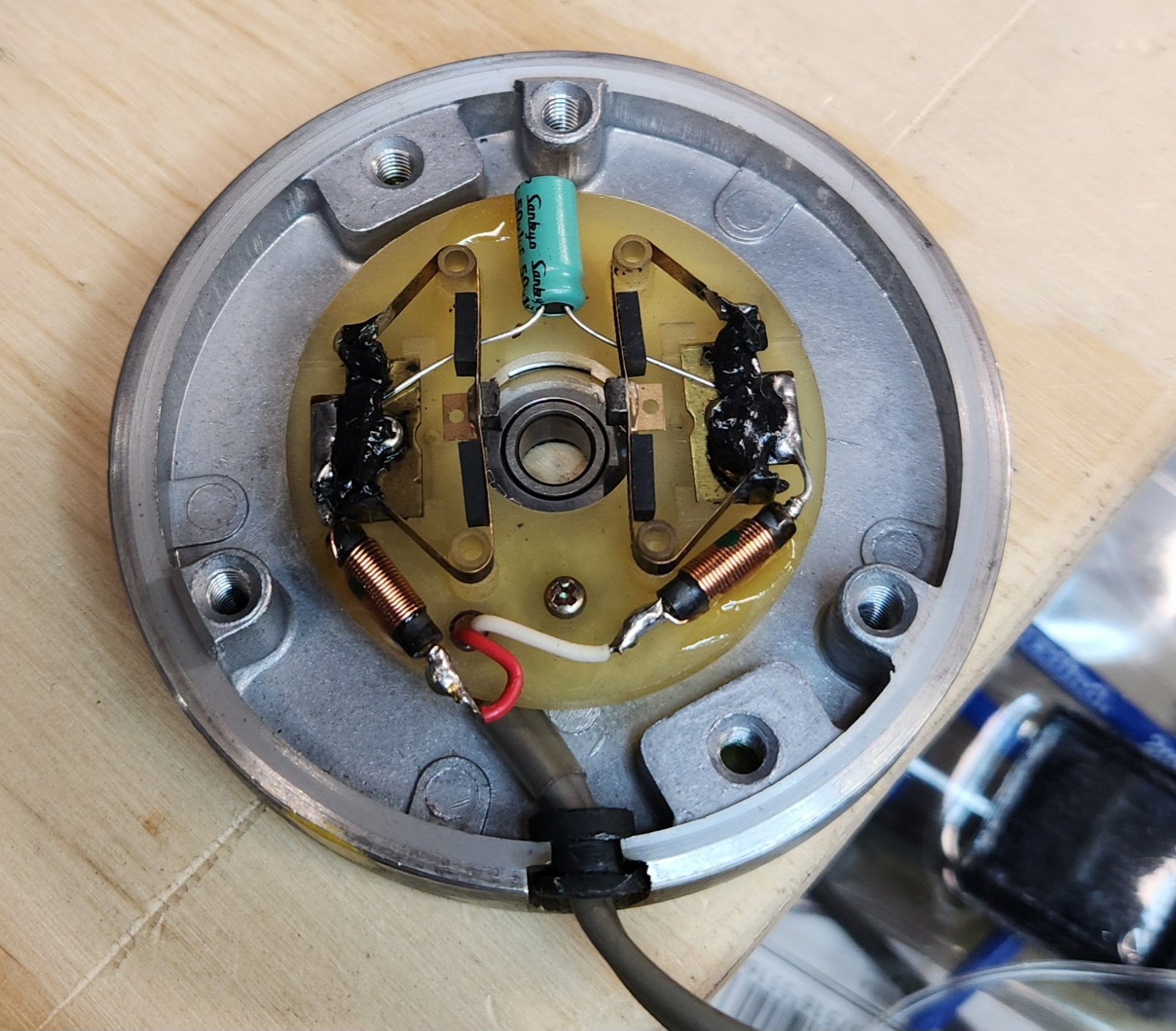
Oh look, two more to do! Me and two lucky? friends are going be the three Teac amigos.
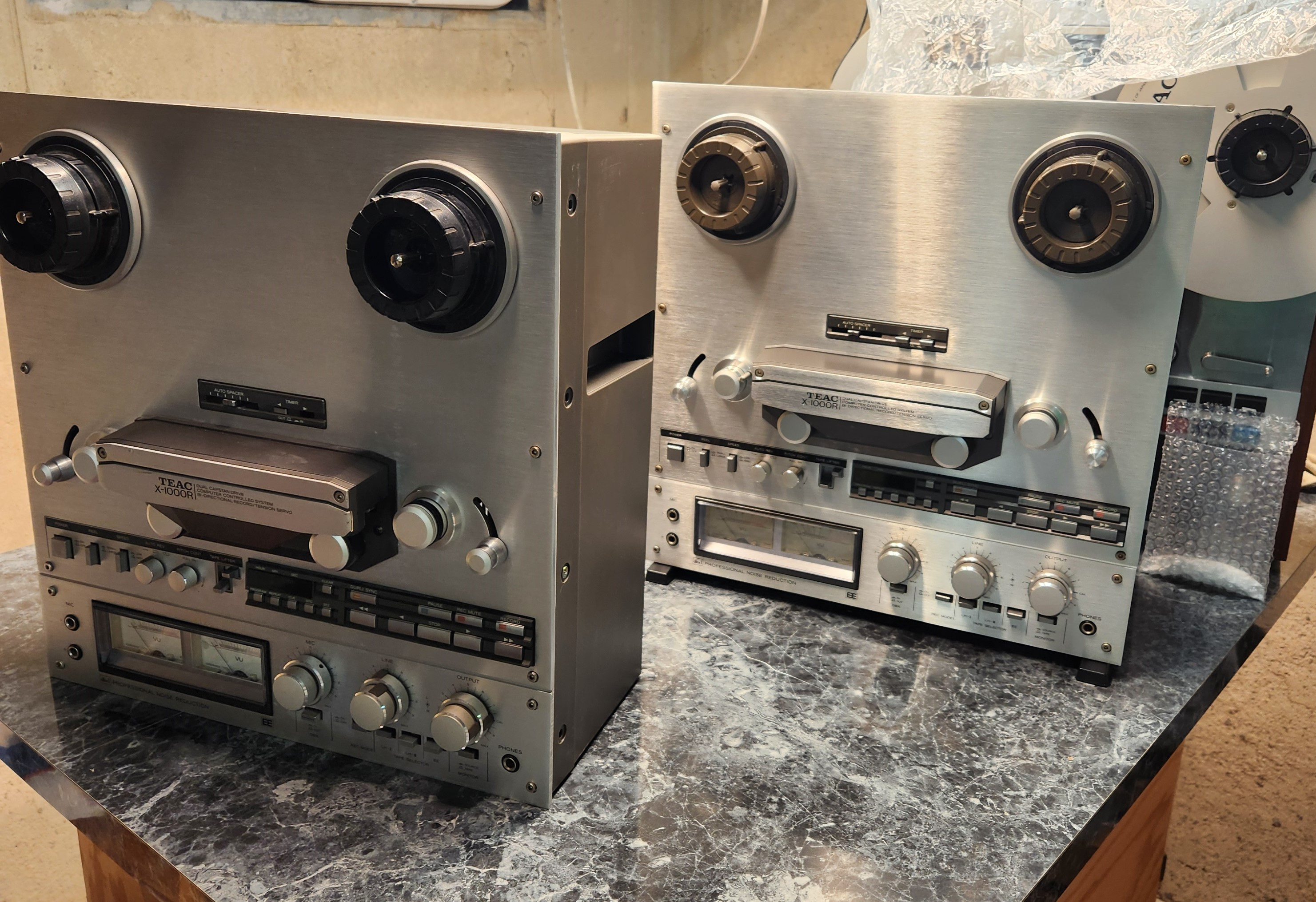
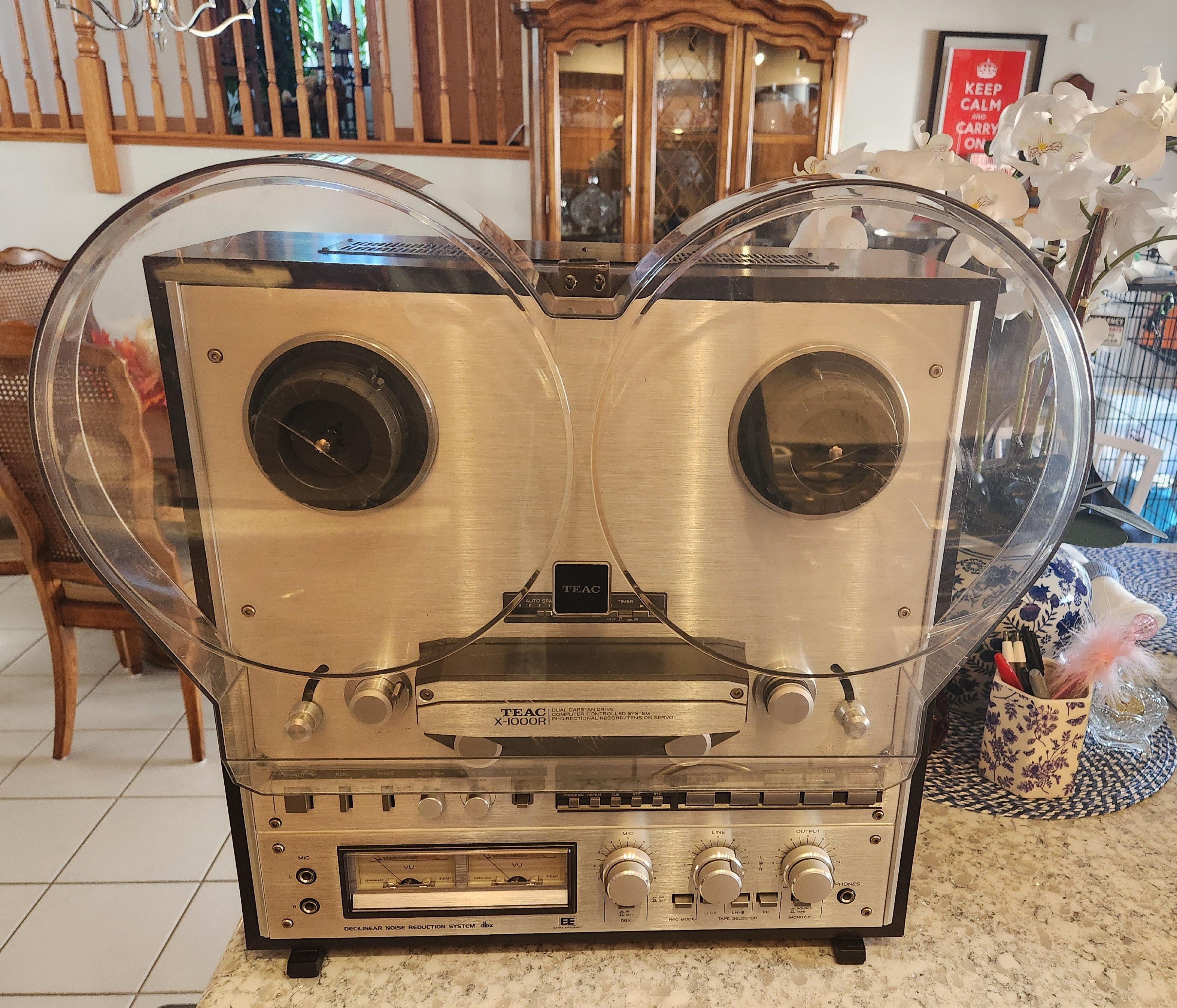
I’m getting braver. Teac X-1000r. Near excellent condition, heads have some wear but far from wore out. One weakness of these decks is the capstan motor, EM1446. Teac went to DC motors in the X series. That means brushes and commutators. When the brushes get thin, you may lose brush tension and the brush doesn’t touch the commutator. It also means if your belt gets gooey and the capstan motor freezes, the motor burns out. One of my fav ebay ads read “Teac X1000 purchased in estate sale. We plugged it in and pressed play and smoke came out of vents….still in excellent condition but needs work.”
Pioneer 901/909 used the same motor, but Pioneer added a sensing circuit that protects the motor in a high amperage condition. Teac may have said, we saved a few bucks not adding that circuitry, so you just may have to buy yourself a motor.
The new capstan motor supply was exhausted ~ 2021. Only used are available for big money, ~ $250-$350+. Most being in the ‘like a box of chocolates, you never know what you're gonna get’ category. (Although one reputable seller opens them up to show brushes and provides scope pattern of tachometer). He is in the higher price range but less of a gamble.
If you’re handy, and brave, unstable, you can get brushes that are close in size, file the ends flat and conductive epoxy them in. Size is ~ 3mm x 3mm x 4mm.
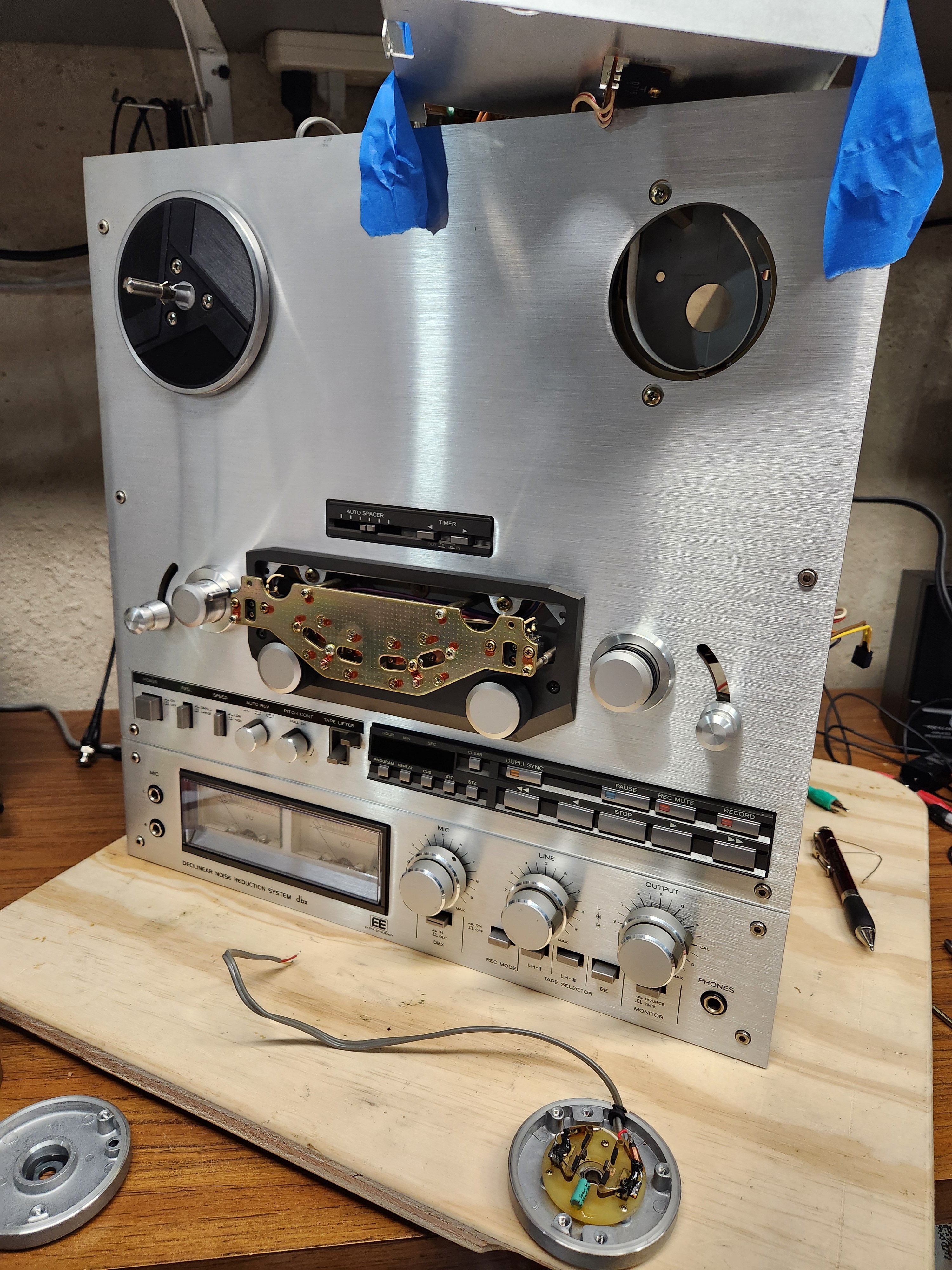
Did I mention these were small motors?
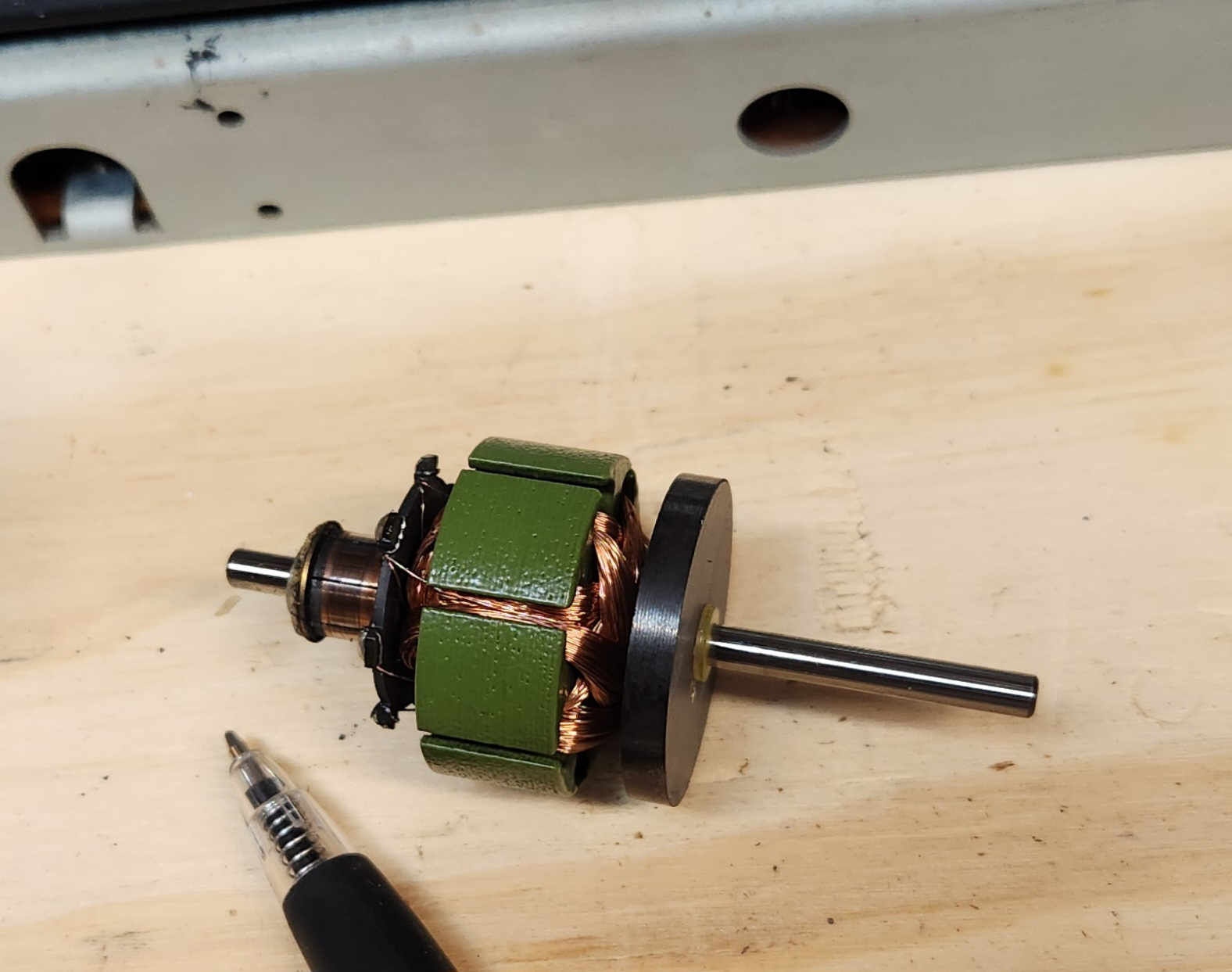
The old paper clip trick. If you pull armature out without spreading brushes, you will bend/destroy the brushes/holders. Maybe the plastic nubs too. You must remove brush end and armature in one piece.
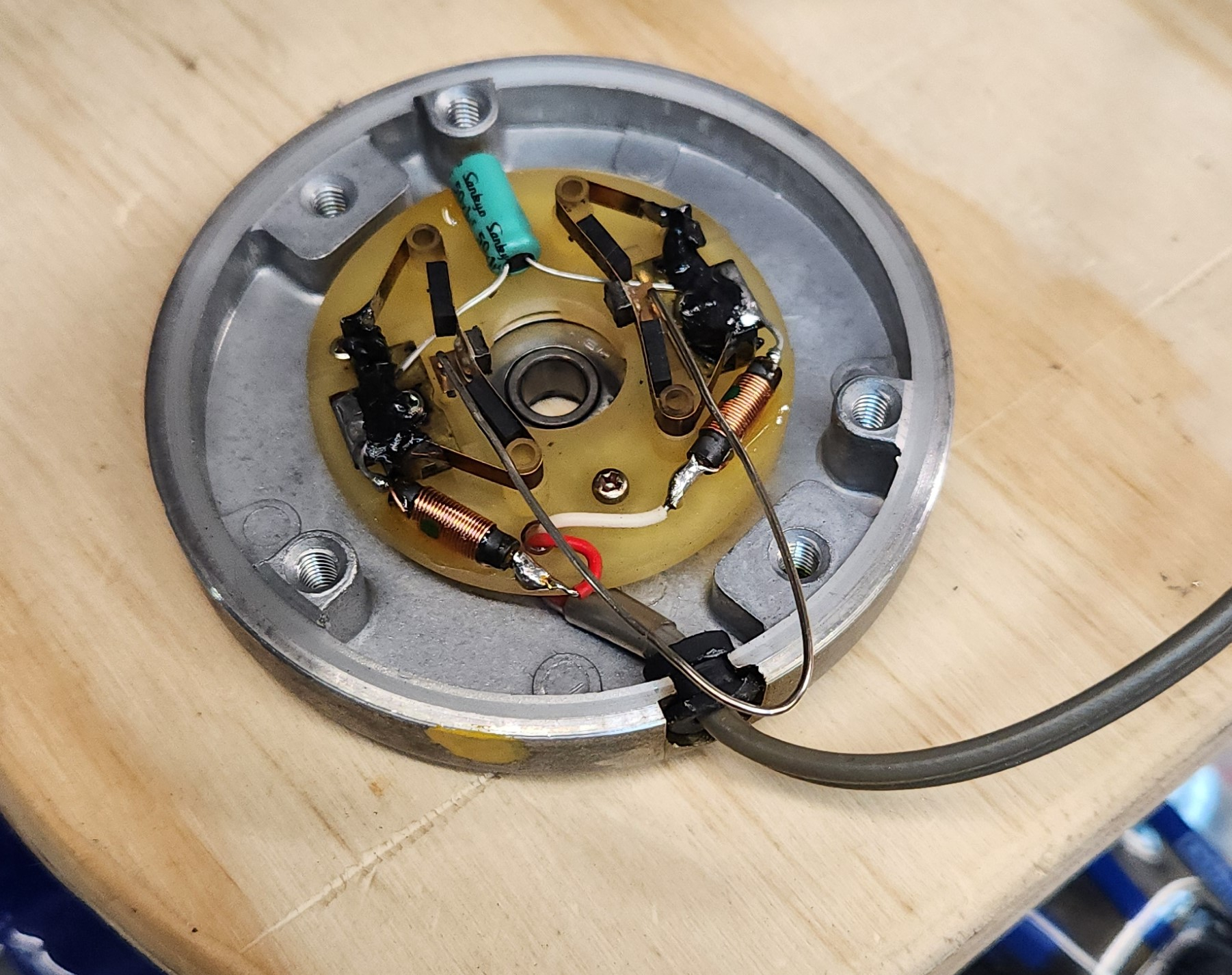
One brush little thinner than the other. The bottom is thinner, taper wear.
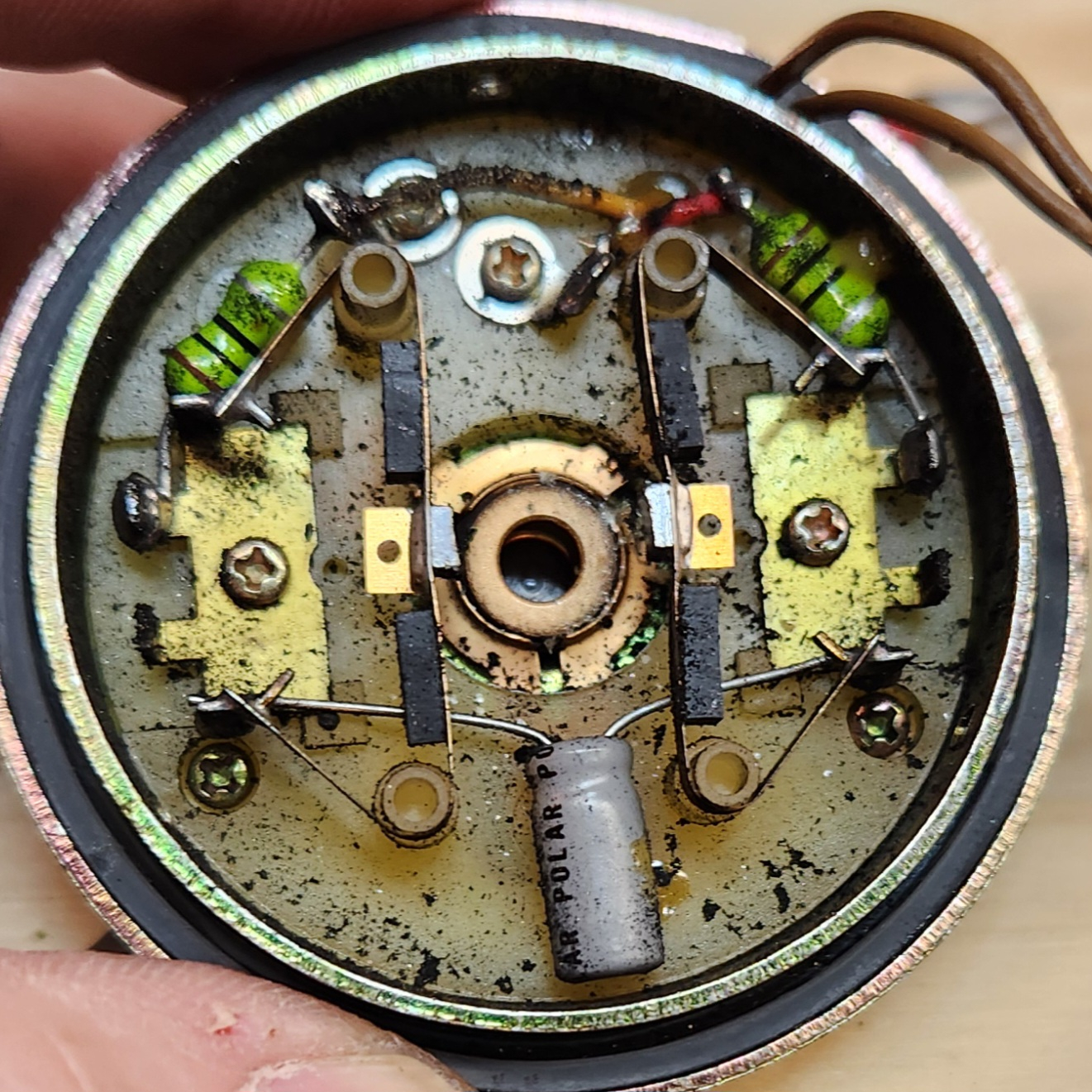
Trying an acetone soak but that is cured epoxy.
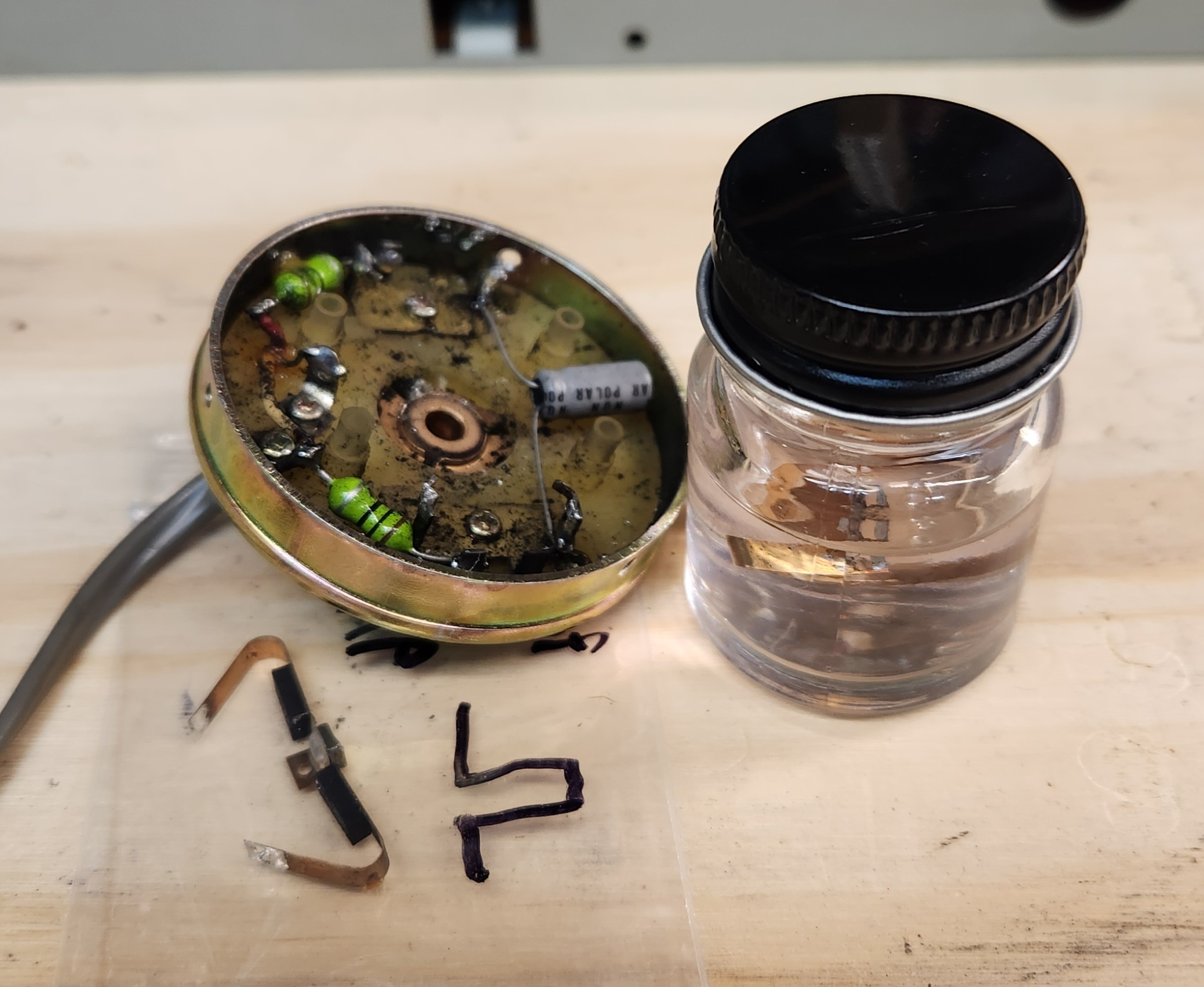
Take a look at the reel motor brushes. They are like new. The only reason I can think of for the worn capstan brushes is 1) motor was replaced. 2) Leaving the unit powered on, not playing a tape but the tape tension is holding the R and L tension arms up. With tension arms up, the capstan motor runs, even when tape not playing. Add some slack in tape, tension arms fall, capstan motor does not run.
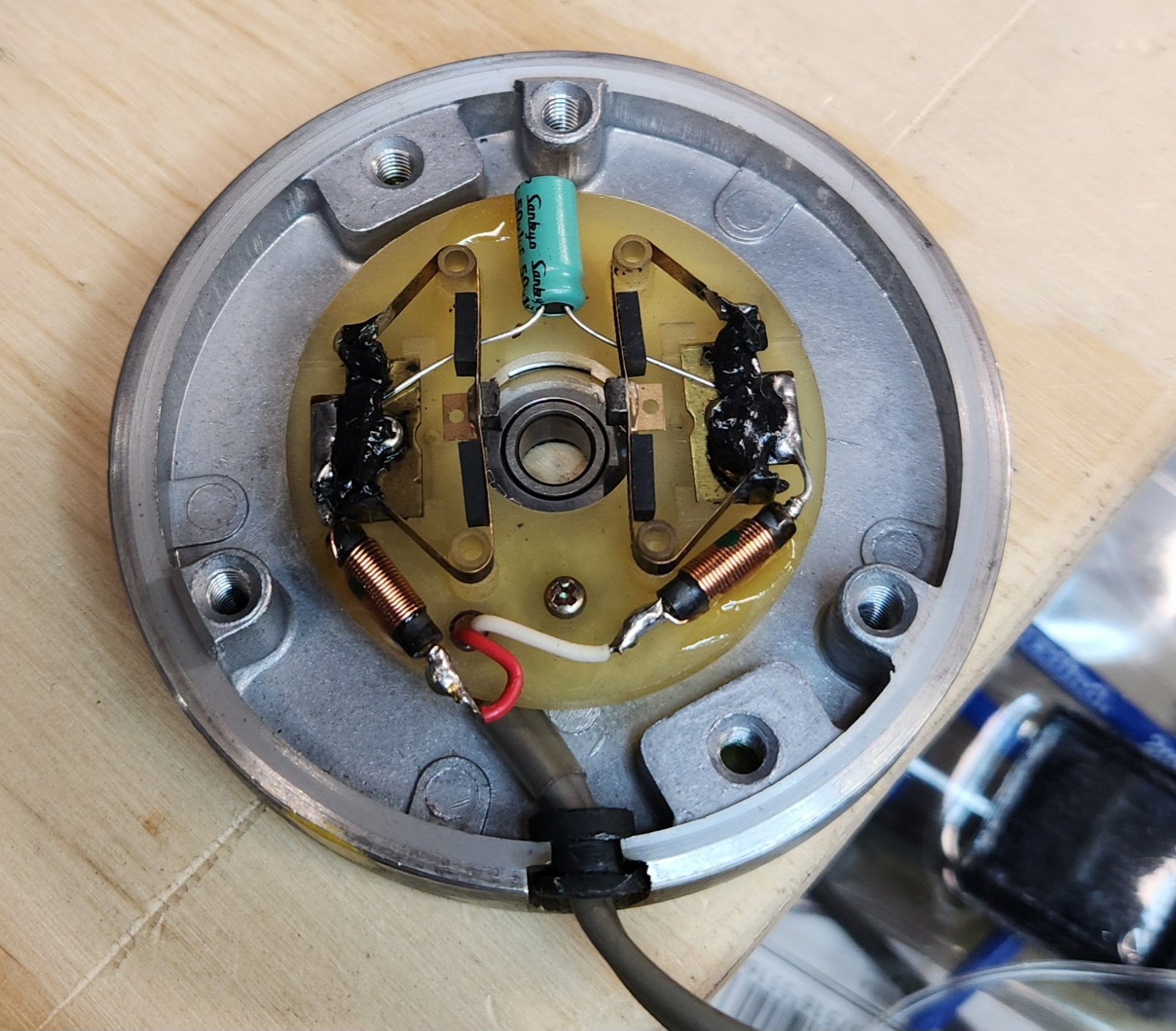
Oh look, two more to do! Me and two lucky? friends are going be the three Teac amigos.
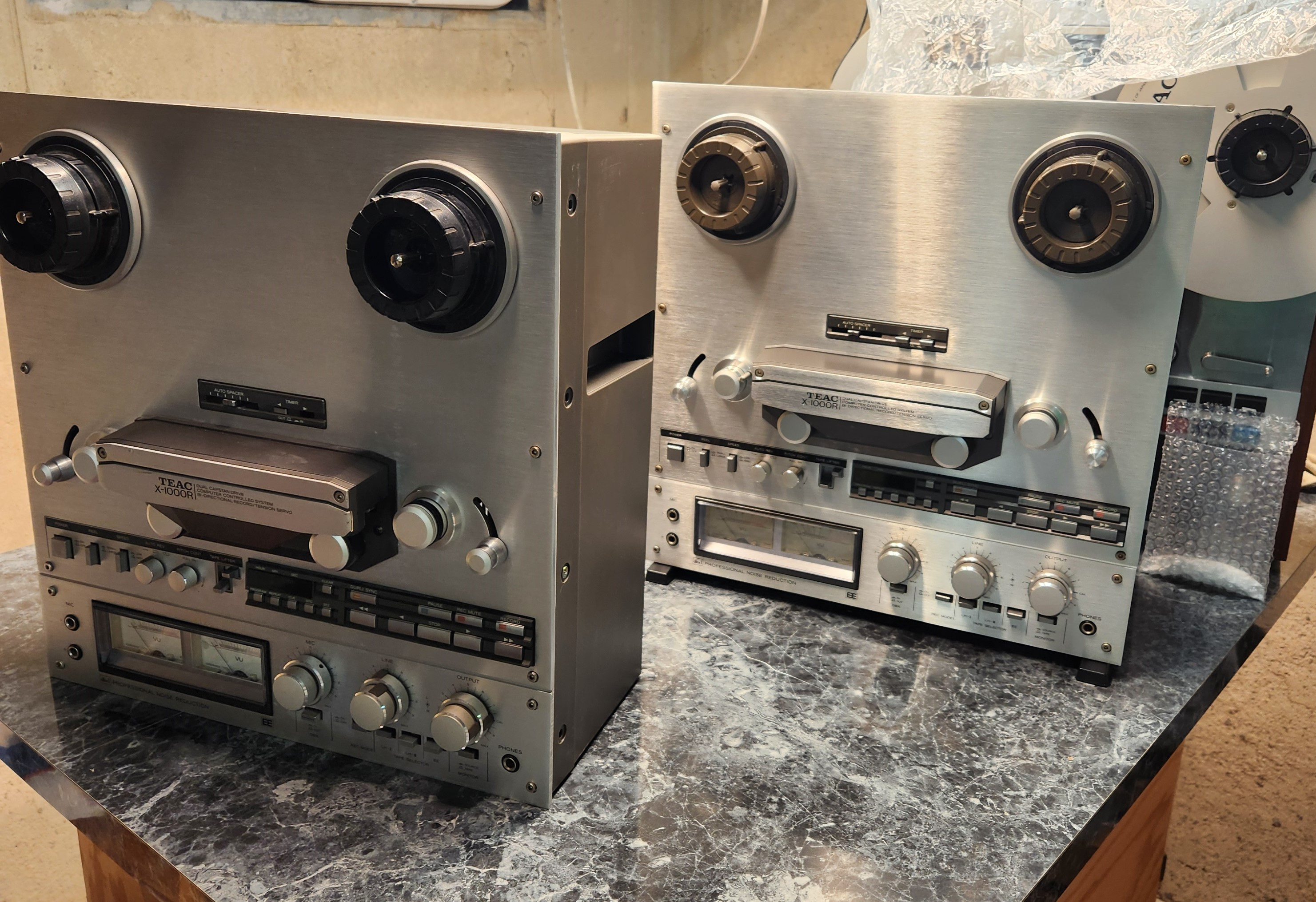
Salk SoundScape 8's * Audio Research Reference 3 * Bottlehead Eros Phono * Park's Audio Budgie SUT * Krell KSA-250 * Harmonic Technology Pro 9+ * Signature Series Sonore Music Server w/Deux PS * Roon * Gustard R26 DAC / Singxer SU-6 DDC * Heavy Plinth Lenco L75 Idler Drive * AA MG-1 Linear Air Bearing Arm * AT33PTG/II & Denon 103R * Richard Gray 600S * NHT B-12d subs * GIK Acoustic Treatments * Sennheiser HD650 *
Comments
-
Brushes and small non-polar caps ordered for motors.
It's always interesting to see what went on inside used gear that saw service.
Power set to Japan, 100V instead of 117.
Belt replacement requires removing capstan motor bracket. They missed getting the timer switch mounting nubs in the top of capstan motor bracket. The mounting screws above it are not accessible with circuit boards mounted in place on rear of deck.
This resulted in breaking one of the two timer switches.
It's best to remove the entire assembly to properly clean and lube the pinch roller linkage. Easier to clean all the tape path and heads too. The head assembly is mounted on fixed posts so the head height/azimuth adjustments remain unmolested.
You can also remove any goo belt remnants obscured by components left installed. This stuff is like the gift that keeps on giving. Get it on your fingers or step on it and you'll leave a mark on everything you touch or every step you take.
Yeah, I mark everything even if it's obvious the R and L pinch roller arms are not interchangeable. ....
A missing washer. You can tell by the grease mark one was missing. I'll be searching to make sure it isn't inside somewhere.
This is the solenoid actuator linkage at rear between the capstan flywheels. Hard to access that installed. Sharp eyes will notice the R and L capstan flywheels are different, so I take pictures, mark everything. I have not reached the familiarity breeds contempt stage with the X-1000r yet.
Salk SoundScape 8's * Audio Research Reference 3 * Bottlehead Eros Phono * Park's Audio Budgie SUT * Krell KSA-250 * Harmonic Technology Pro 9+ * Signature Series Sonore Music Server w/Deux PS * Roon * Gustard R26 DAC / Singxer SU-6 DDC * Heavy Plinth Lenco L75 Idler Drive * AA MG-1 Linear Air Bearing Arm * AT33PTG/II & Denon 103R * Richard Gray 600S * NHT B-12d subs * GIK Acoustic Treatments * Sennheiser HD650 * -
Had an issue with the fast rewind switch, had to wiggle it to work. Removed front panel, seemed easiet with everything else off it.
Common issues I'm told. Simple easily obtainable momentary contact switches. Beats a $75 used panel.
Look what I found. The missing pinch roller linkage washer.
Salk SoundScape 8's * Audio Research Reference 3 * Bottlehead Eros Phono * Park's Audio Budgie SUT * Krell KSA-250 * Harmonic Technology Pro 9+ * Signature Series Sonore Music Server w/Deux PS * Roon * Gustard R26 DAC / Singxer SU-6 DDC * Heavy Plinth Lenco L75 Idler Drive * AA MG-1 Linear Air Bearing Arm * AT33PTG/II & Denon 103R * Richard Gray 600S * NHT B-12d subs * GIK Acoustic Treatments * Sennheiser HD650 * -
"..every step you take." Isn't that a Police song? Nice work! A Teac master mechanic!
-
Yes, I was channeling some Police there!
You are kind of responsible for this madness.
Another common issue is a spring in the left tape guide roller gets mangled and/or broken. The spring creates a path to ground when a metal sensing foil completes the circuit between the sensing post and roller guide. That triggers reverse play mode, the "r" in X-1000r.
This is what it should look like.
Two of the three decks had mangled springs. I straightened them. They are sold with the roller on ebay for $25 and up, typically with bent spring.
The manual shows the loop around the axle but some argue it rests against it. When you remove the roller retainer, I think the spring snaps off the axle and ends up touching the edge of axle. The nylon washer goes over the spring, then the roller retainer. At 2 o'clock is the sensing post.
What you don't want is the spring getting caught between the retainer and axle. All you have to do to confirm correct assembly is spin the tape guide roller. No spin, fix it.
Salk SoundScape 8's * Audio Research Reference 3 * Bottlehead Eros Phono * Park's Audio Budgie SUT * Krell KSA-250 * Harmonic Technology Pro 9+ * Signature Series Sonore Music Server w/Deux PS * Roon * Gustard R26 DAC / Singxer SU-6 DDC * Heavy Plinth Lenco L75 Idler Drive * AA MG-1 Linear Air Bearing Arm * AT33PTG/II & Denon 103R * Richard Gray 600S * NHT B-12d subs * GIK Acoustic Treatments * Sennheiser HD650 * -
You've been busy, Rich!Jay
SDA 2BTL * Musical Fidelity A5cr amp * Oppo BDP-93 * Modded Adcom GDA-600 DAC * Rythmik F8 (x2)
Micro Seiki DQ-50 * Hagerman Cornet 2 Phono * A hodgepodge of cabling * Belkin PF60
Preamp rotation: Krell KSL (SCompRacer recapped) * Manley Shrimp * PS Audio 5.0 -
My brain was turning to mush so I figured better start using it again.
While waiting for parts I decided to lap the heads. They had some wear but were in lapping range. If you got deep pockets you can try for some NOS. New record heads are around $80, while play heads are $200-250. The 1000r records and plays in reverse so that's two of each. Used can be in worse condition than the ones you have.
Lapping requires a steady pressure while dragging and turning the head on sandpaper on a flat surface to remove material along the entire contour. A chunk of wood with an old broom handle across a sink to give some angle. Running water is best to flush sanding debris off paper. I didn't have any glass so I used a chunk of granite.
400, 800 and 1500 wet/dry paper is used. Take only enough material to make the tape groove disappear. All four took less than an hour. I check progress often with a lighted magnifier.
I was free handing but remembered this angle aluminum I had. A little grease on it helps lubricate the thick mounting side of head while dragging against it.
Heads slightly worn. Would still play OK but when calibrating and adjusting azimuth, you want a smooth surface for the tape.
The record head on left is finish lapped and just needs polishing. You can see it still has a contour, no flat spots. The one on right is up next. I didn't have any finish lapping cloth so used some Mothers Aluminum polish instead.
Since the heads were removed from their mounting brackets, the height and azimuth screws were untouched. Head align looks pretty good. Before assembly, I'll attach it with screws and ensure the coarse adjustment is all good.
Salk SoundScape 8's * Audio Research Reference 3 * Bottlehead Eros Phono * Park's Audio Budgie SUT * Krell KSA-250 * Harmonic Technology Pro 9+ * Signature Series Sonore Music Server w/Deux PS * Roon * Gustard R26 DAC / Singxer SU-6 DDC * Heavy Plinth Lenco L75 Idler Drive * AA MG-1 Linear Air Bearing Arm * AT33PTG/II & Denon 103R * Richard Gray 600S * NHT B-12d subs * GIK Acoustic Treatments * Sennheiser HD650 * -
Still await brushes. I cobbled together a way to remove the old brushes while protecting the fragile strap it is attached to.
A piece of scrap lumber. Drill hole size of brush. Cut a washer up and smooth rough edges. Drill hole in washer for screw. Use a shim under washer thickness of strap.
A lighted magnifier helps. I soaked the assembly in acetone for a couple days. It was well cured epoxy and the acetone didn't seem to help at first but it may have softened it. I carefully scaped epoxy with a sharp Exacto knife.
No collateral damage!
Salk SoundScape 8's * Audio Research Reference 3 * Bottlehead Eros Phono * Park's Audio Budgie SUT * Krell KSA-250 * Harmonic Technology Pro 9+ * Signature Series Sonore Music Server w/Deux PS * Roon * Gustard R26 DAC / Singxer SU-6 DDC * Heavy Plinth Lenco L75 Idler Drive * AA MG-1 Linear Air Bearing Arm * AT33PTG/II & Denon 103R * Richard Gray 600S * NHT B-12d subs * GIK Acoustic Treatments * Sennheiser HD650 * -
That's really clever, Rich!
-
Thanks Ken!
More progress. 1uf 50v Bipolar caps arrived for the reel motors. They were only 20% out while the capstan was 40% out spec. Inductors tested good. Good brushes, sealed ball bearings smooth, all good.
Cleaned up commutators, reassembled both reel motors and tested. 12v .07 amp no load is good.
A little finger pressure and amps increase. These little motors have some torque. I had it a little over an amp and got a hot spot on the finger from the motor shaft.
Got the tactile switches. I provided part number to maybe help someone else. IMO it is risky purchasing a used control panel that could have same issue. The momentary switches were $.12 each, $1.80 for fifteen. A used panel can set you back $68. Yes, it's a process but the Hakko desoldering gun made it easy. I ordered 45 in case the other two decks need them.
A little smaller footprint but height and terminal spacing are correct.
One new switch installed by the 4" mark. If too high switches will be held in ON. The old ones measured between 4.75 and 5mm tall off PCB. I measured 5.56mm from switch actuator to PCB.
All in. Double checked all terminals that had a trace were soldered in and all switches against PCB. Not all terminals are soldered and the replacements do not have a fifth locating leg. Some of the old switches had pads for the locating tabs and were soldered. I wondered if it was for ESD ground, but the pads have no continuity to ground. No LED's suffered collateral damage.
I tested all these switches before installing and after installed. Clipped ohm meter to power side of switches and pushed every button to ensure full open and good closed numbers. Some buttons have slightly longer plungers and less clearance to switches than others. Some with only .002" clearance.
Panel in place. Leave the control panel mounting screws loose when fitting face plate.
I received the used timer switches and replaced those. They were on a broken PCB so got them cheap.
Face plate on, getting closer. Await brushes and inductors for capstan motor.
Salk SoundScape 8's * Audio Research Reference 3 * Bottlehead Eros Phono * Park's Audio Budgie SUT * Krell KSA-250 * Harmonic Technology Pro 9+ * Signature Series Sonore Music Server w/Deux PS * Roon * Gustard R26 DAC / Singxer SU-6 DDC * Heavy Plinth Lenco L75 Idler Drive * AA MG-1 Linear Air Bearing Arm * AT33PTG/II & Denon 103R * Richard Gray 600S * NHT B-12d subs * GIK Acoustic Treatments * Sennheiser HD650 * -
Brush time. I learned there are a few different grades of brushes. The ones I got say carbon, but they look more like carbon graphite. A brush company engineer said they are slightly softer than carbon but will work and should last as long. We'll see.
I had ordered some brushes near the exact size, 3x3 mm. They were longer but easily trimmed to 4mm length. But it was a leaded brush. I was thinking how far those leads may extend into brush. We don't want harder wire eating up the commutator as brush wears.
I found an unleaded brush, but it was 4x4mm and needed to be trimmed down. While one could do some filing/sanding by hand, I wanted a way to achieve a more precision result. So, I cobbled again.
Two 1/8" (3.18mm) drill bits fastened down to a chunk of wood with a screw and nut. The screw allows repositioning the bits to get a snug fit on the width of brush. A file is used. Drill shanks are hard, the file just removes brush material. The .18mm can disappear dragging it over some fine sandpaper. I don't want to deviate from the OEM brush size.
Second station, two more 1/8" (3.18mm) drill bits set to hold the 3.18mm width tight. File down to 3.18, now I have a square brush.
Third station. Two 3/32" (2.33mm) drill bits. Two concrete nails. A 1/16" bit used as stop. This files some relief on each side of brush to fit in the small slot in brush holder.
This brush will get trimmed down. The strap can only stretch so far before the strap or plastic posts it's wraps around, gives.
Conductive epoxy is pricey but they do sell it in small packets for $13 on Amazon.
24 hours cure time and they we'll see if it holds. My old eyes held out long enough working through lighted magnifier to apply some conductive epoxy without making too much of a mess.
Salk SoundScape 8's * Audio Research Reference 3 * Bottlehead Eros Phono * Park's Audio Budgie SUT * Krell KSA-250 * Harmonic Technology Pro 9+ * Signature Series Sonore Music Server w/Deux PS * Roon * Gustard R26 DAC / Singxer SU-6 DDC * Heavy Plinth Lenco L75 Idler Drive * AA MG-1 Linear Air Bearing Arm * AT33PTG/II & Denon 103R * Richard Gray 600S * NHT B-12d subs * GIK Acoustic Treatments * Sennheiser HD650 * -
It lives! Gonna run it, break in brushes. When inductors get here, I'll pop it apart and replace them, clean out any brush dust.
Salk SoundScape 8's * Audio Research Reference 3 * Bottlehead Eros Phono * Park's Audio Budgie SUT * Krell KSA-250 * Harmonic Technology Pro 9+ * Signature Series Sonore Music Server w/Deux PS * Roon * Gustard R26 DAC / Singxer SU-6 DDC * Heavy Plinth Lenco L75 Idler Drive * AA MG-1 Linear Air Bearing Arm * AT33PTG/II & Denon 103R * Richard Gray 600S * NHT B-12d subs * GIK Acoustic Treatments * Sennheiser HD650 * -
The owner of this deck has been sitting on two pairs of Teac CA (Cobalt Amorphous) record/playback heads (found in the X-2000r) and asked for them to be installed instead of the Permalloy. They standout due to orange epoxy being used instead of black.
Teac said their CA, Cobalt Amorphous head, has twice as many segments as a regular Permalloy head. The advantages are significantly smaller eddy current losses making it easier on the recording/playback amplifier. They also claimed better operation in the HF range.
When swapping heads, head alignment needs to be checked and adjusted. Next up, the old clear leader trick, improved. I cut a length of clear leader tape and attached a short piece of rubber band to the loose ends. This keeps the tape tensioned and leaves my hands free to turn screws.
The tape was routed under the capstans in order to wrap the tape around the record heads for easier adjusting.
It's easy to set height, that is edge of tape position to head cores, but harder to ensure the head is square to the tape and head plate, especially with head shields. This is all I will show as my setup is very Rube Goldberg like. Basically, a square that has been checked with another square has been secured to a flat surface that had been checked with a straight edge.
The head plate is secured against the square, so the head plate is 90 degrees to the flat surface. A dial indicator is used to adjust head position. That is front and back of head are equal distance off the flat surface. It sure looked pretty good viewed from different angles. Any adjustment here means the clear leader tape must be installed and height checked again. The shields were added after this adjustment.
Getting closer to hope it still works...and calibration.
Salk SoundScape 8's * Audio Research Reference 3 * Bottlehead Eros Phono * Park's Audio Budgie SUT * Krell KSA-250 * Harmonic Technology Pro 9+ * Signature Series Sonore Music Server w/Deux PS * Roon * Gustard R26 DAC / Singxer SU-6 DDC * Heavy Plinth Lenco L75 Idler Drive * AA MG-1 Linear Air Bearing Arm * AT33PTG/II & Denon 103R * Richard Gray 600S * NHT B-12d subs * GIK Acoustic Treatments * Sennheiser HD650 * -
Another issue with the X-1000r, the solenoid-controlled mechanical ALPS switches mounted to bottom PCB. S307, S308 and S309 handle forward/reverse switching of various circuits, including R & L channel signals to and from the heads. They are difficult to clean. When dirty or worn you can lose a channel or have a record/playback channel imbalance.
A fellow named Kurt Jacobs sells a kit on ebay for $100 that replaces the mechanical switches/relay with sealed relays with gold contacts. He gave me a great deal on three kits. His pic from his ad.
The worst part of removal, some of the pins were bent over to hold them in prior to soldering. They are very hard pins to bend. One must be careful. Remove all the solder possible between bent pins and board with flux/solder wick. I still heated the pins before attempting to straighten so I didn't pull a trace off board. Some of the pins broke when straightened.
The Hakko FR-301 desolder gun is a great asset. No collateral damage to PCB. Just need some flux/solder wick clean up.
One switch disassembled. This one had some resistance between some positions. The replacement relay kits should be here Monday.
Another issue concerned the "wood" cabinet. No veneer here, it's a vinyl wrap over the inexpensive wood. This deck was missing the anchor bracket for the large plastic cover that will fit over 10.5" reels. I made one out of textured one side ABS plastic (opposite side smooth) and used double sided tape to mount it. A 3D printer would have been a nice way to make one.
I added an adhesive felt disc on the cover mount bracket to prevent the screws from chewing up the vinyl wood wrap any more than they have.
This pic is when it first arrived here. The cover has some small cracks over the reel hub area. Wondering if I should drill some tiny stop holes at each end of them.
Post edited by SCompRacer onSalk SoundScape 8's * Audio Research Reference 3 * Bottlehead Eros Phono * Park's Audio Budgie SUT * Krell KSA-250 * Harmonic Technology Pro 9+ * Signature Series Sonore Music Server w/Deux PS * Roon * Gustard R26 DAC / Singxer SU-6 DDC * Heavy Plinth Lenco L75 Idler Drive * AA MG-1 Linear Air Bearing Arm * AT33PTG/II & Denon 103R * Richard Gray 600S * NHT B-12d subs * GIK Acoustic Treatments * Sennheiser HD650 * -
WOW! The audio technician/magician is at it again! Great work Richee! I am lovin' this photo journal!
Carl -
-
Yes, that is my deck on the operating table!
Sure hope Rich knows what he's doing, I'd be scared to wake up without my deck2-channel: Modwright KWI-200 Integrated, Dynaudio C1-II Signatures
Desktop rig: LSi7, Polk 110sub, Dayens Ampino amp, W4S DAC/pre, Sonos, JRiver
Gear on standby: Melody 101 tube pre, Unison Research Simply Italy Integrated
Gone to new homes: (Matt Polk's)Threshold Stasis SA12e monoblocks, Pass XA30.5 amp, Usher MD2 speakers, Dynaudio C4 platinum speakers, Modwright LS100 (voltz), Simaudio 780D DAC
erat interfectorem cesar et **** dictatorem dicere a -
I can absolutely guarantee Carl's Teac X-1000r deck is the only thing I put my hands on.
Correct relay kits arrived today. Kurt supplies some solder and solder wick with each relay kit. Instructions are emailed and very thorough. No pictures, so I had to use my brain and may have sprained it.
Instructions suggest fitting header pins from bottom of board. It's real busy inside chassis with wires and components, and this makes it easier.
One thing that made fitting easier was carefully sliding plastic base up header pins an 1/8" or so. Carefully means holding PCB sides while pushing base up without bending any components or putting pressure on tops of relays. The pins become more flexible with extra length. Less chance of harming traces using tool to bend pins against board or forcing them in. This doesn't mean you can mount the relays closer to PCB as they still have to clear components on the topside of PCB. I don't like to bend older components on PCB's as it increases risk of collateral damage.
Tight spacing on the pins so you have to check for solder bridges. I had a couple.
All fixed. You must check that pin length is not too long; that they are no longer than existing pins. An insulator sheet and metal cover are fastened under this PCB. If leads are too long, you invite a short.
You attach the white and brown wire from solenoid to first relay board. The other two boards arrive daisy chained with wires.
The boards have LED's which can be used to indicate problems. No LED's are illuminated in forward play. Reverse play, you should get three greens and one red. All good.
It lives and breathes. On to calibration.
EDIT:
One other thing Kurt Jacobs provides is a plug and play X-1000r 7"/10.5" reel size and 3.75/7.5ips speed switch. These are notorious for breaking, or failure to latch. Some guys take the springs off and manually push them in, pull them out. I read no exact replacement switches were available, only one that required modding.
The old.
The new.
Post edited by SCompRacer onSalk SoundScape 8's * Audio Research Reference 3 * Bottlehead Eros Phono * Park's Audio Budgie SUT * Krell KSA-250 * Harmonic Technology Pro 9+ * Signature Series Sonore Music Server w/Deux PS * Roon * Gustard R26 DAC / Singxer SU-6 DDC * Heavy Plinth Lenco L75 Idler Drive * AA MG-1 Linear Air Bearing Arm * AT33PTG/II & Denon 103R * Richard Gray 600S * NHT B-12d subs * GIK Acoustic Treatments * Sennheiser HD650 * -
Hello Carl! Nice rig!!
-
Thanks Ivan!
Dude put his name on the PCB for the new relays and speed switch. Nice upgrade!
These decks will be refurbished like no other! Rock on Richee!
Carl -
Bad richee. I was watching one of Bigg Matt's X-1000r repair videos and learned the washer goes under the link against the face of pinch roller bracket. I need to find an original manual as some of the downloads don't print well.
This was assembled incorrectly by a previous person. The washer doesnt go there.
Salk SoundScape 8's * Audio Research Reference 3 * Bottlehead Eros Phono * Park's Audio Budgie SUT * Krell KSA-250 * Harmonic Technology Pro 9+ * Signature Series Sonore Music Server w/Deux PS * Roon * Gustard R26 DAC / Singxer SU-6 DDC * Heavy Plinth Lenco L75 Idler Drive * AA MG-1 Linear Air Bearing Arm * AT33PTG/II & Denon 103R * Richard Gray 600S * NHT B-12d subs * GIK Acoustic Treatments * Sennheiser HD650 * -
Still plugging away. Two of the decks had brake problems. You measure it with a string wrapped around an empty reel, read ounces it takes to move reel and multiply by radius of empty reel to get result. Techs were saying go to fabric store, buy some 1.5mm premium felt, cut to size and glue on brake band. With the new felt, I could not get the correct spring scale tension even adjusted to the max. The wife says you know most felt is 100% polyester these days, try some wool felt. Joann fabrics had a 35% wool blend, and it worked. I got correct tension at minimum band adjustment. Felt matters.
A brake band with felt lining. The lacquer finish on brake drums is also important. If worn through, must refinish. You don't want stop on a dime and give you change. Some slip is needed, or you stretch and break tape.
Did brushes in the other two capstan motors. Reel motor brushes were very good. Glad to have brushes done.
You run into tape wear on guides, tape lifter. Some fine micron paper smooths and polishes.
Mother's came to rescue the appearance of some reel hubs.
The foam cushions for the swinging tension arms were in decay. I had saved a block of pluck and pull foam from a case for something we can't talk about here. Basically, it's a foam block with pre-scored small squares you pluck out to fit. I cut them to size and adhered with double sided tape.
One deck is missing nylon mounting washers for the tension roller posts and a couple washers. The mounting washers are different size then the friction washers (which can be found on epay, but you do pay). The mount washers are unobtanium unless you buy a complete tension arm post for 80 bucks. Got some thin washers coming from China. I was also thinking of a leather punch to make my own out of .010 plastic sheet.
Got up to bias trap calibration on Carl's deck and wasn't sure if this scope pattern of test point 1 and 2 were correct, but it is. The manual says adjust to lowest reading with millivolt meter, but techs were saying you can get a closer adjustment with scope. More calibration to do.
Two of the decks are getting a new look. Like AC/DC, back in black. Thank you Carl! I kinda like the silver accents. The seller forgot to include the black mounting screws, but they are on the way. The black head cover was included, but some guys swap it out for a silver one.
To get all black as Teac shipped it, one has to spend for knobs (like $25 each), VU meter cover, etc... The white VU meters are much easier to read than the black ones. Brighter LED's can cause more issues then they solve. Some guys have added white VU meters to their black X-1000r's.
I had purchased a black VU meter cover for an X-2000r (cheap at $25 free shipping), but the black insert is different so I had to use my silver one. The lens and frame are identical to the X-1000r.
A you tube video showing various X-1000r color combinations.https://youtu.be/XJAdm-xWHSE?si=lTXwOHDprDyPM28y
Post edited by SCompRacer onSalk SoundScape 8's * Audio Research Reference 3 * Bottlehead Eros Phono * Park's Audio Budgie SUT * Krell KSA-250 * Harmonic Technology Pro 9+ * Signature Series Sonore Music Server w/Deux PS * Roon * Gustard R26 DAC / Singxer SU-6 DDC * Heavy Plinth Lenco L75 Idler Drive * AA MG-1 Linear Air Bearing Arm * AT33PTG/II & Denon 103R * Richard Gray 600S * NHT B-12d subs * GIK Acoustic Treatments * Sennheiser HD650 * -
Those missing washers for the tension roller mounting posts..... a .010" (.25mm) thick plastic sheet, a three-ring binder hole punch, a 4mm leather punch and a small hammer took care of that.
I felt like a magician at first. They kept disappearing until I colored them with a marker.
Salk SoundScape 8's * Audio Research Reference 3 * Bottlehead Eros Phono * Park's Audio Budgie SUT * Krell KSA-250 * Harmonic Technology Pro 9+ * Signature Series Sonore Music Server w/Deux PS * Roon * Gustard R26 DAC / Singxer SU-6 DDC * Heavy Plinth Lenco L75 Idler Drive * AA MG-1 Linear Air Bearing Arm * AT33PTG/II & Denon 103R * Richard Gray 600S * NHT B-12d subs * GIK Acoustic Treatments * Sennheiser HD650 * -
I cobbled together a wood rack to safely hold the deck on its back while calibrating it. I like this better than pillows or quilts supporting the two circuit boards at top rear. It also provides space to get at the input/output RCA's and not stress them with weight of the deck. The rack also fits on my rotisserie and allows turning the assembly.
There are 36 pots on bottom PCB to adjust. There are another 16 on the dbx board and hopefully that one is OK and hasn't been messed with. That one also requires a distortion meter.
The pots are hard to get at from top, inside, with rear I/O panel attached. There are lots of wires in the way. There are also test points to connect scope/millivolt meter to while adjusting.
Home Depot actually had two very straight 1x2's!
I removed mic/line in and out pots from the PCB to clean. The ones on this deck were scratchy. Their location made it more a spray and pray with high odds for a mess. They were tested with analog ohm meter afterwards to make sure they operated smoothly.
Salk SoundScape 8's * Audio Research Reference 3 * Bottlehead Eros Phono * Park's Audio Budgie SUT * Krell KSA-250 * Harmonic Technology Pro 9+ * Signature Series Sonore Music Server w/Deux PS * Roon * Gustard R26 DAC / Singxer SU-6 DDC * Heavy Plinth Lenco L75 Idler Drive * AA MG-1 Linear Air Bearing Arm * AT33PTG/II & Denon 103R * Richard Gray 600S * NHT B-12d subs * GIK Acoustic Treatments * Sennheiser HD650 * -
Incredible!!
-
Love it. What complicated machines, yet considered the best for playing music. Had no idea all the engineering that went into a R2R.
You make it look and sound so easy. Carl will be tickled pink when he gets the virgin playback.
H9"Appreciation of audio is a completely subjective human experience. Measurements can provide a measure of insight, but are no substitute for human judgment. Why are we looking to reduce a subjective experience to objective criteria anyway? The subtleties of music and audio reproduction are for those who appreciate it. Differentiation by numbers is for those who do not".--Nelson Pass Pass Labs XA25 | EE Avant Pre | EE Mini Max Supreme DAC | MIT Shotgun S1 | Pangea AC14SE MKII | Legend L600 | BlueSound Node 3 - Tubes add soul! -
Thanks for the kind words. These things are pretty complicated and have presented some challenges. I hope to get all three working without turning one into a parts machine.
One other thing I learned. JIS. Japanese Industry Standard screws. I have some really good quality screwdrivers and bits, but they didn't seem quite right loosening or tightening screws on these decks. I had to apply extra force to keep the driver engaged in screw head.
JIS are similar to our Phillips head. Unlike Phillips which are designed to cam out, the JIS is designed to keep applying force and hold tighter in the head of screw. There is a significant difference in feel using the JIS drivers on the JIS screw heads.
Salk SoundScape 8's * Audio Research Reference 3 * Bottlehead Eros Phono * Park's Audio Budgie SUT * Krell KSA-250 * Harmonic Technology Pro 9+ * Signature Series Sonore Music Server w/Deux PS * Roon * Gustard R26 DAC / Singxer SU-6 DDC * Heavy Plinth Lenco L75 Idler Drive * AA MG-1 Linear Air Bearing Arm * AT33PTG/II & Denon 103R * Richard Gray 600S * NHT B-12d subs * GIK Acoustic Treatments * Sennheiser HD650 * -
I picked up a nice used Tentelometer a few weeks back. A very good deal at $205 shipped and it had the manual and calibration weight. There are various models with different ranges. The word was to have the target spec close to middle of scale and cover the ranges needed. Need one to adjust tape tension with tape running. Target is 50-60gram. Fast wind spec is 110 gram.
Lots of things to watch for. Tilt, height, tangency, azimuth and zenith. A sharpie and an old tape show the contact area on head. Azimuth is done with test tape.
I snapped up a pair of Teac NOS record heads at a very reasonable price. You don't see them often at below scarce pricing. This allowed me to compare my lap job to a new head. New is at left.
The lapped tracing is from one of the installed heads.
I temporarily mounted a new head to compare to my lapped one. Looks good. New head at right.
Post edited by SCompRacer onSalk SoundScape 8's * Audio Research Reference 3 * Bottlehead Eros Phono * Park's Audio Budgie SUT * Krell KSA-250 * Harmonic Technology Pro 9+ * Signature Series Sonore Music Server w/Deux PS * Roon * Gustard R26 DAC / Singxer SU-6 DDC * Heavy Plinth Lenco L75 Idler Drive * AA MG-1 Linear Air Bearing Arm * AT33PTG/II & Denon 103R * Richard Gray 600S * NHT B-12d subs * GIK Acoustic Treatments * Sennheiser HD650 * -
WOW! Perfect lap job Richee! This work is several levels above professional, might be better than factory!Carl
-
Wow Carl, I thought I restored decks as a hobby - Richee is on a whole different league or two above what I do! Looks great! / Pepe
-
Richee has been getting his cootox handed to him, Pepe.
The first deck, Carl’s, has been driving me crazy. Issues include an odd bias trap pattern for R and L channels. L channel bias ½ value of right channel, no record in fwd or rev mode and vu meters deflect to zero in FWD record/record pause mode. I'd study schematic, test. Having three of these is nice to cross check voltages and scope patterns.
Some techs said they’ve never seen that before. Great. I thought it was going to be a parts machine and I’d give Carl my deck. Then I swapped the replacement relay boards out with three of the removed (cleaned and tested) mechanical ALPS switches. Now, all is well again.
The relays test OK so I don’t know if one stuck or? (There were no solder bridges and all solder joints were redone). The designer is out of country and will look into it when he returns. In his instructions he mentions one deck out of all relay kits he sold had noise issues in FWD record mode, but I had more than noise. He came up with a different ground scheme for it. In hindsight I should have tried it, but I was frustrated and wasn't thinking clearly.
I have had no problems with the relay boards in the other two decks. There were no LED’s on so the relays should have been in default FWD mode.
Bias trap TP1 (L) and TP2 (R) before with relays.
Bias trap TP1 and TP2 after ALPS switches re-installed.
The deck was manufactured with three mechanical ALPS switches in bottom board. A solenoid bar moves them for REV record/play. Think of them as twenty four SPDT (single pole double throw) switches. Nine each in two switches and six in one. Every three pins is an individual switch. Center hot, right and left = FWD and REV.
I ohm'd out the relays with no power to them and they checked out OK. Proper continuity in all pin positions, nothing where it shouldn't be. I applied power and tested in REV mode, all test OK. Remove power and re-test in FWD mode, all OK. While it checked out OK I'm reluctant to reinstall it without knowing why it happened.
New tires showed up from Terry Witt. I learned of another source for new pinch rollers from SofH in Italy. Price wise, I can get a new set with bushings or bearings for same price as replacing rubber tires. Terry does a great job. They are perfectly round, no runout. You can buy slip on tires from ebay cheap, clean the hubs and glue them on, but they won't be perfectly round and may be too large and need turning down in diameter.
If the pinch rollers are hard or have a tape path worn in, you will get tape skew across the heads and poor record/playback. Out of round can introduce wow and flutter. OEM roller at right.
Salk SoundScape 8's * Audio Research Reference 3 * Bottlehead Eros Phono * Park's Audio Budgie SUT * Krell KSA-250 * Harmonic Technology Pro 9+ * Signature Series Sonore Music Server w/Deux PS * Roon * Gustard R26 DAC / Singxer SU-6 DDC * Heavy Plinth Lenco L75 Idler Drive * AA MG-1 Linear Air Bearing Arm * AT33PTG/II & Denon 103R * Richard Gray 600S * NHT B-12d subs * GIK Acoustic Treatments * Sennheiser HD650 *