Magnet Shift Repair Solved...for me that is.

downinmexico
Posts: 9
I wanted to share my solution for the magnet shift issue in hopes that it may help someone here.
I have a part time business restoring and repairing vintage stereo equipment. Recently I began restoration of a set of Monitor 7s. Both MW-6500s were locked up tight. They both ohmed out fine, but the magnets had definitely shifted, preventing the coils from moving.
I began first by separating the magnet and pole piece from each basket. I then went to thinking about the easiest way to line them back up and glue them in place without the voice coil rubbing. One of the great perks I have where I work is that I can do my "Government Projects" without any problems from the boss.
I knew that I had to glue the pole piece exactly in the center of the magnet hole. So I fabricated a piece of aluminum shaft to fit exactly inside diameter of the magnet hole. I then drilled out the center of the aluminum shaft the exact diameter of the pole piece.
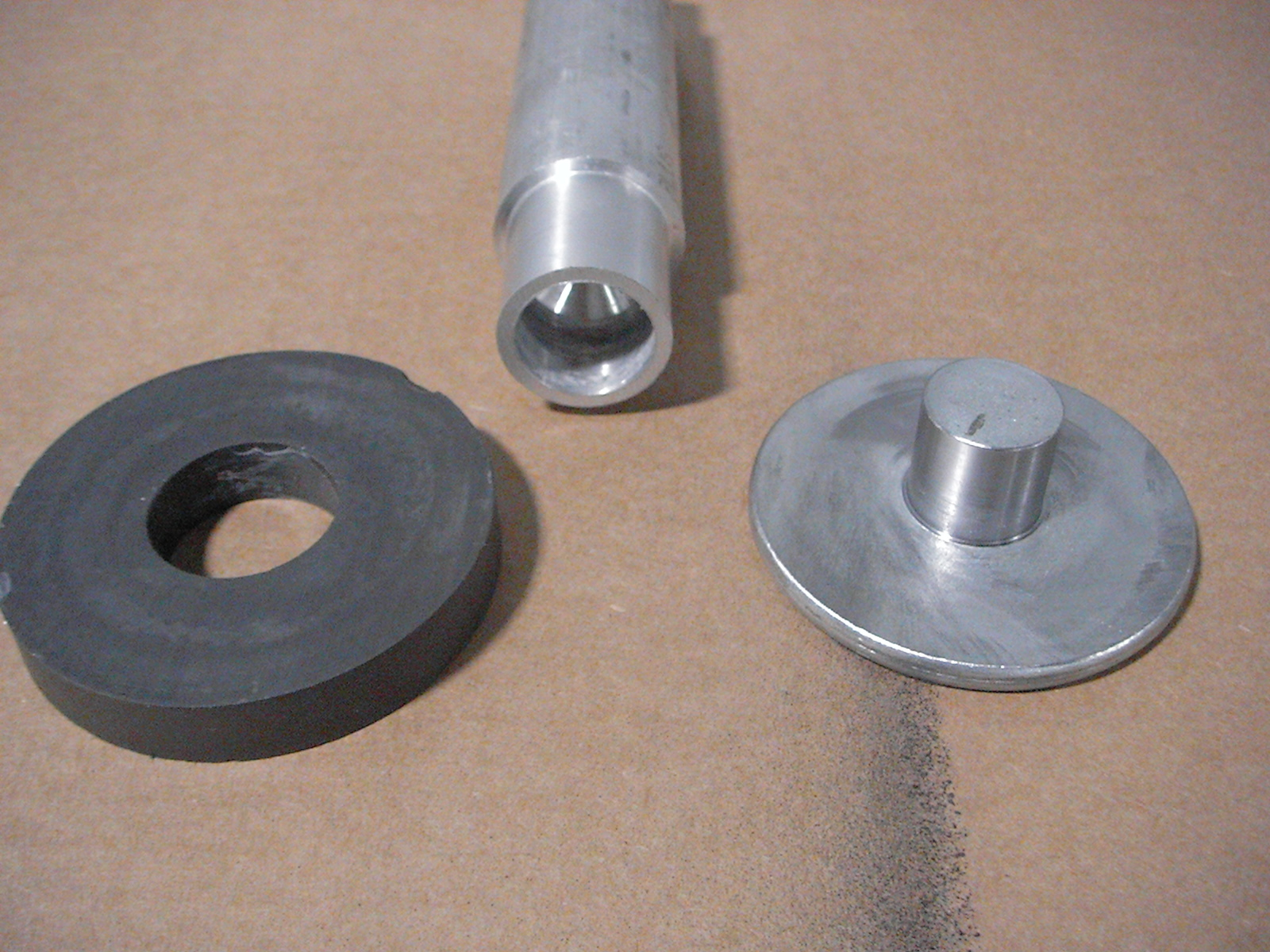
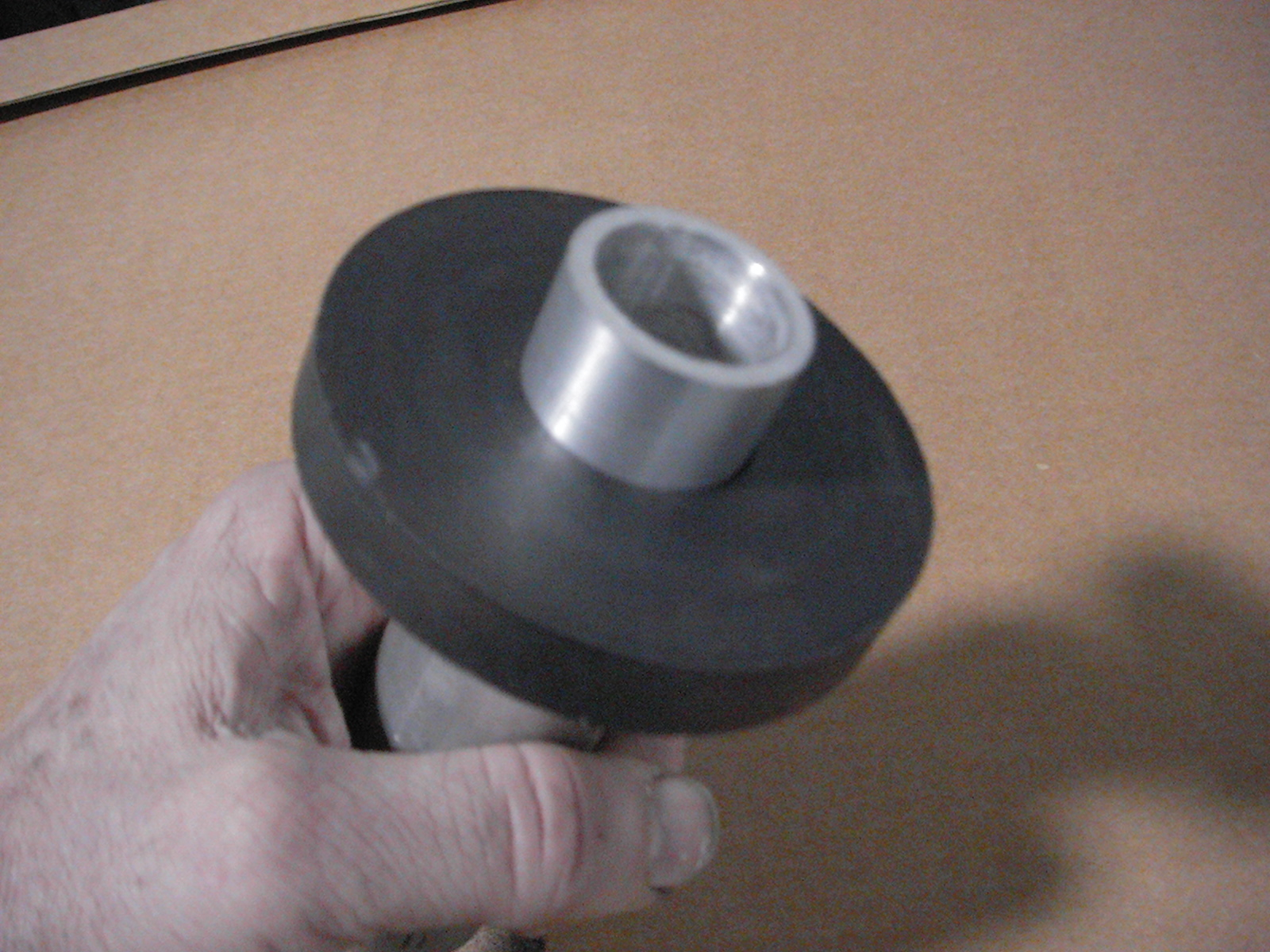
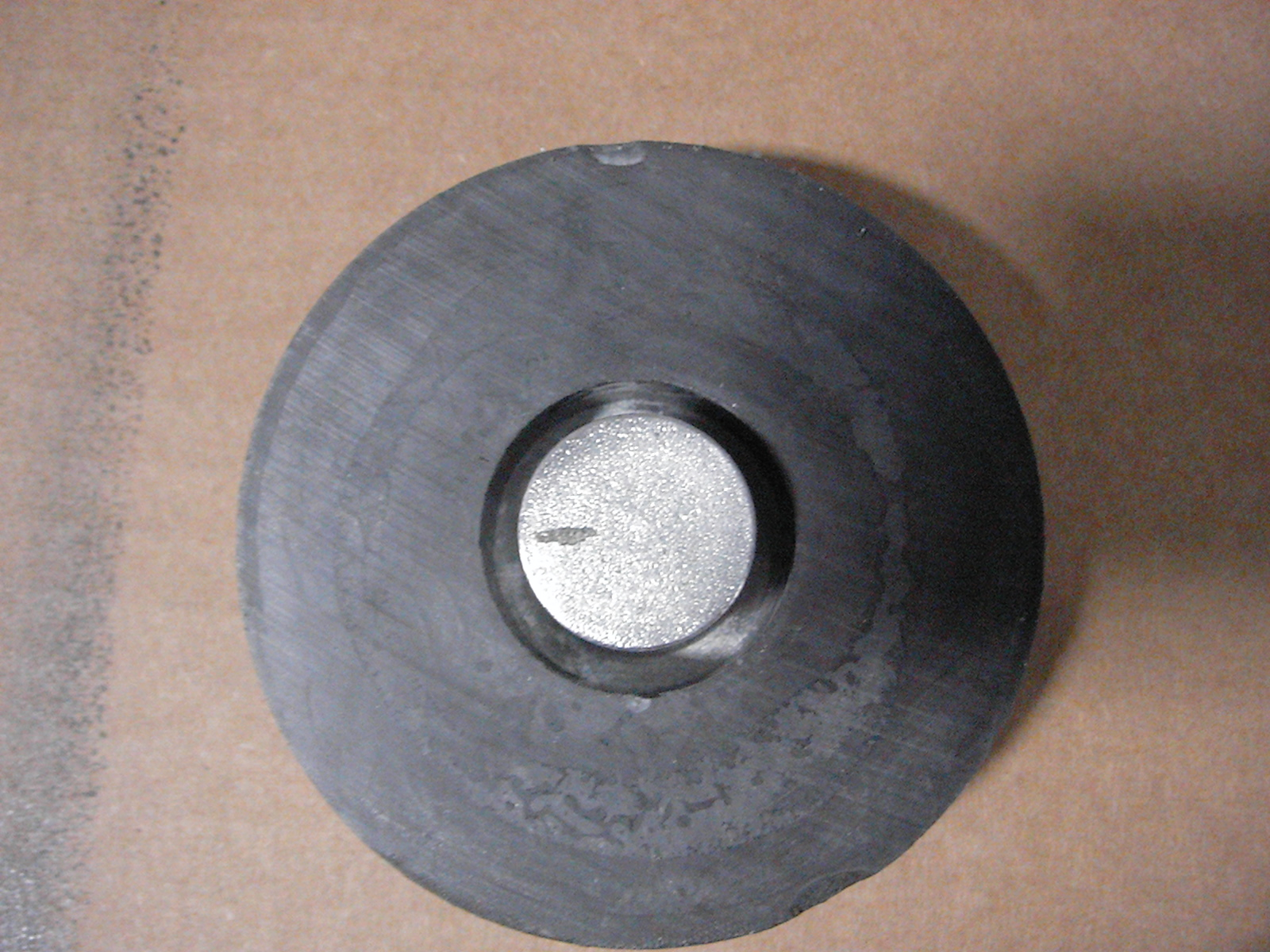
Before I glued the pole piece to the magnet, I drilled out the hole on the back of the pole piece so I could tap it with 7/16" x 14 threads. This was so I could hold it steady when I got to the point of joining the pole piece/magnet assembly to the basket.
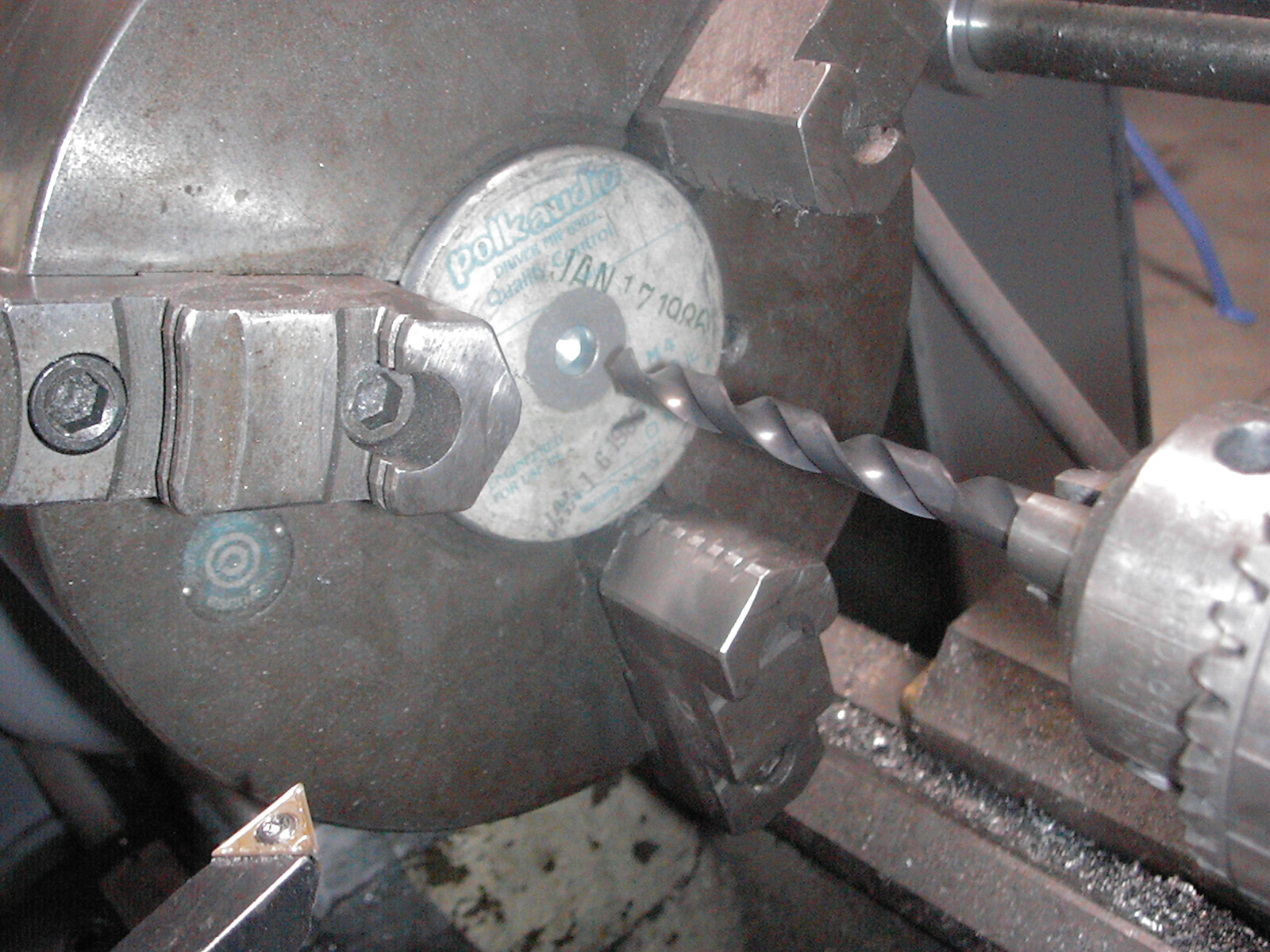
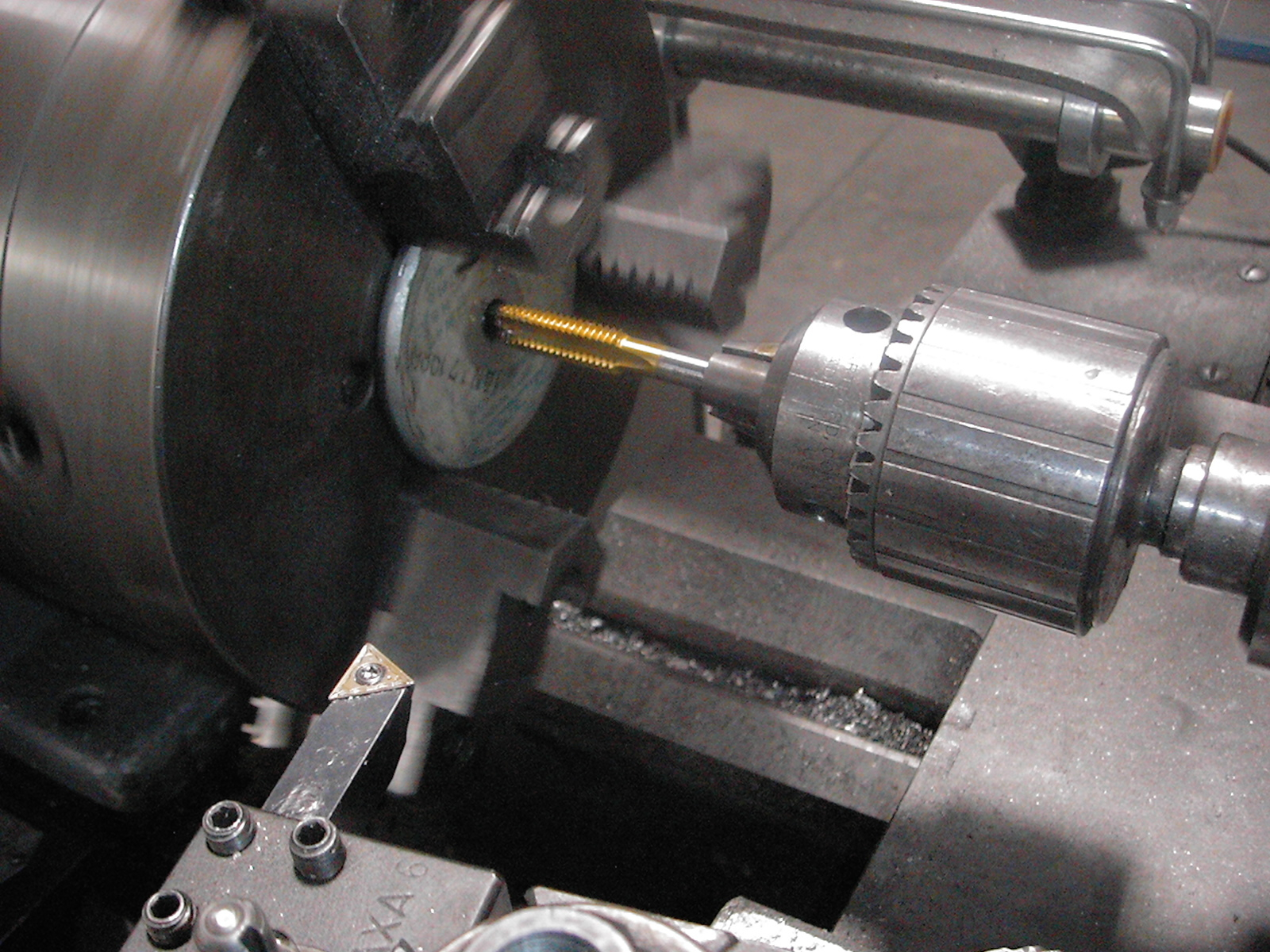
I have had pretty good luck using 3M 460 two part epoxy for gluing metal in the past, so I tried here also. I spread the glue evenly around the magnet's surface keeping it away from the center so it would not squeeze into the gap between the pole piece and the magnet.
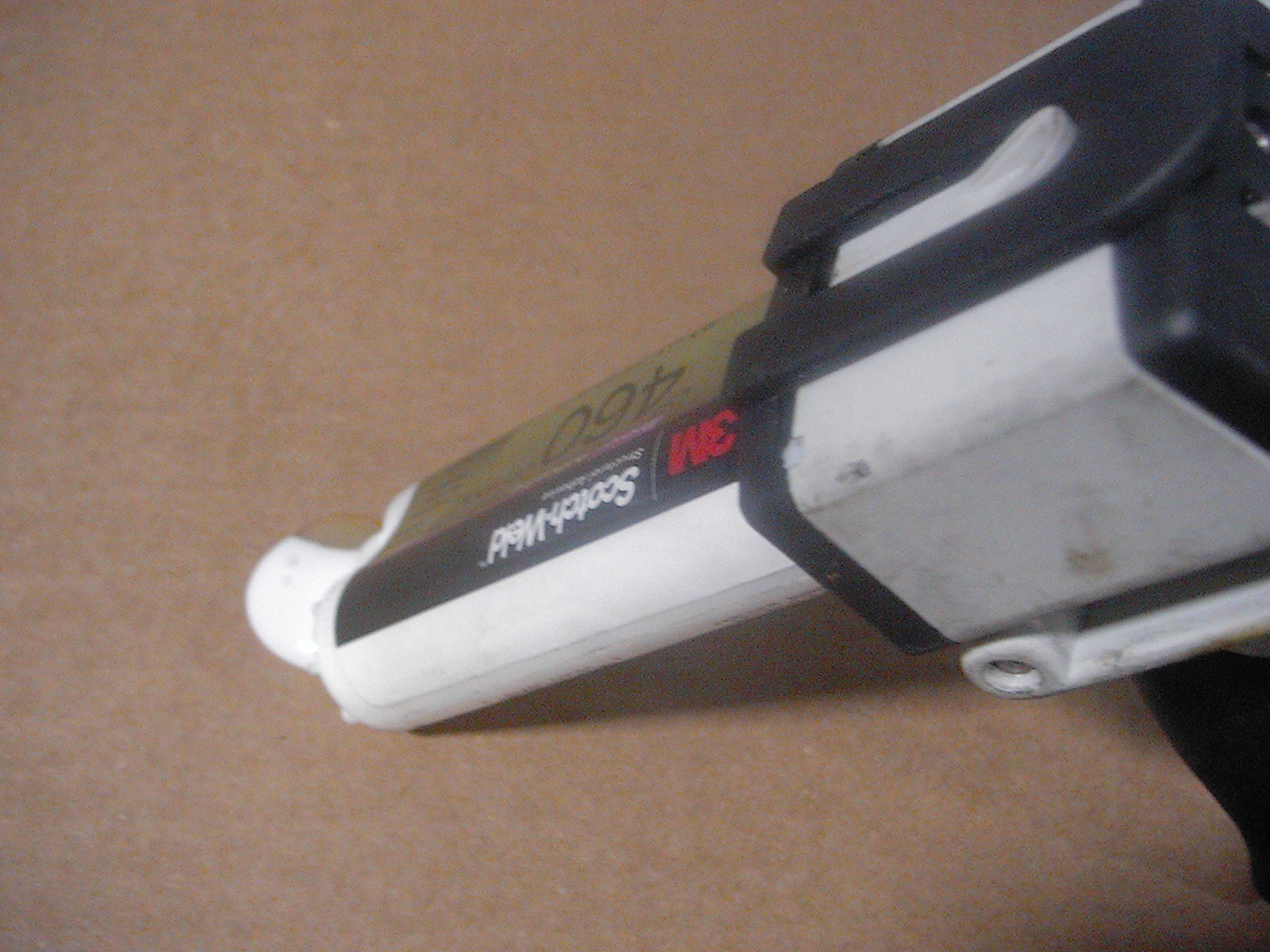
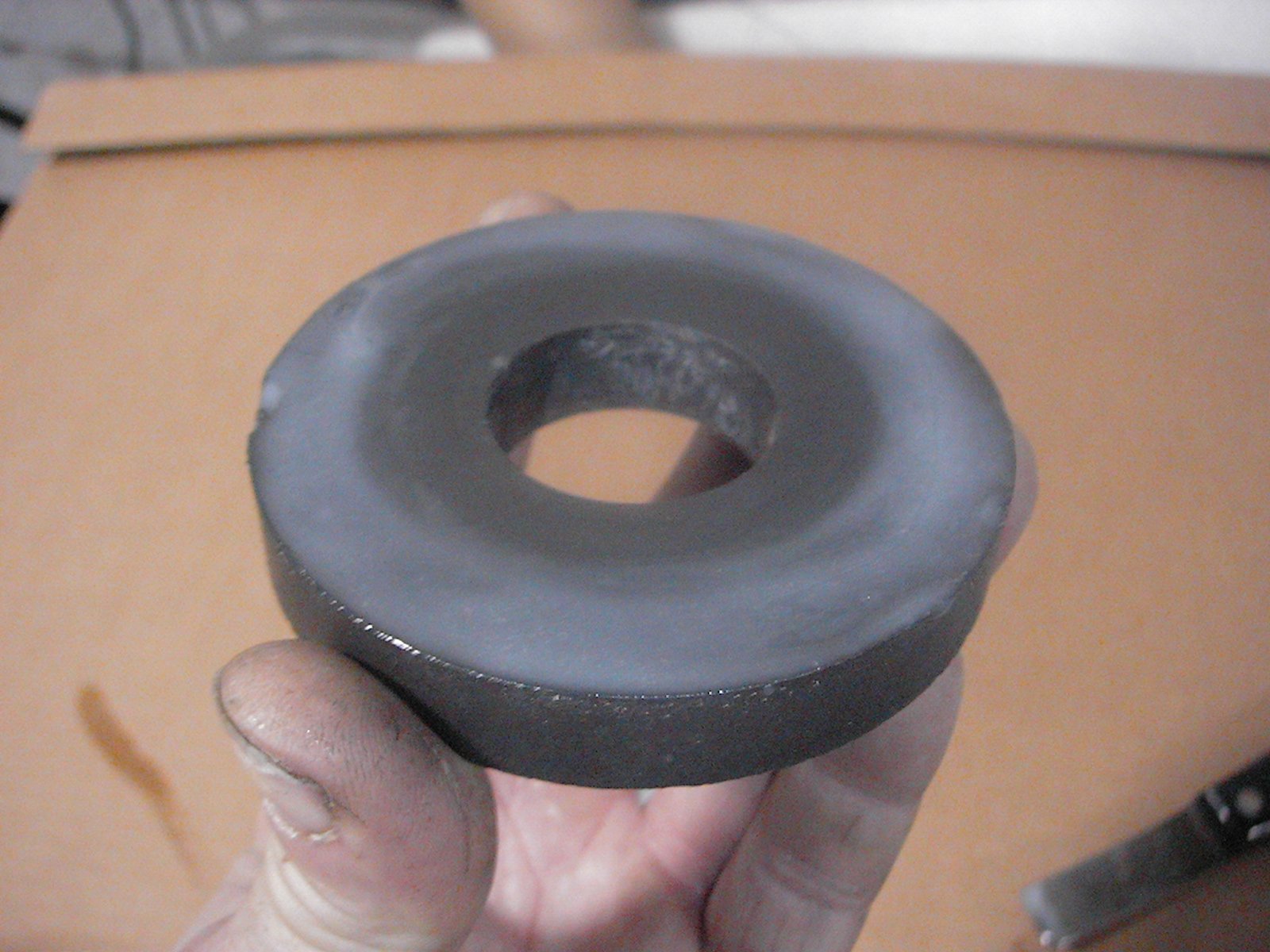
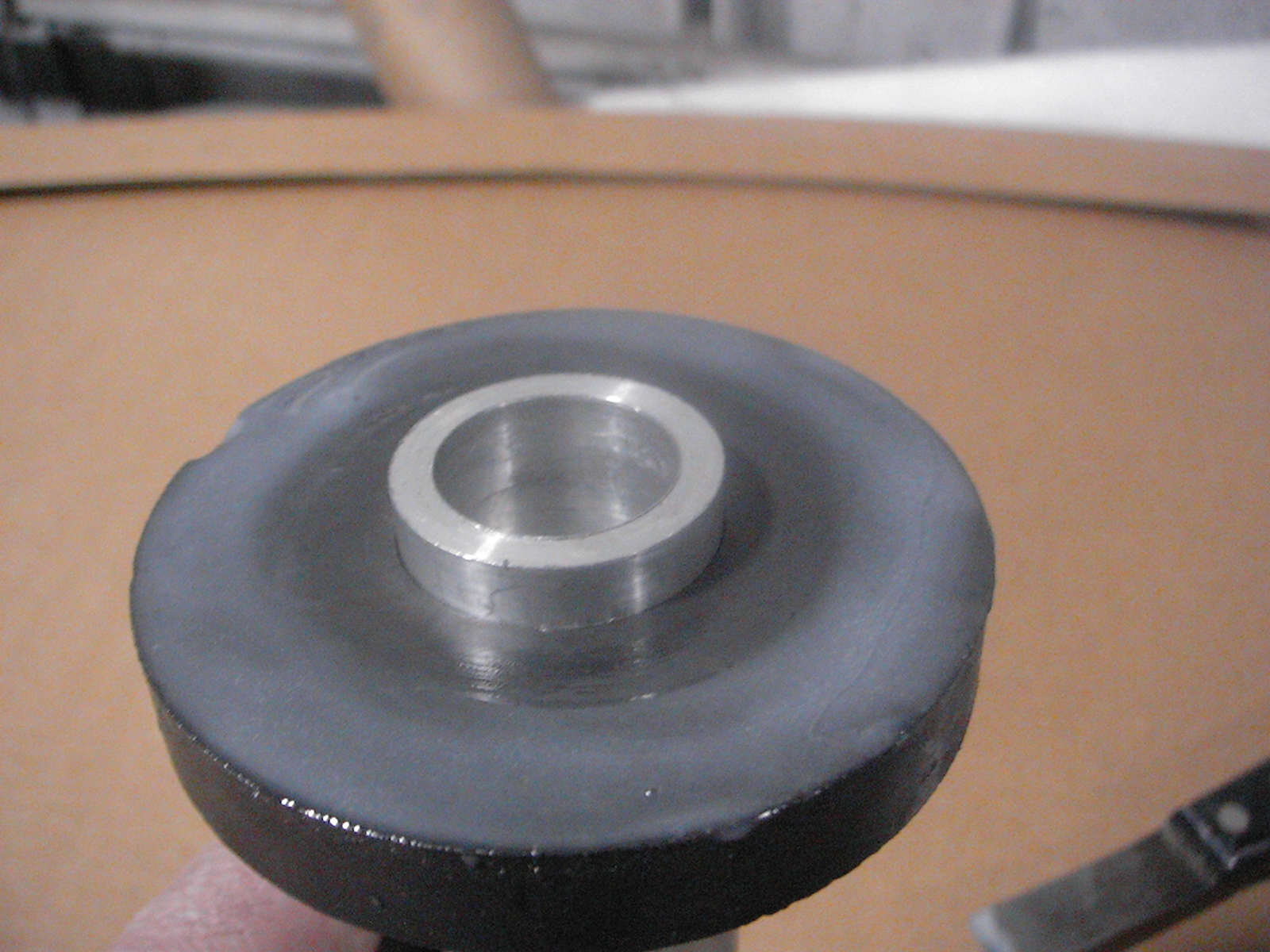
Once I glued them together, I then clamped them tight.
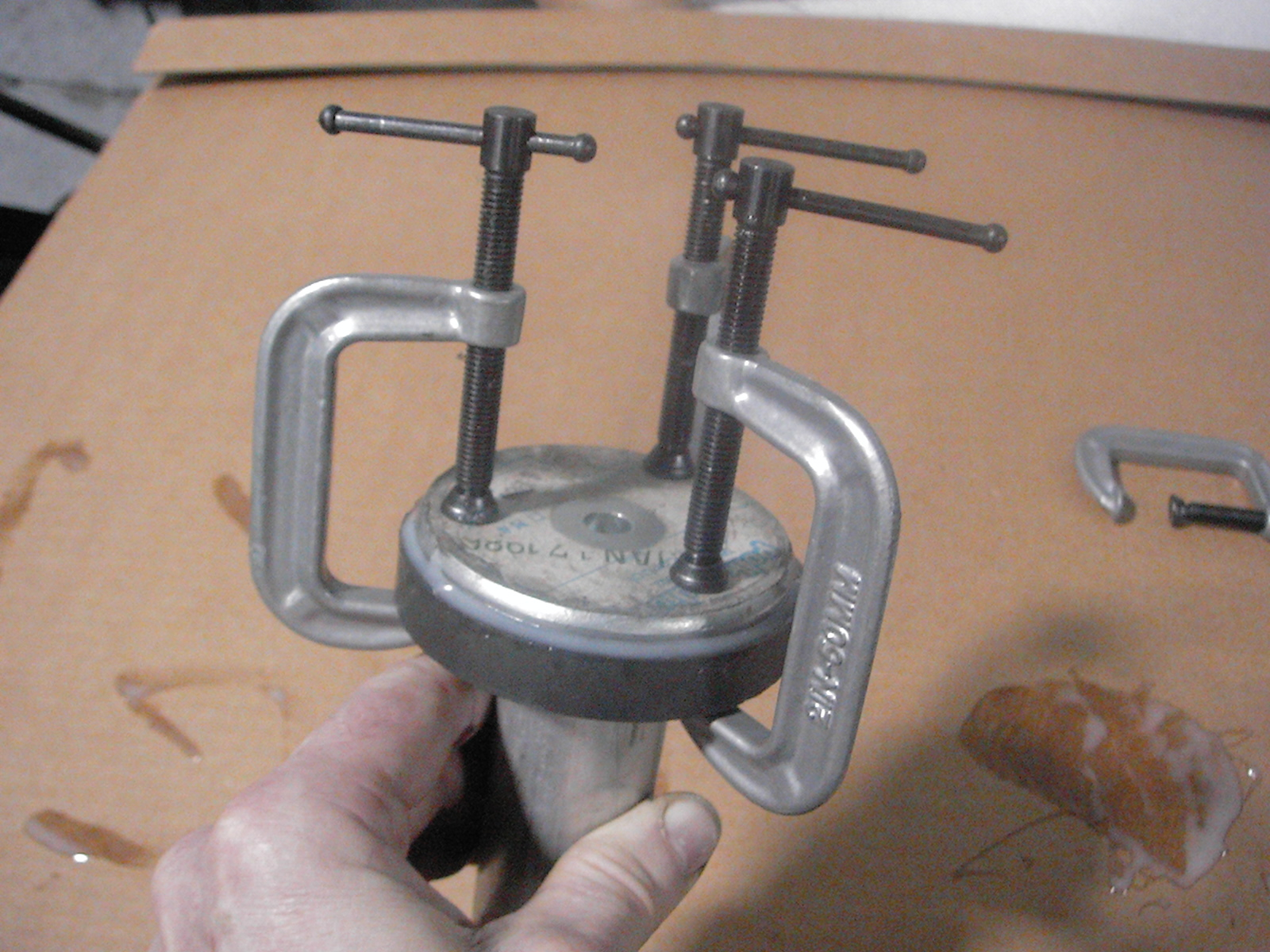
The next thing I had to do was make a way to join the pole piece/magnet assembly to the basket and get it perfectly centered. I took a piece of 3.5" o.d. steel pipe (I may should have used pvc, but I am a machinist by trade and not a plumber), and turned down the inside diameter to exactly fit the outside diameter of the magnet (appx. 3.375") and cut it off at 2" long. I then needed a way to center this to the back of the basket, around the steel disk with the hole in it for the voice coil. I took a piece of the same 3.5" o.d. pipe and turned down a section that would fit exactly around the steel disk attached to the basket (appx. 3" i.d). I then turned down the outside to fit the inside of the first section of pipe, (appx. 3.375). I cut this section .5" long and then inserted it into the 2" section of pipe at one end. I then drilled 4 holes 90 degrees apart all the way through both sections and tapped them to 10-32 threads. I then took the .5" section out of the 2" section and cut it in half so I could remove it once the epoxy had set.
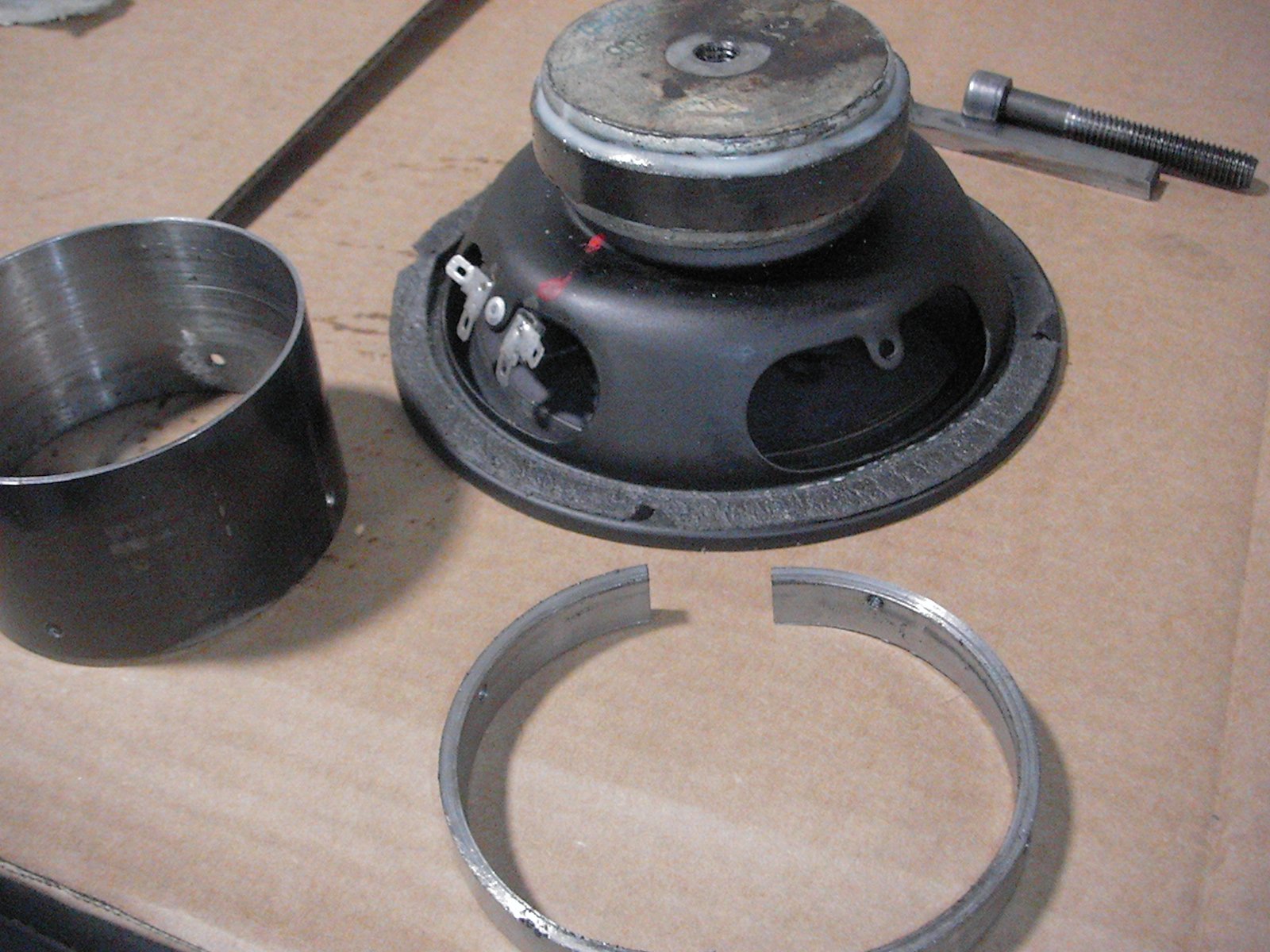
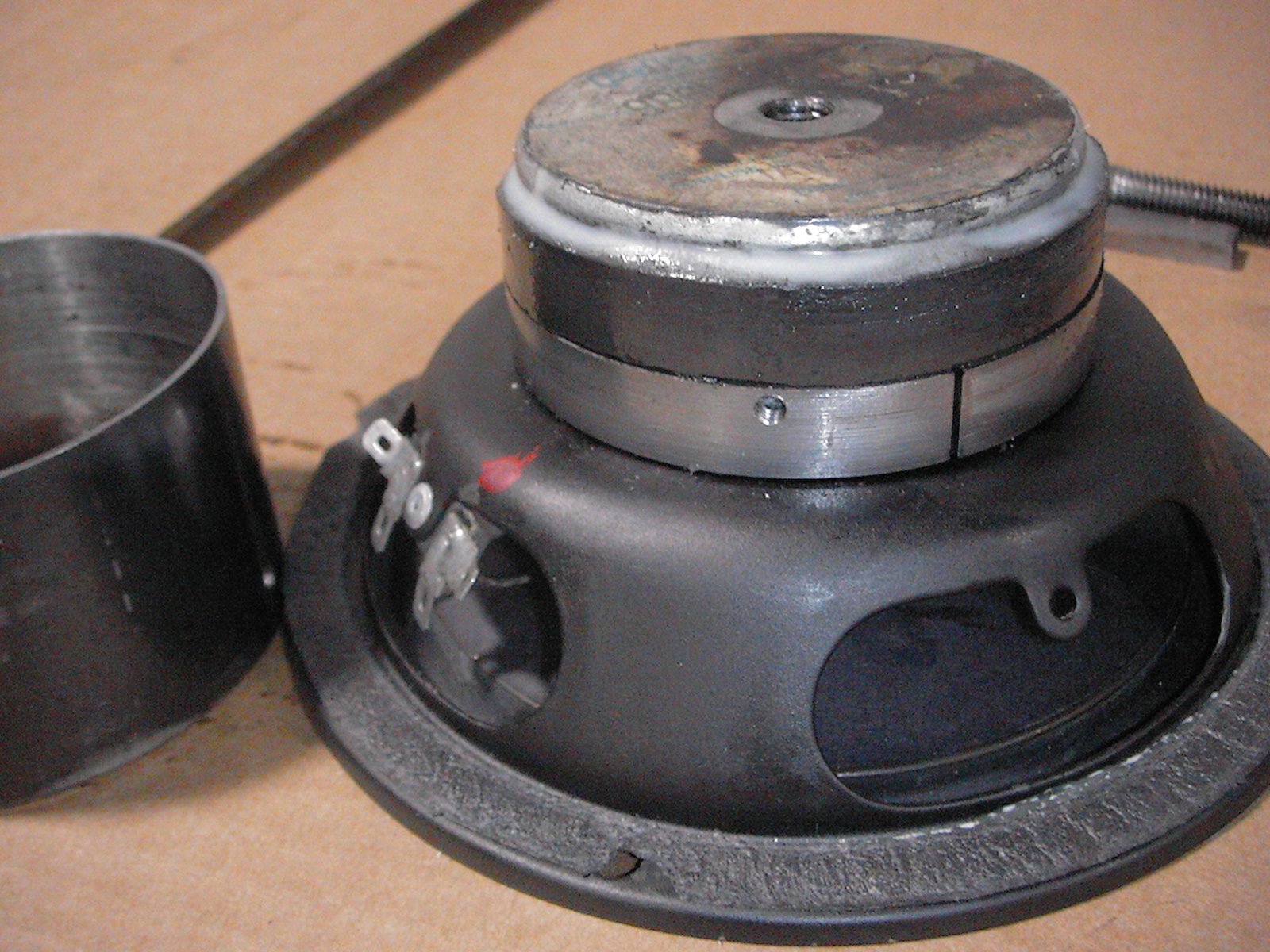
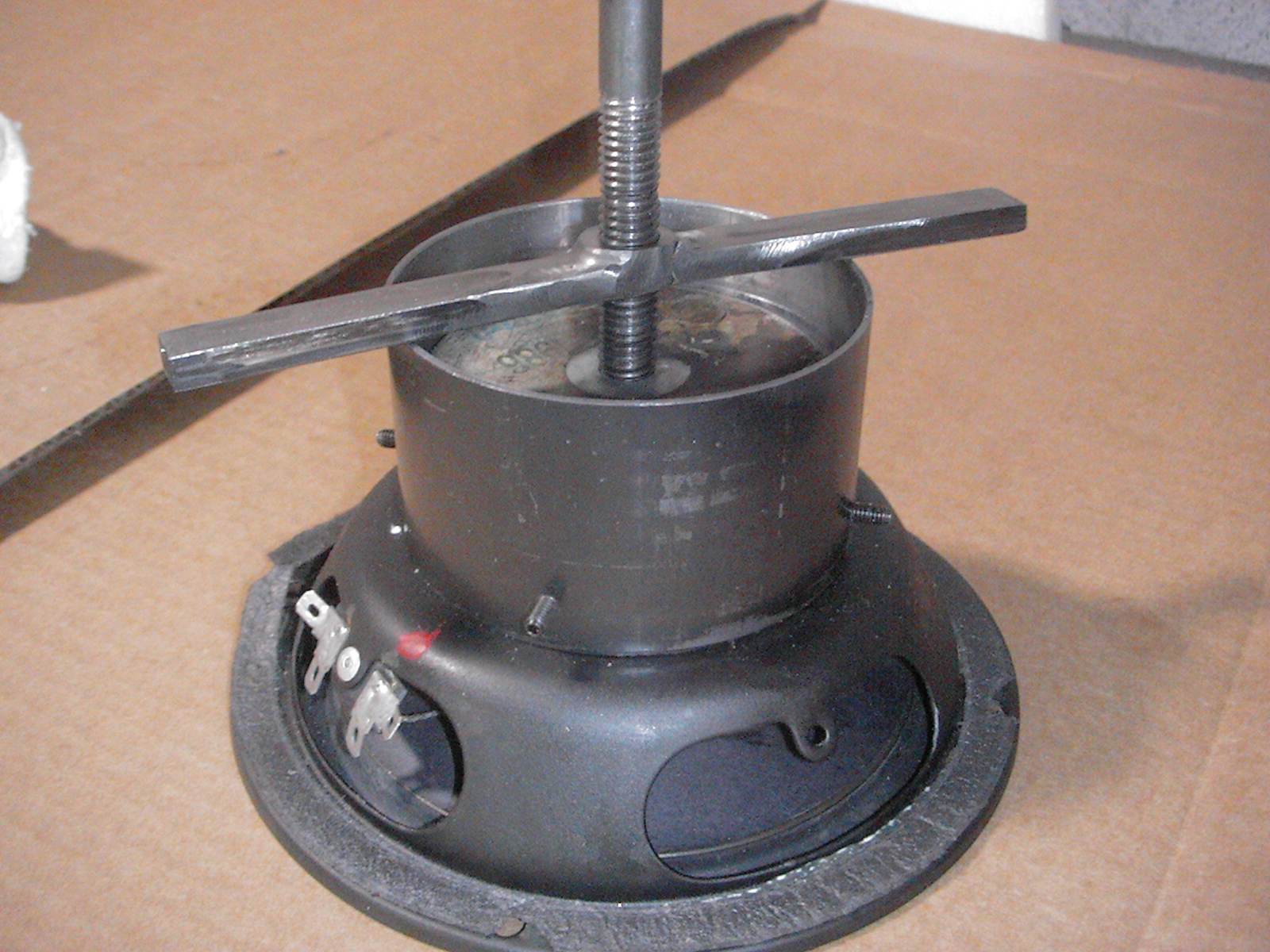
I then fabricated a piece that would allow me to lower the pole piece/magnet assembly down onto the basket. I took a 7/16"x14 " nut and welded two flat bars on each side. I inserted a 7/16''x14 bolt into the nut, screwed the bolt into the hole I previously drilled and tapped into the back of the poll piece. I put epoxy onto the bottom side of the magnet and carefully inserted the assembly into the 3.5" section of pipe (I coated the inside of the 3.5" pipe with machine oil to help the magnet assembly slide into place. I began to turn the nut with the "wings" until the magnet mated with the basket assembly. It went together perfectly with no rubbing. I let them dry over night.
I will be glad to answer any questions if I have not been fully clear on my directions.
I have a part time business restoring and repairing vintage stereo equipment. Recently I began restoration of a set of Monitor 7s. Both MW-6500s were locked up tight. They both ohmed out fine, but the magnets had definitely shifted, preventing the coils from moving.
I began first by separating the magnet and pole piece from each basket. I then went to thinking about the easiest way to line them back up and glue them in place without the voice coil rubbing. One of the great perks I have where I work is that I can do my "Government Projects" without any problems from the boss.
I knew that I had to glue the pole piece exactly in the center of the magnet hole. So I fabricated a piece of aluminum shaft to fit exactly inside diameter of the magnet hole. I then drilled out the center of the aluminum shaft the exact diameter of the pole piece.
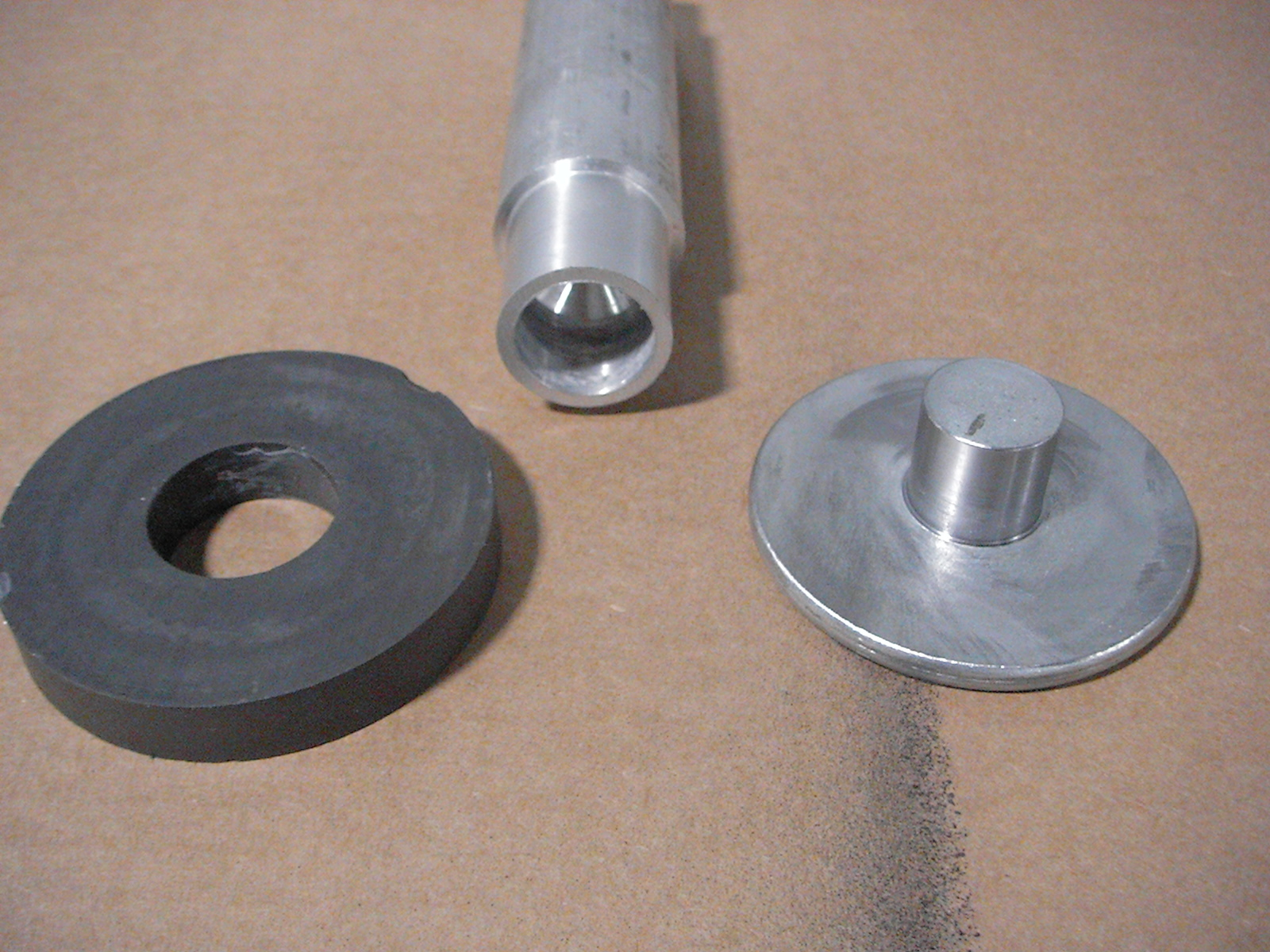
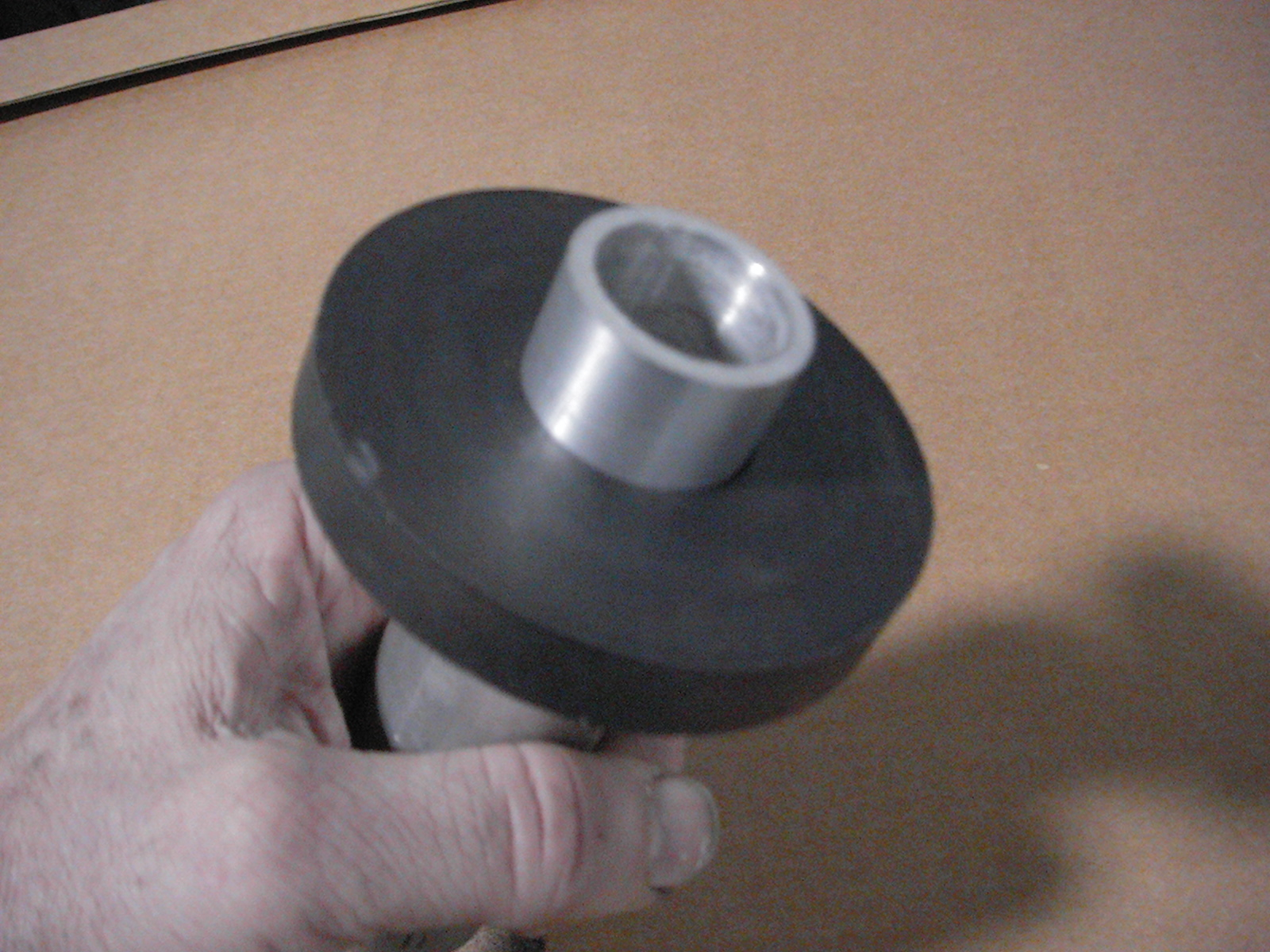
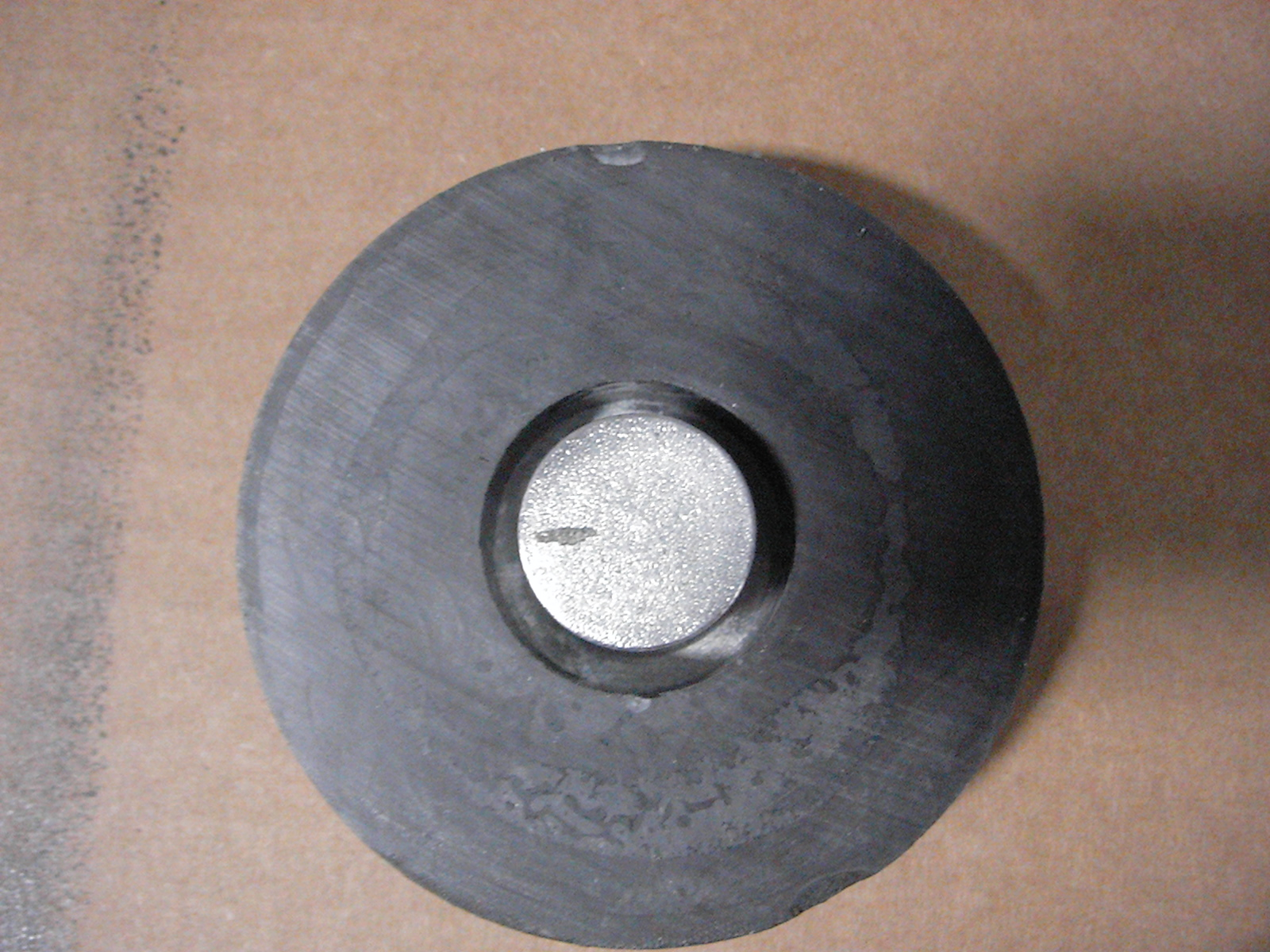
Before I glued the pole piece to the magnet, I drilled out the hole on the back of the pole piece so I could tap it with 7/16" x 14 threads. This was so I could hold it steady when I got to the point of joining the pole piece/magnet assembly to the basket.
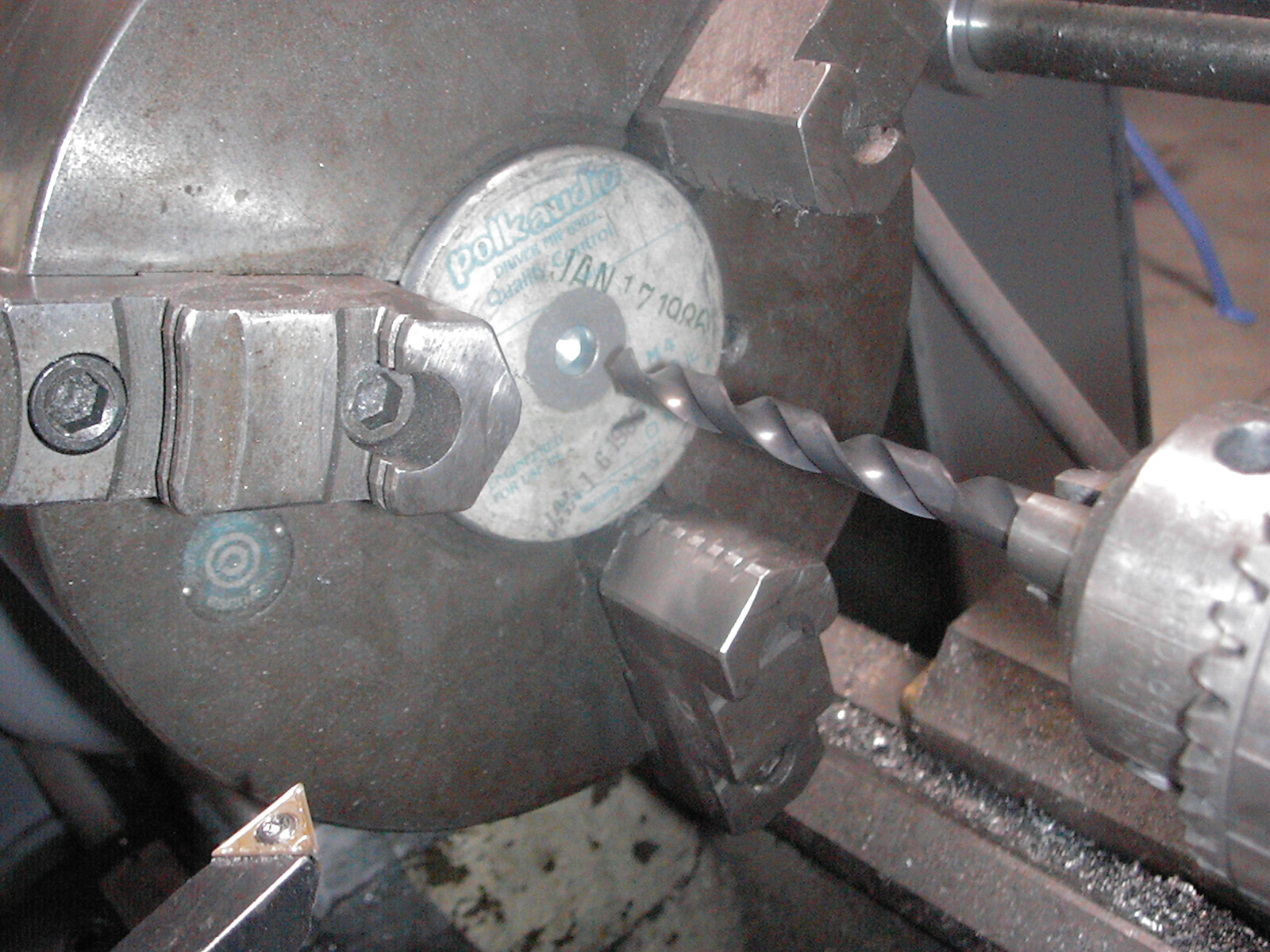
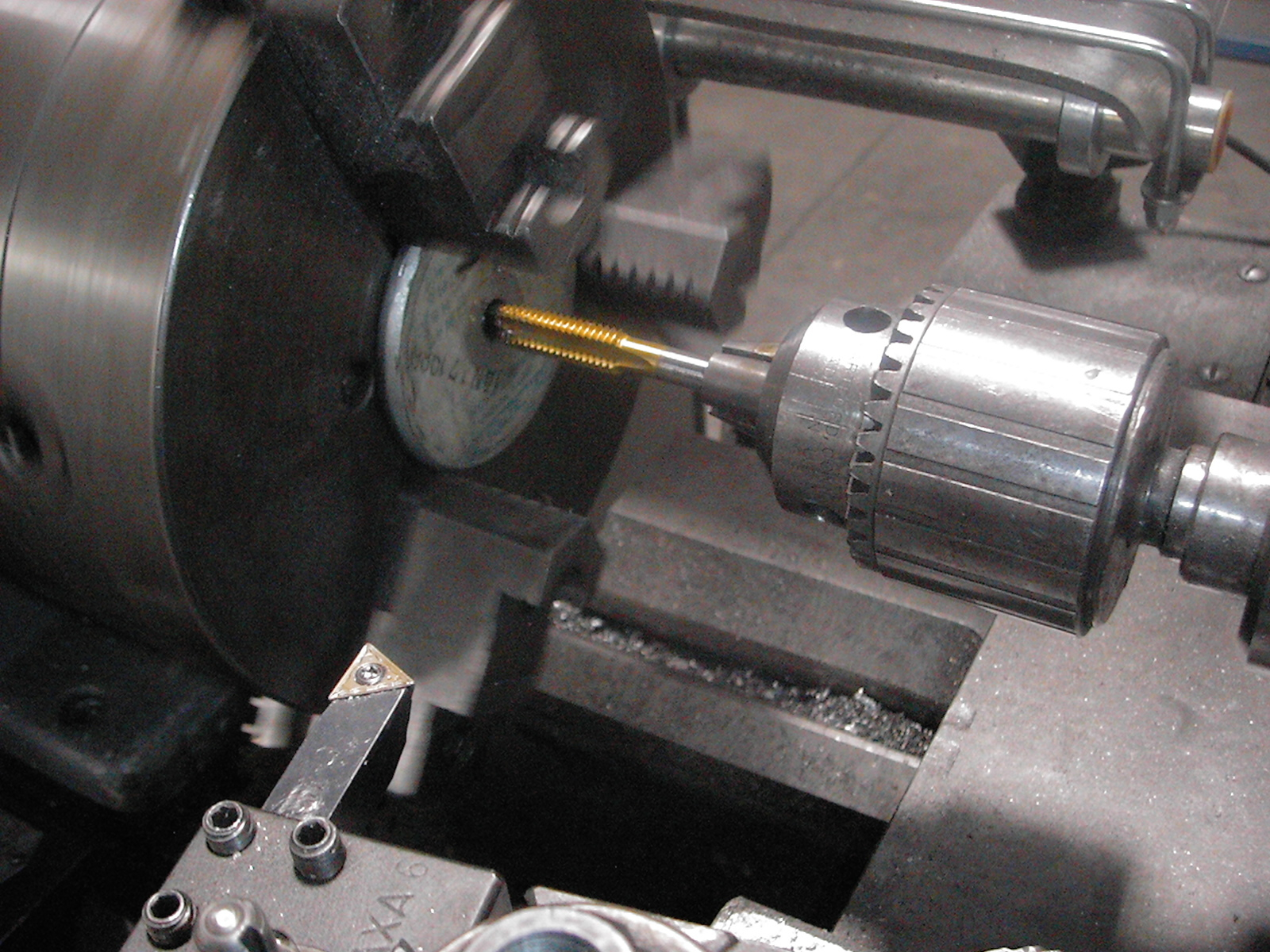
I have had pretty good luck using 3M 460 two part epoxy for gluing metal in the past, so I tried here also. I spread the glue evenly around the magnet's surface keeping it away from the center so it would not squeeze into the gap between the pole piece and the magnet.
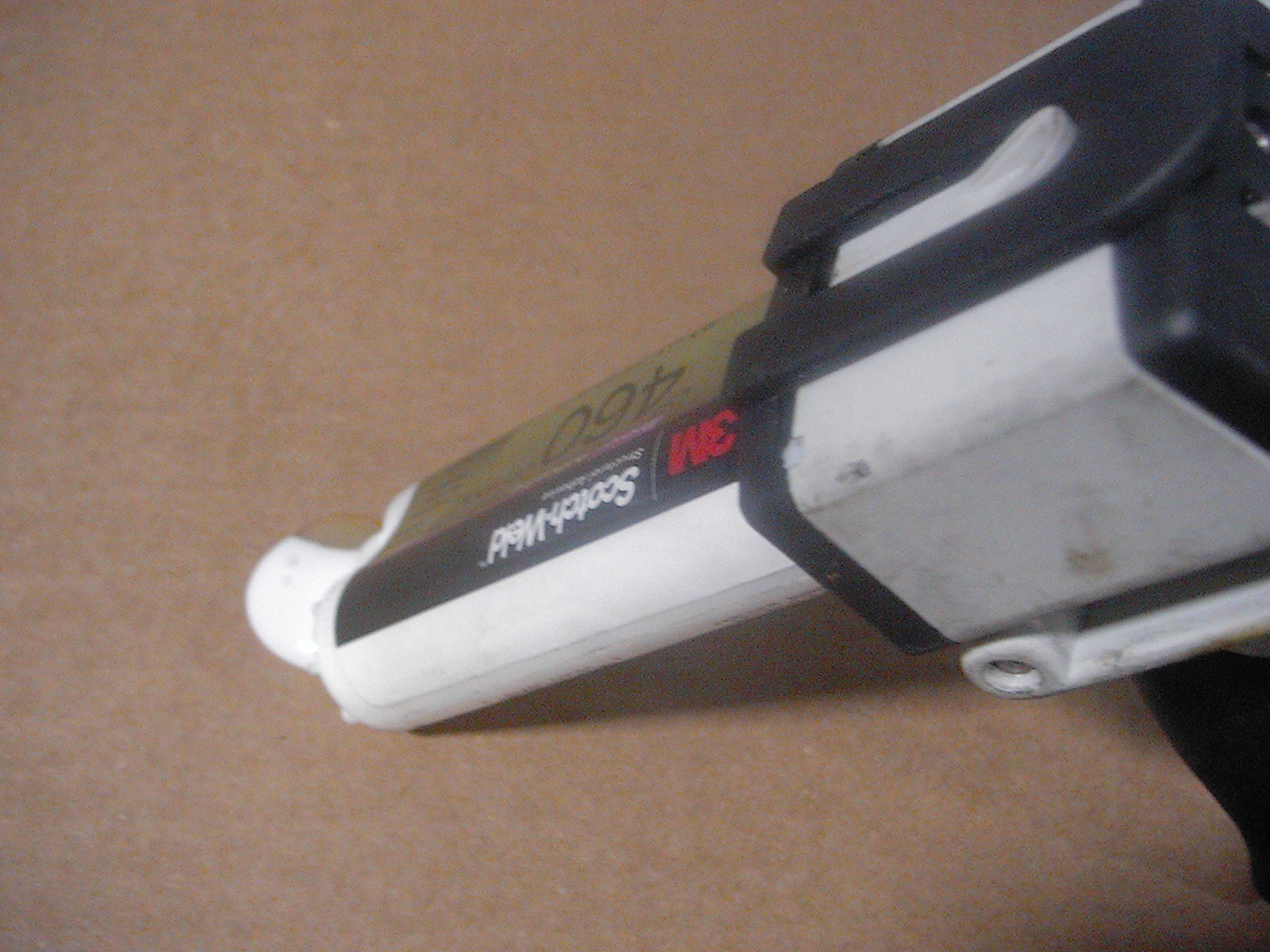
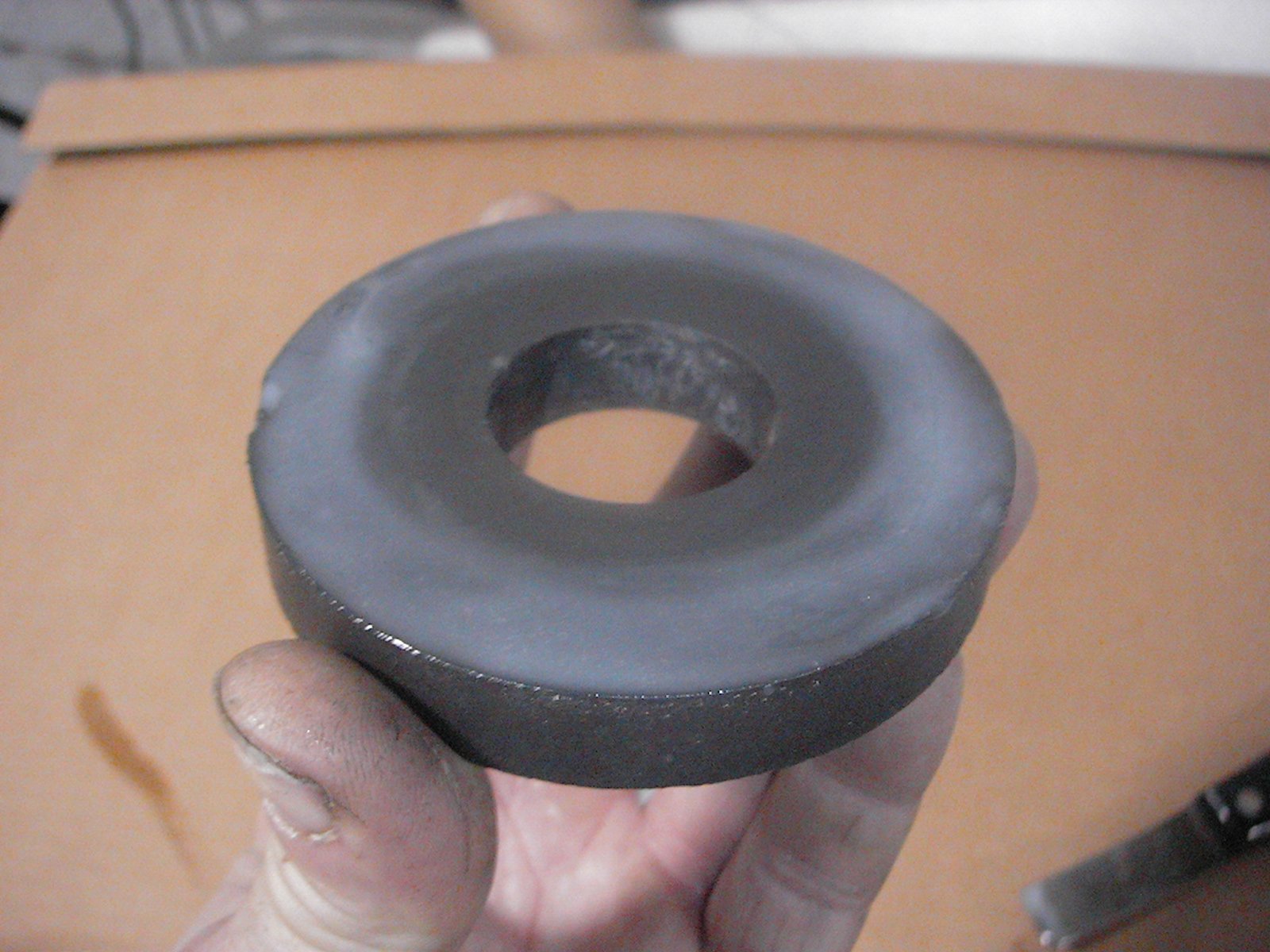
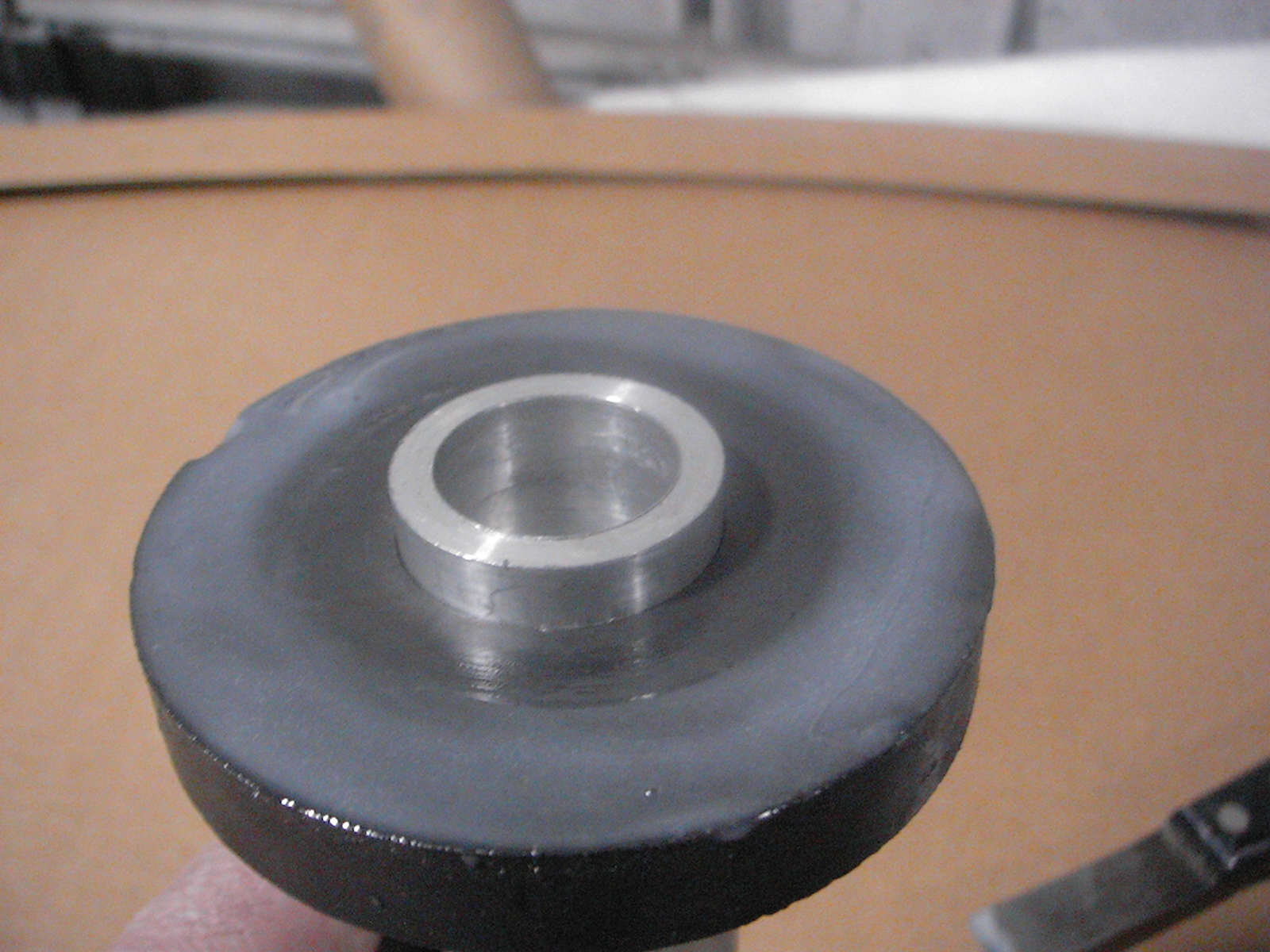
Once I glued them together, I then clamped them tight.
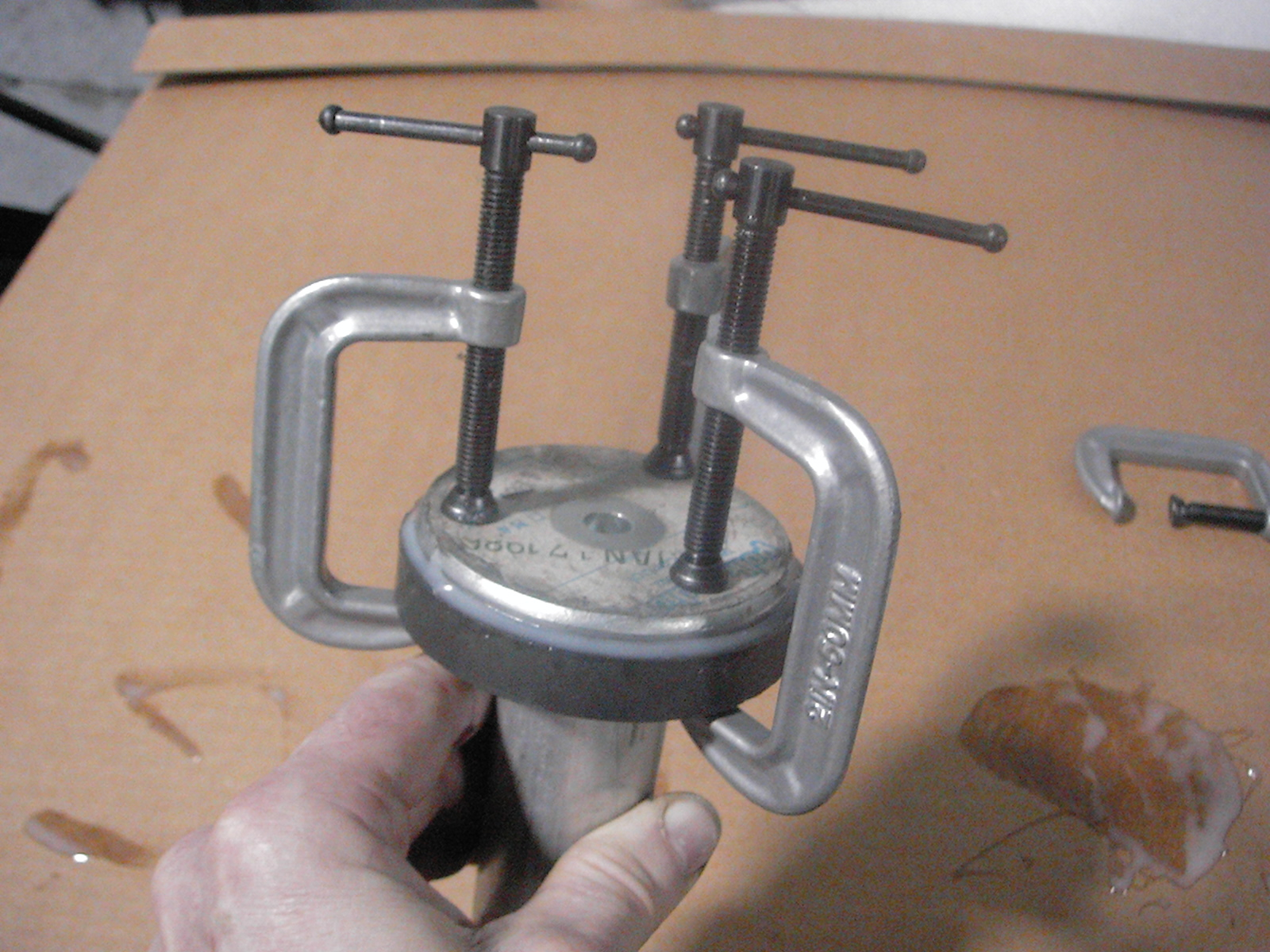
The next thing I had to do was make a way to join the pole piece/magnet assembly to the basket and get it perfectly centered. I took a piece of 3.5" o.d. steel pipe (I may should have used pvc, but I am a machinist by trade and not a plumber), and turned down the inside diameter to exactly fit the outside diameter of the magnet (appx. 3.375") and cut it off at 2" long. I then needed a way to center this to the back of the basket, around the steel disk with the hole in it for the voice coil. I took a piece of the same 3.5" o.d. pipe and turned down a section that would fit exactly around the steel disk attached to the basket (appx. 3" i.d). I then turned down the outside to fit the inside of the first section of pipe, (appx. 3.375). I cut this section .5" long and then inserted it into the 2" section of pipe at one end. I then drilled 4 holes 90 degrees apart all the way through both sections and tapped them to 10-32 threads. I then took the .5" section out of the 2" section and cut it in half so I could remove it once the epoxy had set.
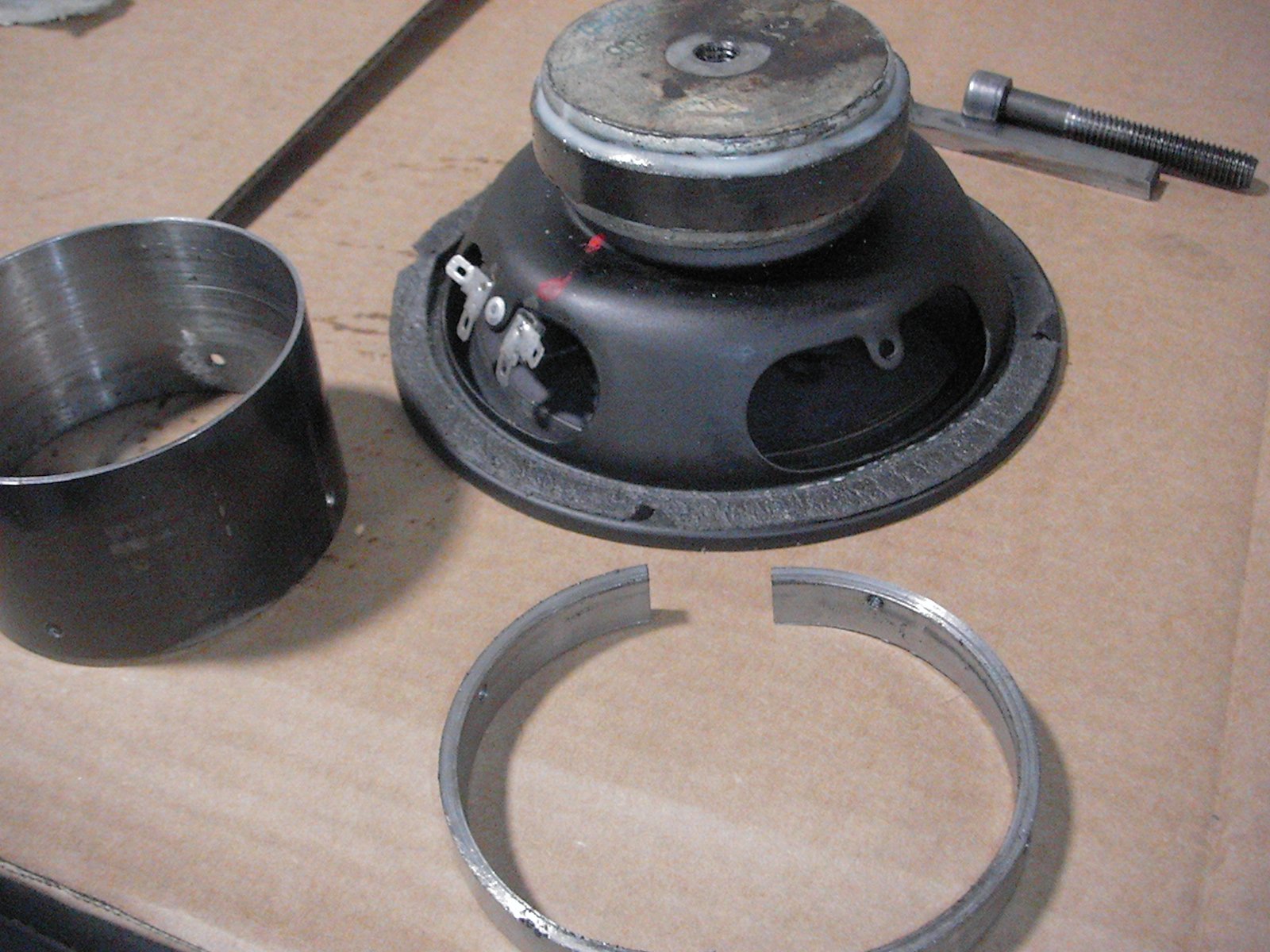
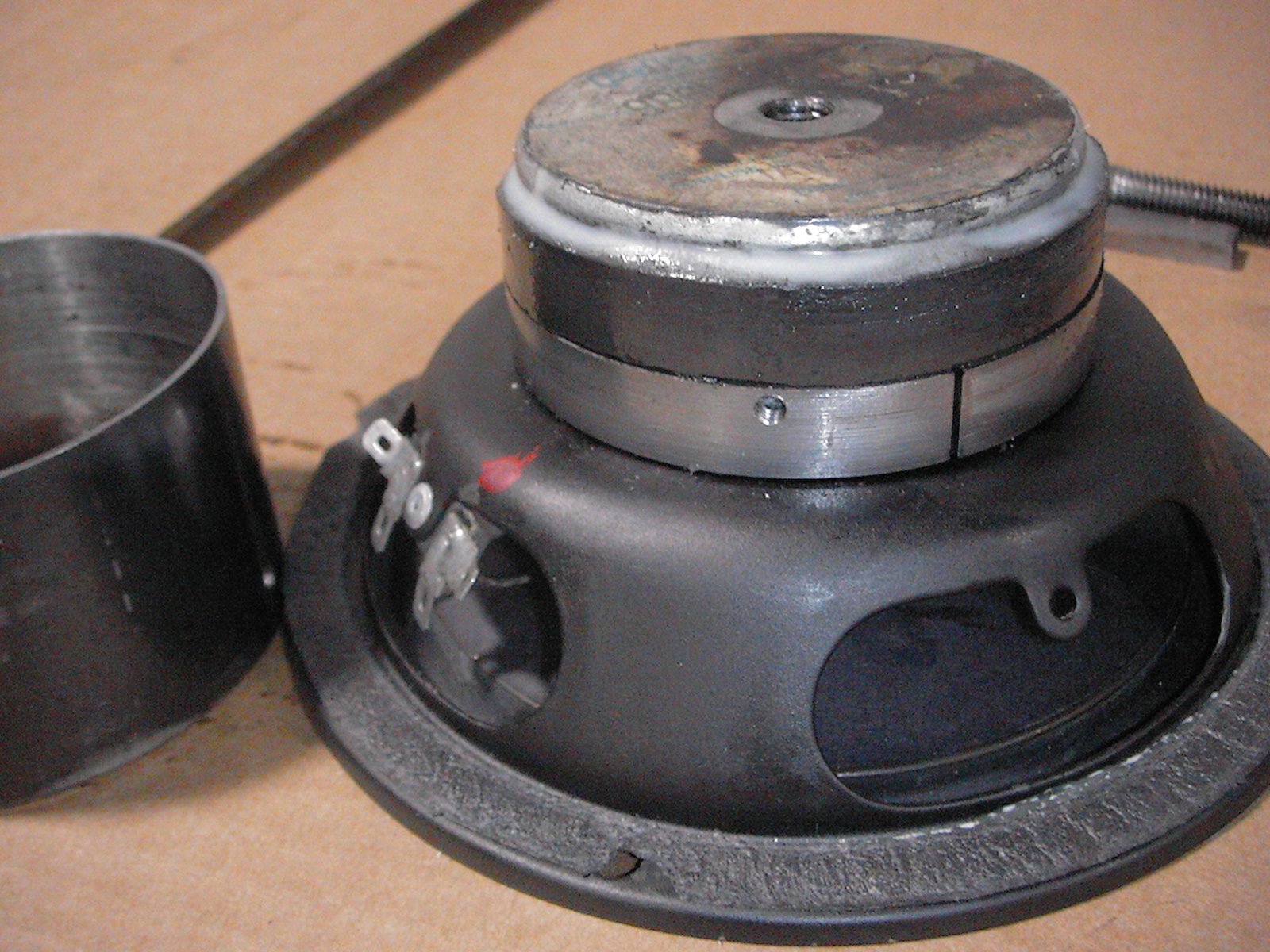
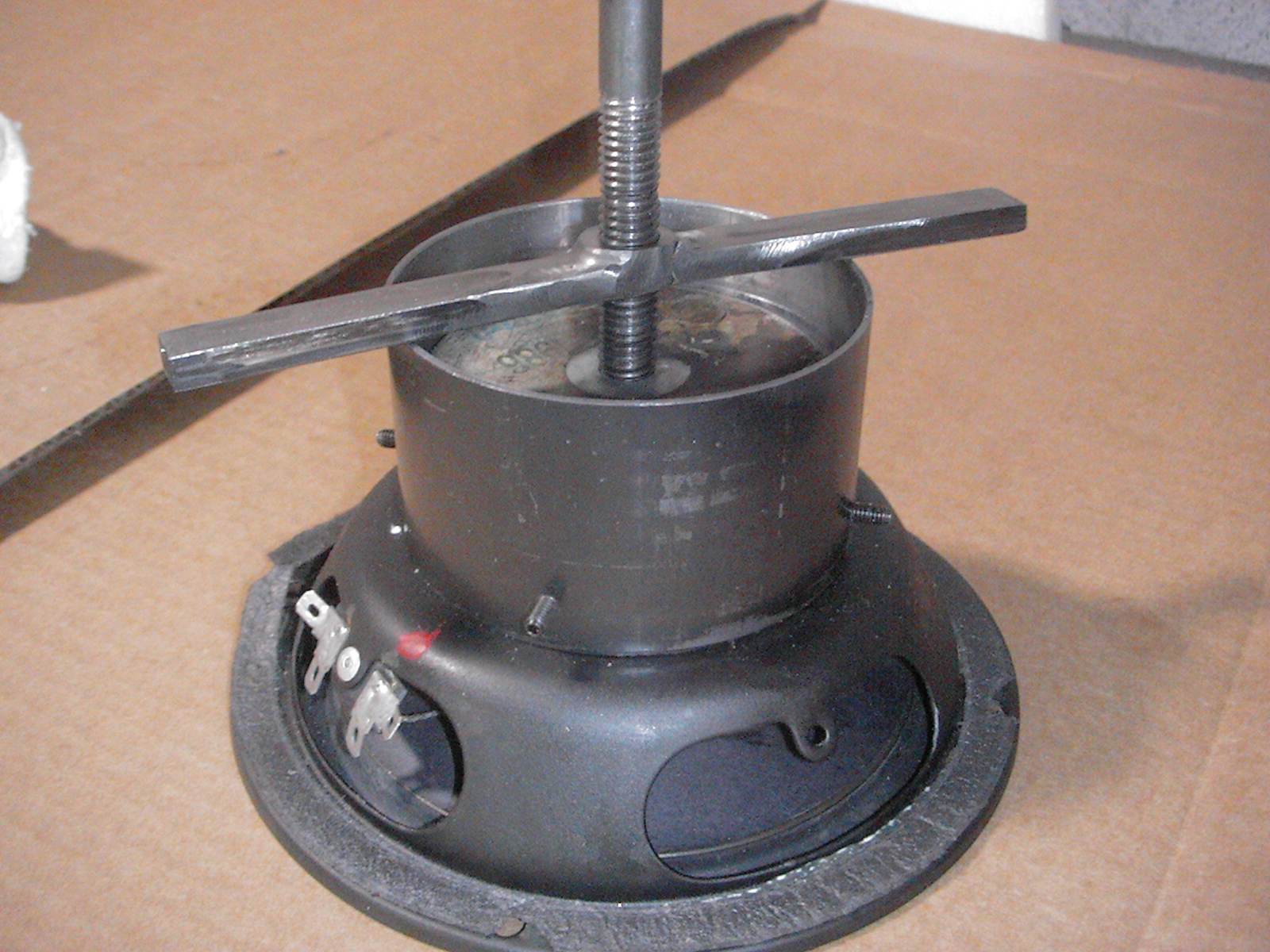
I then fabricated a piece that would allow me to lower the pole piece/magnet assembly down onto the basket. I took a 7/16"x14 " nut and welded two flat bars on each side. I inserted a 7/16''x14 bolt into the nut, screwed the bolt into the hole I previously drilled and tapped into the back of the poll piece. I put epoxy onto the bottom side of the magnet and carefully inserted the assembly into the 3.5" section of pipe (I coated the inside of the 3.5" pipe with machine oil to help the magnet assembly slide into place. I began to turn the nut with the "wings" until the magnet mated with the basket assembly. It went together perfectly with no rubbing. I let them dry over night.
I will be glad to answer any questions if I have not been fully clear on my directions.
Comments
-
I also have access to whatever equipment I need in my work and have made many jigs to get something done. My first thought is that what you made seems pretty good and would be a good fix jig but beyond the abilities of most. Now if you were to offer to use it to help out the polkies here for a little karma or fee, what a hero you’d be!Main System
Marantz AV8802A PrePro
Marantz MM7025 Amp rear surrounds
McIntosh MC7205 Amp center, ceiling and mid surrounds
McIntosh MC300 Amp front mains
Oppo 203 Bluray
Polk SDA-SRS with VR3 monastery crossovers
Polk FX1000 Mid surrounds
Klipsch RP-440C Center channel
Klipsch RP-15M Rear surrounds
SVS prime elevation ceiling surrounds
Rythmik F15HP sub
Samsung 8500 curved screen 65" LED 4K
Mac Mini Server
Office System
Musical Fidelity M6s dac/preamp
Oppo 103D Bluray
Polk SDA-SRS 2
Parasound HCA-1500A
Polk PSW 650 sub
Microrendu
Roku Ultra
Mac Mini Server -
Nice rig, but may I suggest a slight adjustment to your assembly? We can't assume the cone, spider or coil are perfectly centered on the basket, so start with adhering the magnet to the basket base plate, then drop the pole piece in with your jig and use set screws to set your coil clearanceat the pole plate. The magnet being perfectly centered to the pole or plate isn't as critical as the coil to pole clearance.
-
Wow, pretty impressive! The amount of work involved is a great reminder to perform preemptive gluing of the magnets, whenever possible, so that they never have to be re-aligned!! :-)
-
Nice rig, but may I suggest a slight adjustment to your assembly? We can't assume the cone, spider or coil are perfectly centered on the basket, so start with adhering the magnet to the basket base plate, then drop the pole piece in with your jig and use set screws to set your coil clearanceat the pole plate. The magnet being perfectly centered to the pole or plate isn't as critical as the coil to pole clearance.
Thank you for your response. If you look closely at the next to the last photo, you will see that the two piece ring is using the lower base plate as the center reference. When the larger pipe is slide down over it, the four set screws are tightened against that base plate and held perfectly center. -
Grandioso trabajo @downinmexico !Basement: Polk SDA SRS 1.2tl's, Cary SLP-05 Pre with ultimate upgrade,McIntosh MCD301 CD/SACD player, Northstar Designs Excelsio DAC, Cambridge 851N streamer, McIntosh MC300 Amp, Silnote Morpheus Ref2, Series2 Digital Cables, Silnote Morpheus Ref2 Series2 XLR's, Furman 15PFi Power Conditioner, Pangea Power Cables, MIT Shotgun S3 IC's, MIT Shotgun S1 Bi-Wire speaker cables
Office: PC, EAR Acute CD Player, EAR 834L Pre, Northstar Designs Intenso DAC, Antique Sound Labs AV8 Monoblocks, Denon UDR-F10 Cassette, Acoustic Technologies Classic FR Speakers, SVS SB12 Plus sub, MIT AVt2 speaker cables, IFI Purifier2, AQ Cinnamon USB cable, Groneberg Quatro Reference IC's
Spare Room: Dayens Ampino Integrated Amp, Tjoeb 99 tube CD player (modified Marantz CD-38), Analysis Plus Oval 9's, Zu Jumpers, AudioEngine B1 Streamer, Klipsch RB-61 v2, SVS PB1000 sub, Blue Jeans RCA IC's, Shunyata Hydra 8 Power Conditioner
Living Room: Peachtree Nova Integrated, Cambridge CXN v2 Streamer, Rotel RCD-1072 CD player, Furman 15PFi Power Conditioner, Polk RT265 In Wall Speakers, Polk DSW Pro 660wi sub
Garage #1: Cambridge Audio 640A Integrated Amp, Project Box-E BT Streamer, Polk Tsi200 Bookies, Douglas Speaker Cables, Shunyata Power Conditioner
Garage #2: Cambridge Audio EVO150 Integrated Amplifier, Polk L200's, Analysis Plus Silver Oval 2 Speaker Cables, IC's TBD. -
I also have access to whatever equipment I need in my work and have made many jigs to get something done. My first thought is that what you made seems pretty good and would be a good fix jig but beyond the abilities of most. Now if you were to offer to use it to help out the polkies here for a little karma or fee, what a hero you’d be!
Hello sbb2112. I do run a vintage audio repair/restoration business on the side and would love the opportunity to try this repair again just to know for sure if it can be consistently repeated.
-
motorcityguy wrote: »Wow, pretty impressive! The amount of work involved is a great reminder to perform preemptive gluing of the magnets, whenever possible, so that they never have to be re-aligned!! :-)
You are very correct motorcityguy! I have a set of Monitor 10s that I need to do some preventative maintenance on before the glue lets go on them also.
-
downinmexico wrote: »Nice rig, but may I suggest a slight adjustment to your assembly? We can't assume the cone, spider or coil are perfectly centered on the basket, so start with adhering the magnet to the basket base plate, then drop the pole piece in with your jig and use set screws to set your coil clearanceat the pole plate. The magnet being perfectly centered to the pole or plate isn't as critical as the coil to pole clearance.
Thank you for your response. If you look closely at the next to the last photo, you will see that the two piece ring is using the lower base plate as the center reference. When the larger pipe is slide down over it, the four set screws are tightened against that base plate and held perfectly center.
Yes, I noticed that, but what I'm saying is: one can't use the basket base plate as a reference because you can't assume that the cone/coil are glued to the basket perfectly centered. So, instead of pre gluing the magnet and pole piece, do that to the magnet and base plate. Then when the pole plate is installed, use the set screws to move just the pole in relation to the coil, not the whole magnet and pole assembly. Granted my rig uses the base plate as an anchor for the set screws, the jig floats around the magnet and only moves the pole plate. I'd prefer to be able to do it how you built it and set screw the pole plate itself, but I don't have access to a machinist lathe. -
downinmexico wrote: »Nice rig, but may I suggest a slight adjustment to your assembly? We can't assume the cone, spider or coil are perfectly centered on the basket, so start with adhering the magnet to the basket base plate, then drop the pole piece in with your jig and use set screws to set your coil clearanceat the pole plate. The magnet being perfectly centered to the pole or plate isn't as critical as the coil to pole clearance.
Thank you for your response. If you look closely at the next to the last photo, you will see that the two piece ring is using the lower base plate as the center reference. When the larger pipe is slide down over it, the four set screws are tightened against that base plate and held perfectly center.
Yes, I noticed that, but what I'm saying is: one can't use the basket base plate as a reference because you can't assume that the cone/coil are glued to the basket perfectly centered. So, instead of pre gluing the magnet and pole piece, do that to the magnet and base plate. Then when the pole plate is installed, use the set screws to move just the pole in relation to the coil, not the whole magnet and pole assembly. Granted my rig uses the base plate as an anchor for the set screws, the jig floats around the magnet and only moves the pole plate. I'd prefer to be able to do it how you built it and set screw the pole plate itself, but I don't have access to a machinist lathe.downinmexico wrote: »Nice rig, but may I suggest a slight adjustment to your assembly? We can't assume the cone, spider or coil are perfectly centered on the basket, so start with adhering the magnet to the basket base plate, then drop the pole piece in with your jig and use set screws to set your coil clearanceat the pole plate. The magnet being perfectly centered to the pole or plate isn't as critical as the coil to pole clearance.
Thank you for your response. If you look closely at the next to the last photo, you will see that the two piece ring is using the lower base plate as the center reference. When the larger pipe is slide down over it, the four set screws are tightened against that base plate and held perfectly center.
Yes, I noticed that, but what I'm saying is: one can't use the basket base plate as a reference because you can't assume that the cone/coil are glued to the basket perfectly centered. So, instead of pre gluing the magnet and pole piece, do that to the magnet and base plate. Then when the pole plate is installed, use the set screws to move just the pole in relation to the coil, not the whole magnet and pole assembly. Granted my rig uses the base plate as an anchor for the set screws, the jig floats around the magnet and only moves the pole plate. I'd prefer to be able to do it how you built it and set screw the pole plate itself, but I don't have access to a machinist lathe.
The base plate hole has to be centered with the voice coil or it would rub. When I was designing my jig, I took careful measurements with digital calipers the diameter of the coil, diameter of the base plate hole and the clearance around the outside of the coil and the inside of the base plate hole. Now I cant say for sure about any others as of yet, but with my two speakers, the voice coils were dead center in the middle of each base plate hole. I look forward to doing more of these, then I can know for sure if they are all centered exactly or not. -
downinmexico wrote: »motorcityguy wrote: »Wow, pretty impressive! The amount of work involved is a great reminder to perform preemptive gluing of the magnets, whenever possible, so that they never have to be re-aligned!! :-)
You are very correct motorcityguy! I have a set of Monitor 10s that I need to do some preventative maintenance on before the glue lets go on them also.
There is no better time than now on that one in my humble opinion. I thought I could get by a little longer on a set of M 5's one time....It turned out bad. -
downinmexico wrote: »downinmexico wrote: »Nice rig, but may I suggest a slight adjustment to your assembly? We can't assume the cone, spider or coil are perfectly centered on the basket, so start with adhering the magnet to the basket base plate, then drop the pole piece in with your jig and use set screws to set your coil clearanceat the pole plate. The magnet being perfectly centered to the pole or plate isn't as critical as the coil to pole clearance.
Thank you for your response. If you look closely at the next to the last photo, you will see that the two piece ring is using the lower base plate as the center reference. When the larger pipe is slide down over it, the four set screws are tightened against that base plate and held perfectly center.
Yes, I noticed that, but what I'm saying is: one can't use the basket base plate as a reference because you can't assume that the cone/coil are glued to the basket perfectly centered. So, instead of pre gluing the magnet and pole piece, do that to the magnet and base plate. Then when the pole plate is installed, use the set screws to move just the pole in relation to the coil, not the whole magnet and pole assembly. Granted my rig uses the base plate as an anchor for the set screws, the jig floats around the magnet and only moves the pole plate. I'd prefer to be able to do it how you built it and set screw the pole plate itself, but I don't have access to a machinist lathe.downinmexico wrote: »Nice rig, but may I suggest a slight adjustment to your assembly? We can't assume the cone, spider or coil are perfectly centered on the basket, so start with adhering the magnet to the basket base plate, then drop the pole piece in with your jig and use set screws to set your coil clearanceat the pole plate. The magnet being perfectly centered to the pole or plate isn't as critical as the coil to pole clearance.
Thank you for your response. If you look closely at the next to the last photo, you will see that the two piece ring is using the lower base plate as the center reference. When the larger pipe is slide down over it, the four set screws are tightened against that base plate and held perfectly center.
Yes, I noticed that, but what I'm saying is: one can't use the basket base plate as a reference because you can't assume that the cone/coil are glued to the basket perfectly centered. So, instead of pre gluing the magnet and pole piece, do that to the magnet and base plate. Then when the pole plate is installed, use the set screws to move just the pole in relation to the coil, not the whole magnet and pole assembly. Granted my rig uses the base plate as an anchor for the set screws, the jig floats around the magnet and only moves the pole plate. I'd prefer to be able to do it how you built it and set screw the pole plate itself, but I don't have access to a machinist lathe.
The base plate hole has to be centered with the voice coil or it would rub. When I was designing my jig, I took careful measurements with digital calipers the diameter of the coil, diameter of the base plate hole and the clearance around the outside of the coil and the inside of the base plate hole. Now I cant say for sure about any others as of yet, but with my two speakers, the voice coils were dead center in the middle of each base plate hole. I look forward to doing more of these, then I can know for sure if they are all centered exactly or not.
I have also re centered / glued a few. I wanted to know how I did so, off with the dust cap/cover..Lookie in there...Now I could see ! I did great btw. Lol. Very, Very nice rig. -
Hey VSAT88m thanks for the reply! I just finished applying epoxy to my monitor 10s. Now I need to do my Monitor 5jrs.
-
mr downinmexico, i am in dire need of your services or renting you jig set up.
i just picked up a pair of sda1 signature edition the drivers are mw6600x but i think they are all the same physical size (SDA FAMILY).
but anyway about 6 are frozen. is there any way you could help with this issue, as i have no longer access to a machine shop. thanks in advance.
jim in NJ -
also you can directly reach me at jbslomian@verizon.net
-
@downinmexico
There are another few of us here who can get you fixed if he doesn't respond in a few days. -
mr downinmexico, i am in dire need of your services or renting you jig set up.
i just picked up a pair of sda1 signature edition the drivers are mw6600x but i think they are all the same physical size (SDA FAMILY).
but anyway about 6 are frozen. is there any way you could help with this issue, as i have no longer access to a machine shop. thanks in advance.
jim in NJ
Hello Jim, I will send you an email shortly. -
mr down in mexico... i have my drivers all packed up and ready to ship to you , im just waiting for a go ahead from you, jim
-
@sslome if you put @ in front of the person whom you are trying to address, it sends them an automatic notification.
@downinmexico -
Super jealous of your lathe!
my 3.1TLs
I will fix your shifted magnets for free. -
I to have a pair of sda 6509 speakers with being frozen up here in ky no one will attempt repair, almost ready to buy another set just for speakers any help 😁 would be appreciated
-
darrel440644 wrote: »I to have a pair of sda 6509 speakers with being frozen up here in ky no one will attempt repair, almost ready to buy another set just for speakers any help 😁 would be appreciated
Good luck on buying another set they're pretty rare.
There are two here that have had good luck fixing. -
I found the following parameters for the MW6509.
MW 6509
Q 2.1
BL 4.57 N
Compliance 3.54 E-3 N/M
DC Resistance 8.97 Ohms
FS 30 HertzStan
Main 2ch:
Polk LSi15 (DB840 upgrade), Parasound: P/LD-1100, HCA-1000A; Denon: DVD-2910, DRM-800A; Benchmark DAC1, Monster HTS3600-MKII, Grado SR-225i; Technics SL-J2, Parasound PPH-100.
HT:
Marantz SR7010, Polk: RTA11TL (RDO198-1, XO and Damping Upgrades), S4, CS250, PSW110 , Marantz UD5005, Pioneer PL-530, Panasonic TC-P42S60
Other stuff:
Denon: DRA-835R, AVR-888, DCD-660, DRM-700A, DRR-780; Polk: S8, Monitor 5A, 5B, TSi100, RM7, PSW10 (DXi104 upgrade); Pioneer: CT-6R; Onkyo CP-1046F; Ortofon OM5E, Marantz: PM5004, CD5004, CDR-615; Parasound C/PT-600, HCA-800ii, Sony CDP-650ESD, Technics SA 5070, B&W DM601 -
There is an MW6509 in the FS section.Stan
Main 2ch:
Polk LSi15 (DB840 upgrade), Parasound: P/LD-1100, HCA-1000A; Denon: DVD-2910, DRM-800A; Benchmark DAC1, Monster HTS3600-MKII, Grado SR-225i; Technics SL-J2, Parasound PPH-100.
HT:
Marantz SR7010, Polk: RTA11TL (RDO198-1, XO and Damping Upgrades), S4, CS250, PSW110 , Marantz UD5005, Pioneer PL-530, Panasonic TC-P42S60
Other stuff:
Denon: DRA-835R, AVR-888, DCD-660, DRM-700A, DRR-780; Polk: S8, Monitor 5A, 5B, TSi100, RM7, PSW10 (DXi104 upgrade); Pioneer: CT-6R; Onkyo CP-1046F; Ortofon OM5E, Marantz: PM5004, CD5004, CDR-615; Parasound C/PT-600, HCA-800ii, Sony CDP-650ESD, Technics SA 5070, B&W DM601 -
Did you write down the exact O.D. of the pole piece by chance? I'm starting a project and don't want to tear apart a good MW to get the dimension. Thanks much.Don't take experimental gene therapies from known eugenicists.
-
Did you write down the exact O.D. of the pole piece by chance? I'm starting a project and don't want to tear apart a good MW to get the dimension. Thanks much.
I have done several of these so far and have found two different pole piece diameters. One was .965 and the other was .995 -
Which driver?
I measured a 6500 pole piece at 25.39mm +/- whatever to account for my calipers being from harbor freight.
I've learned via all my re-centering that various drivers have different sized pole pieces, most slightly, some not slightly different.my 3.1TLs
I will fix your shifted magnets for free. -
Which driver?
I measured a 6500 pole piece at 25.39mm +/- whatever to account for my calipers being from harbor freight.
I've learned via all my re-centering that various drivers have different sized pole pieces, most slightly, some not slightly different.
.995" is 25.273mm. May be the difference between calipers. I dont remember which drivers they were. -
downinmexico wrote: »Which driver?
I measured a 6500 pole piece at 25.39mm +/- whatever to account for my calipers being from harbor freight.
I've learned via all my re-centering that various drivers have different sized pole pieces, most slightly, some not slightly different.
.995" is 25.273mm. May be the difference between calipers. I dont remember which drivers they were.
A 6509 pole I have piece measured 25.28mm, so that matches.my 3.1TLs
I will fix your shifted magnets for free. -
Thanks guys, I thought I remember them being shy a few thousandths of an inch.Don't take experimental gene therapies from known eugenicists.
-
Hey Lawdogg. Are all the MWs that you've come across have the same 0.375" diameter centering divet/hole on the back of their pole pieces?Don't take experimental gene therapies from known eugenicists.