HD650/600 cable build. The Halo Silver Edition.

ALL212
Posts: 1,577
in Headphones
Fellow Pokie Halo asked me to build an HD650 cable for his incoming HD6XX's. He picked the parts (with some prompting and referencing agfrost's build) and all parts finally arrived.
The Recipe:
Mogami W2534 cable - 11 feet
Soft techflex - about 10 feet
1/4" plug from Eidolic
Y thingy from Eidolic
Furutech FT-2PS headphone connector
various heatshrinks
The cotton stuff was not used, it just don't fit...
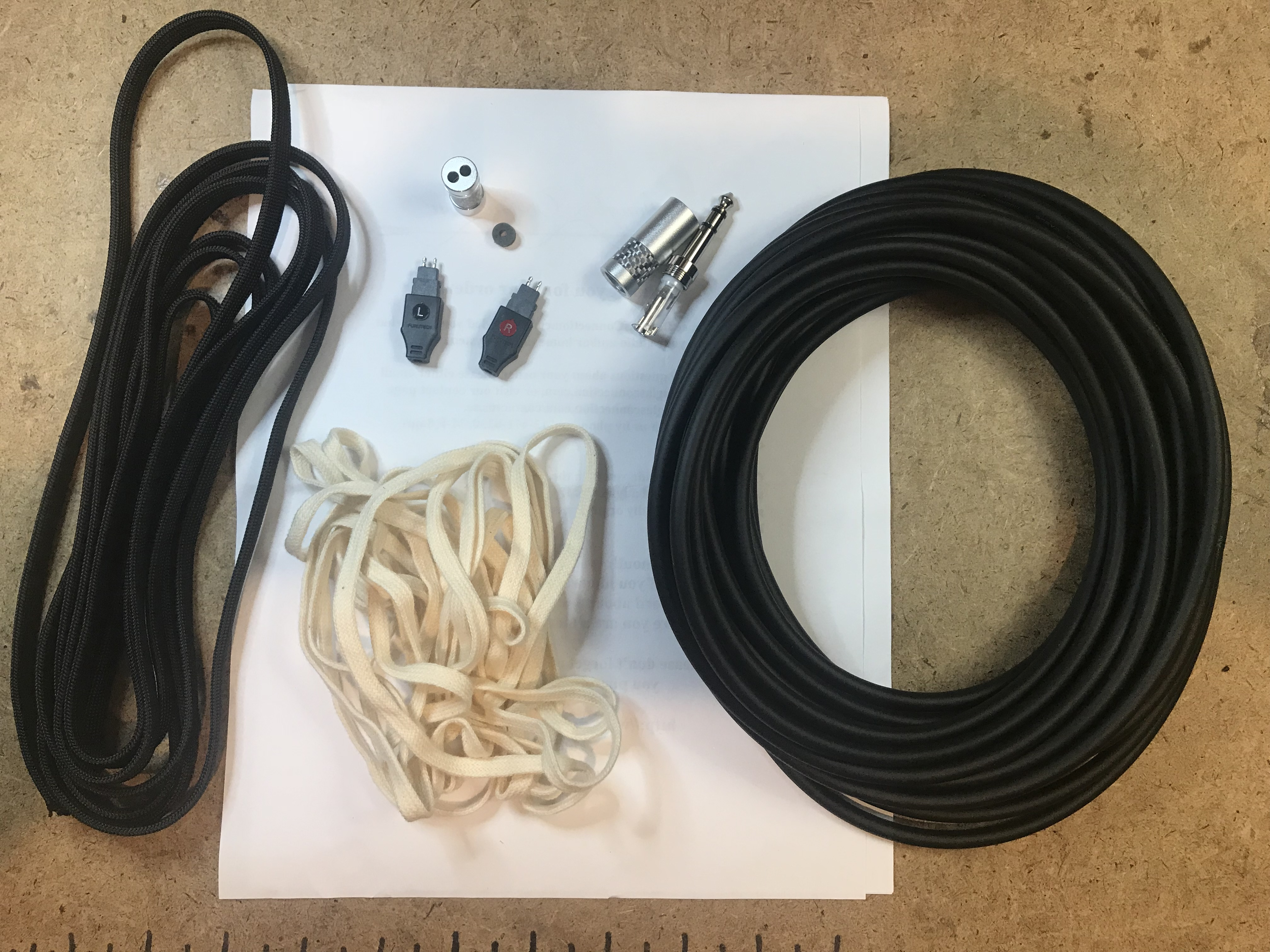
Tools:
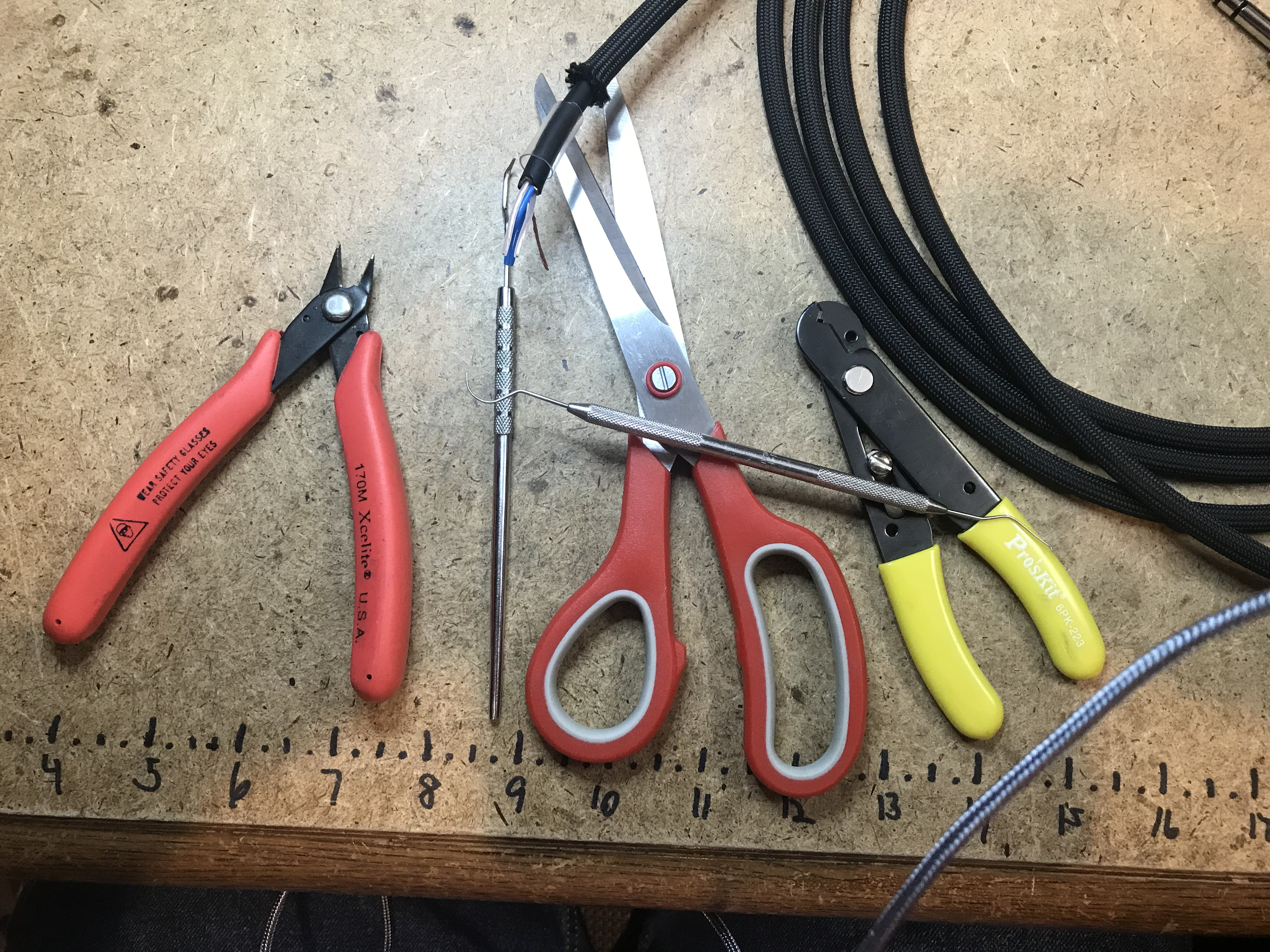
As mentioned in another thread the techflex is the softer cloth type but it doesn't "shrink" as you push it onto the cable so it does take some time and patience to get it threaded on. I pulled it through the entire cable, then sat and thought about it.
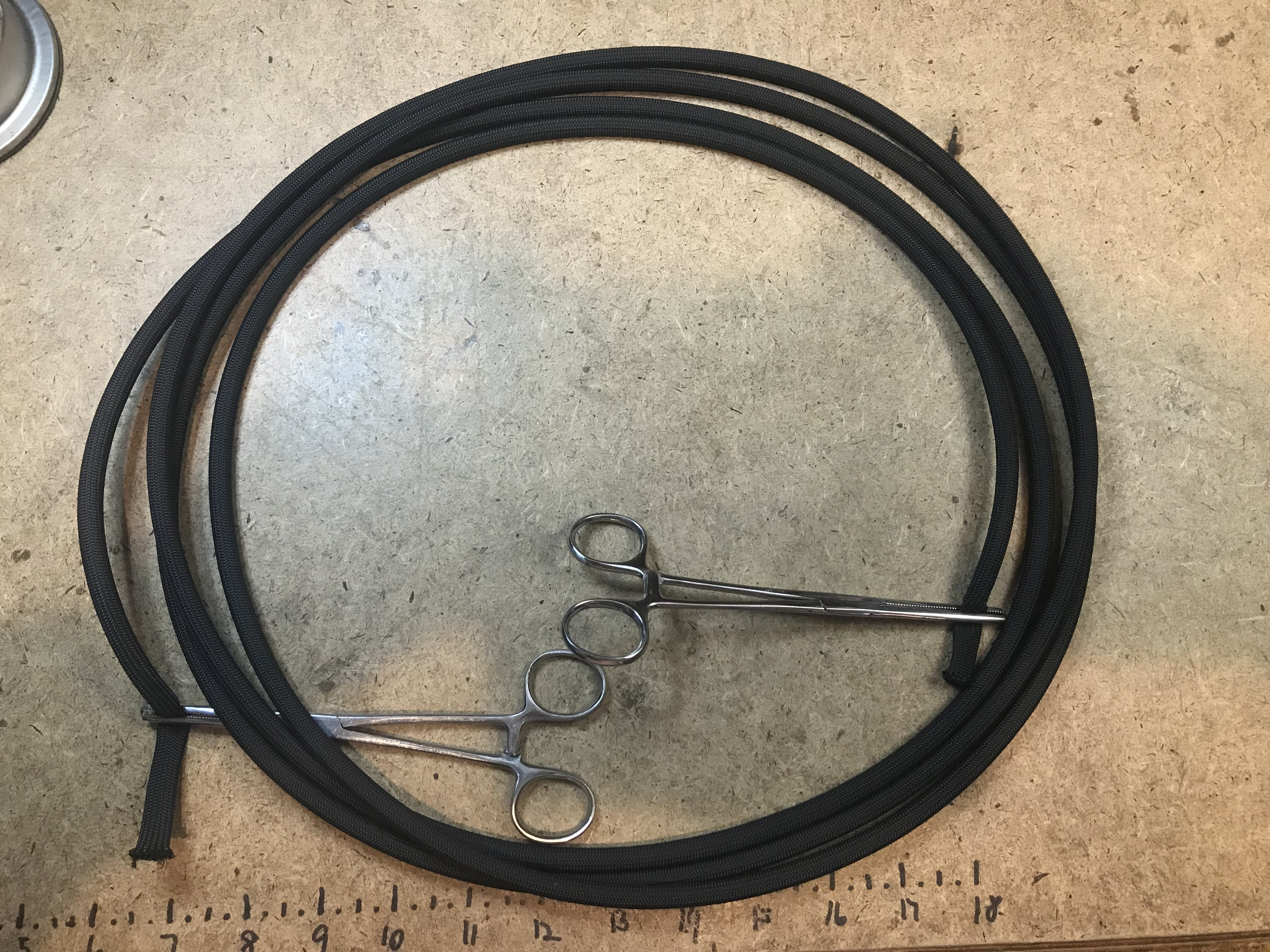
I measured the distance I needed the Y (about 14") + the amount I needed to clear on the 1/4 plug end (about 1 1/2) and pulled that amount back off and cut it. You'll need a good scissors. Then I pulled it back on to where I wanted it and left it alone.
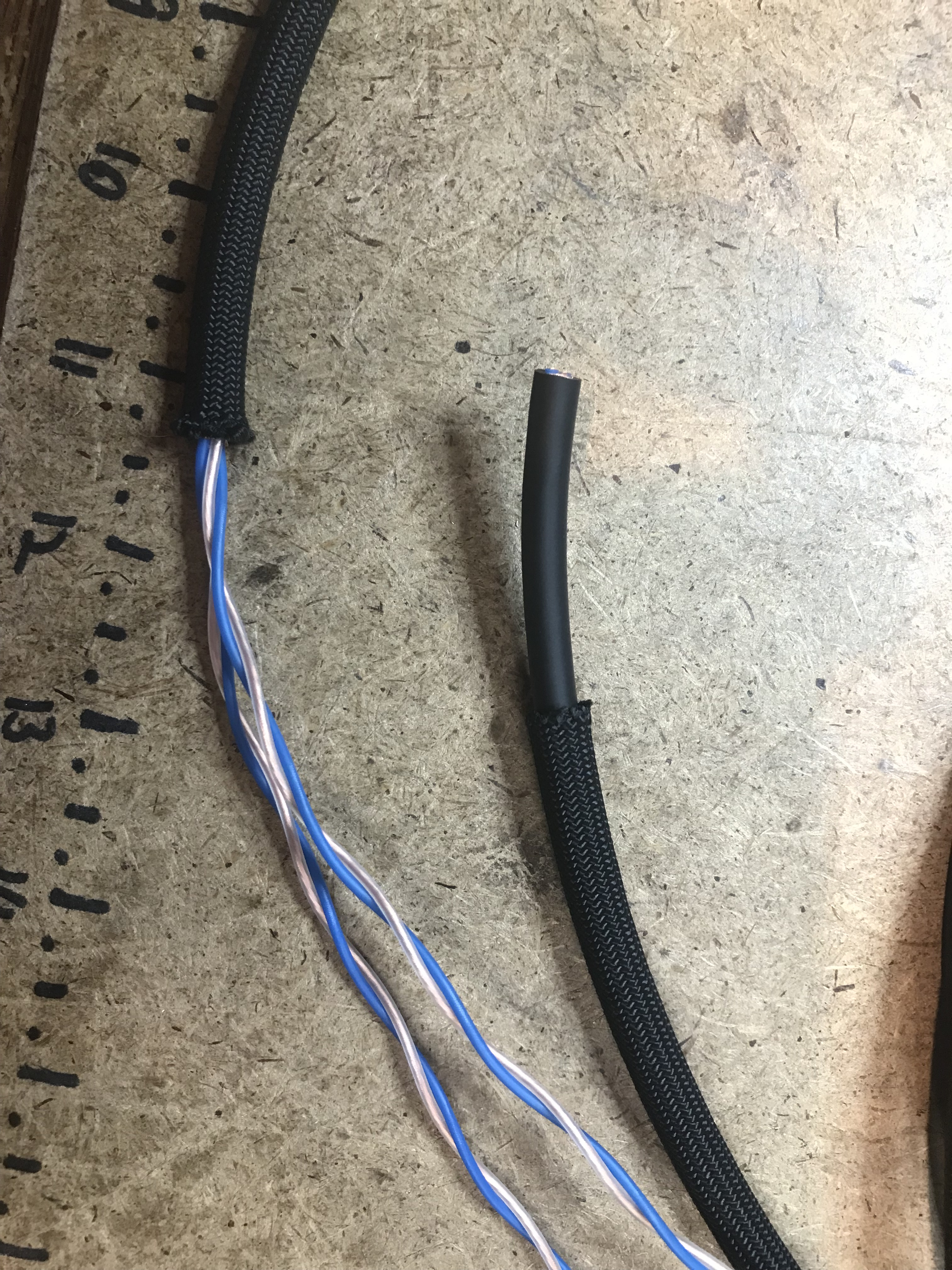
I stripped the Y end first and removed the shield but then moved to the easy end.
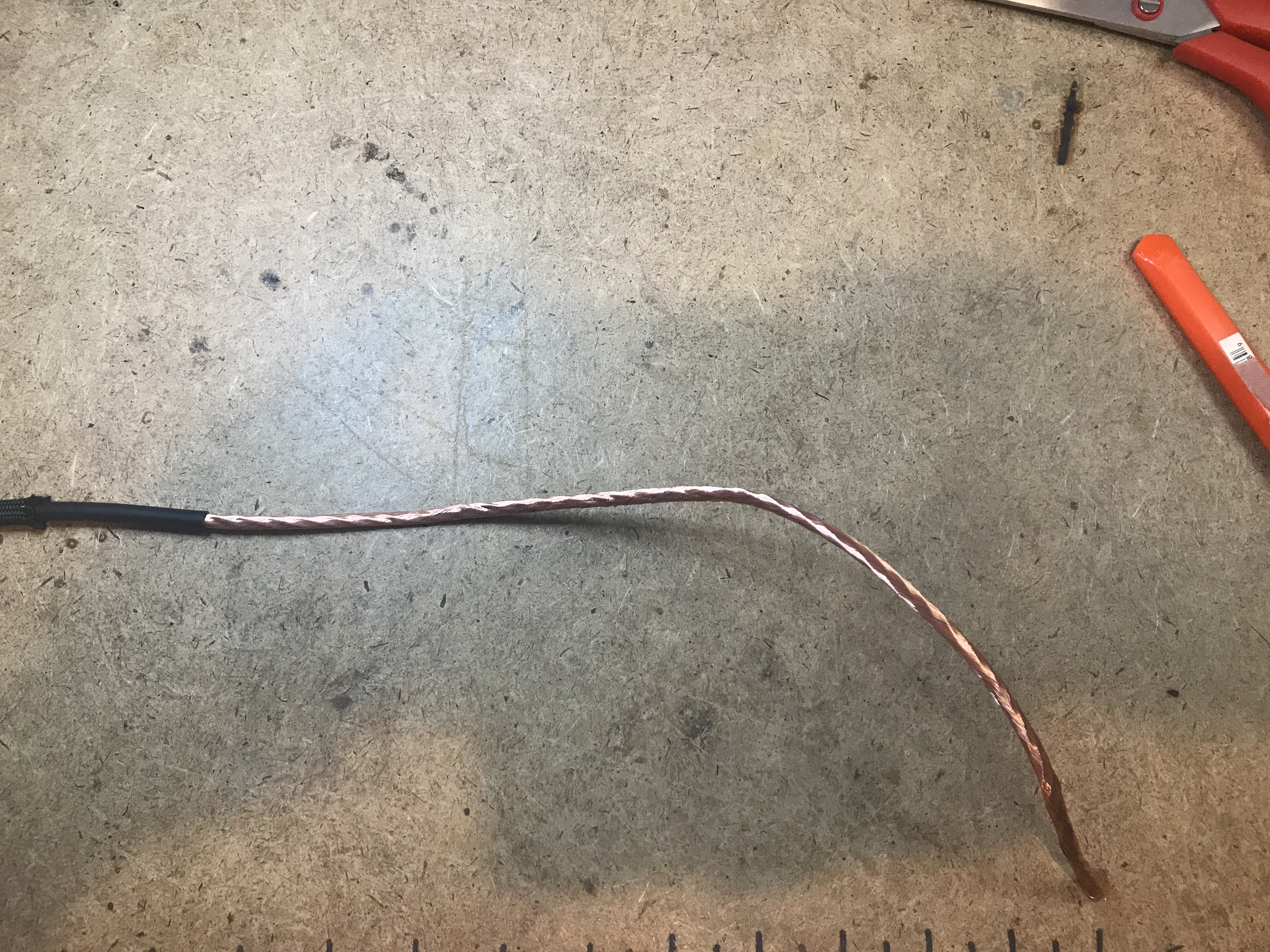
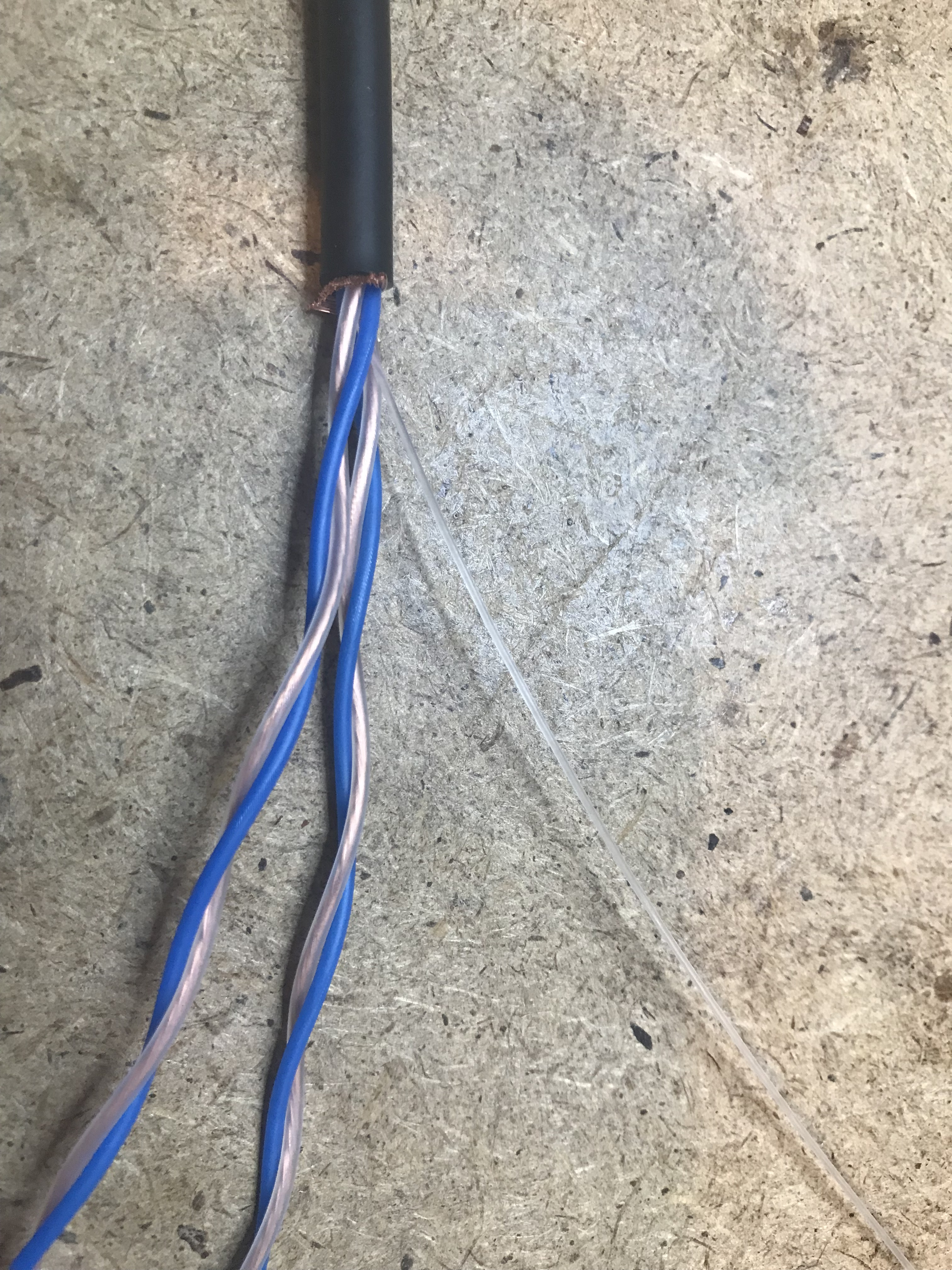
The Eidolic is a fairly easy connector to work with. I opened up the ground pole hole with a small file I use just for that purpose and got the tinned grounds through it with no issues.
Don't forget to thread on your backshell, heat shrink and the clear plastic insulator before soldering.
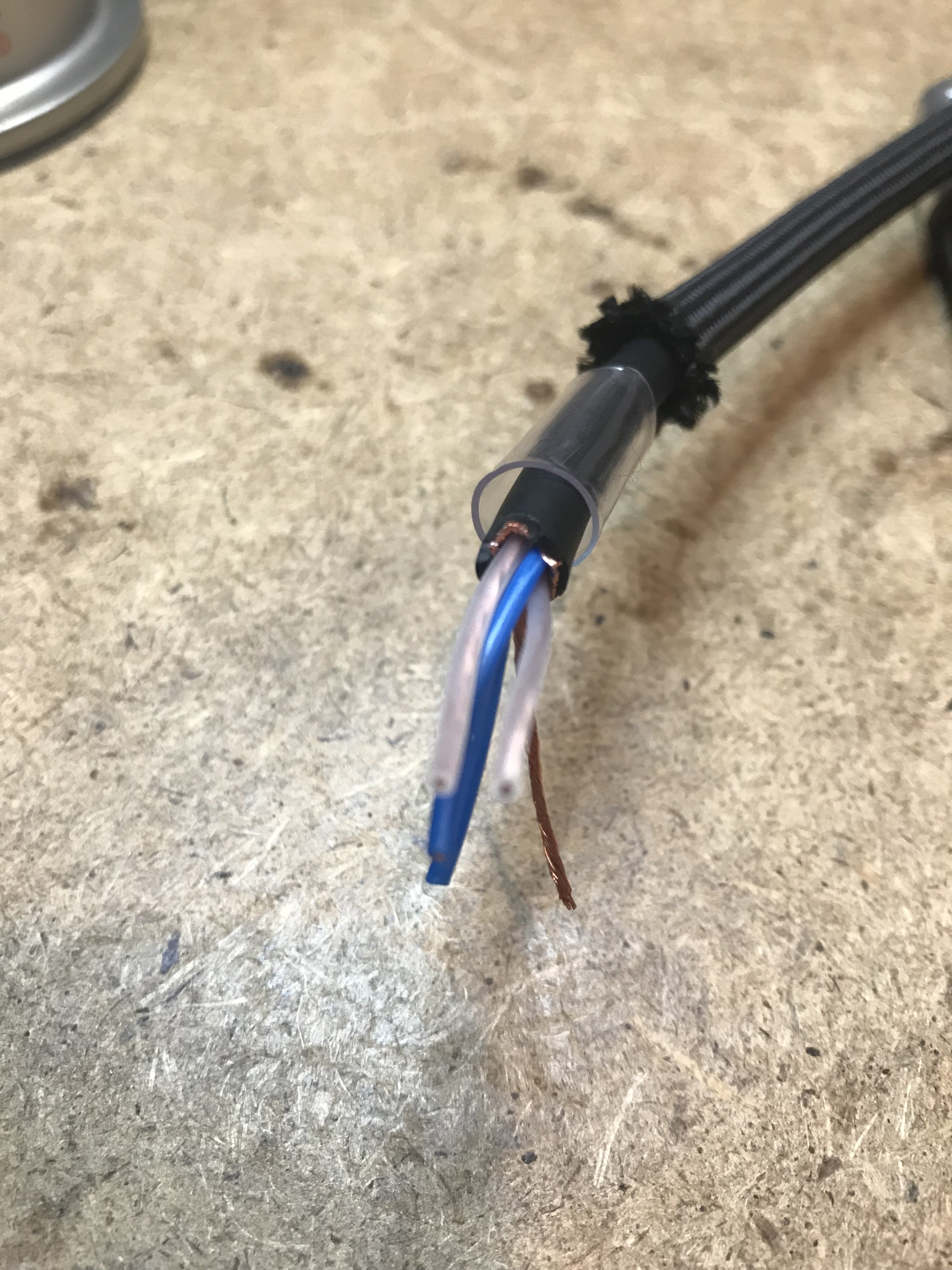
Tin the ends (solder together the naked copper wires). This will keep stray strands from escaping and shorting stuff out later. It also makes it much easier to solder this together.
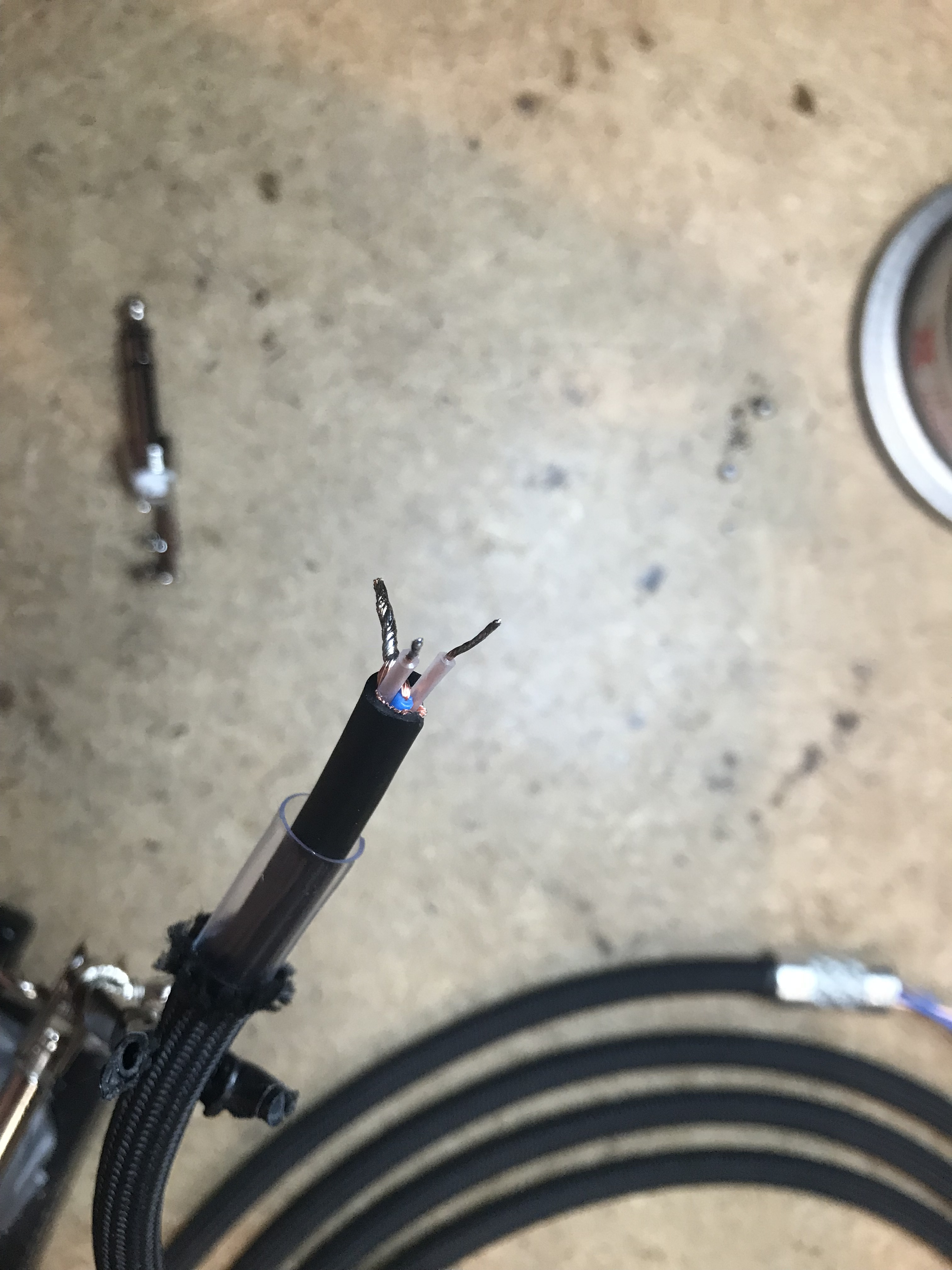
I put it all together before soldering. I do use a bit of shield combined with the grounds.
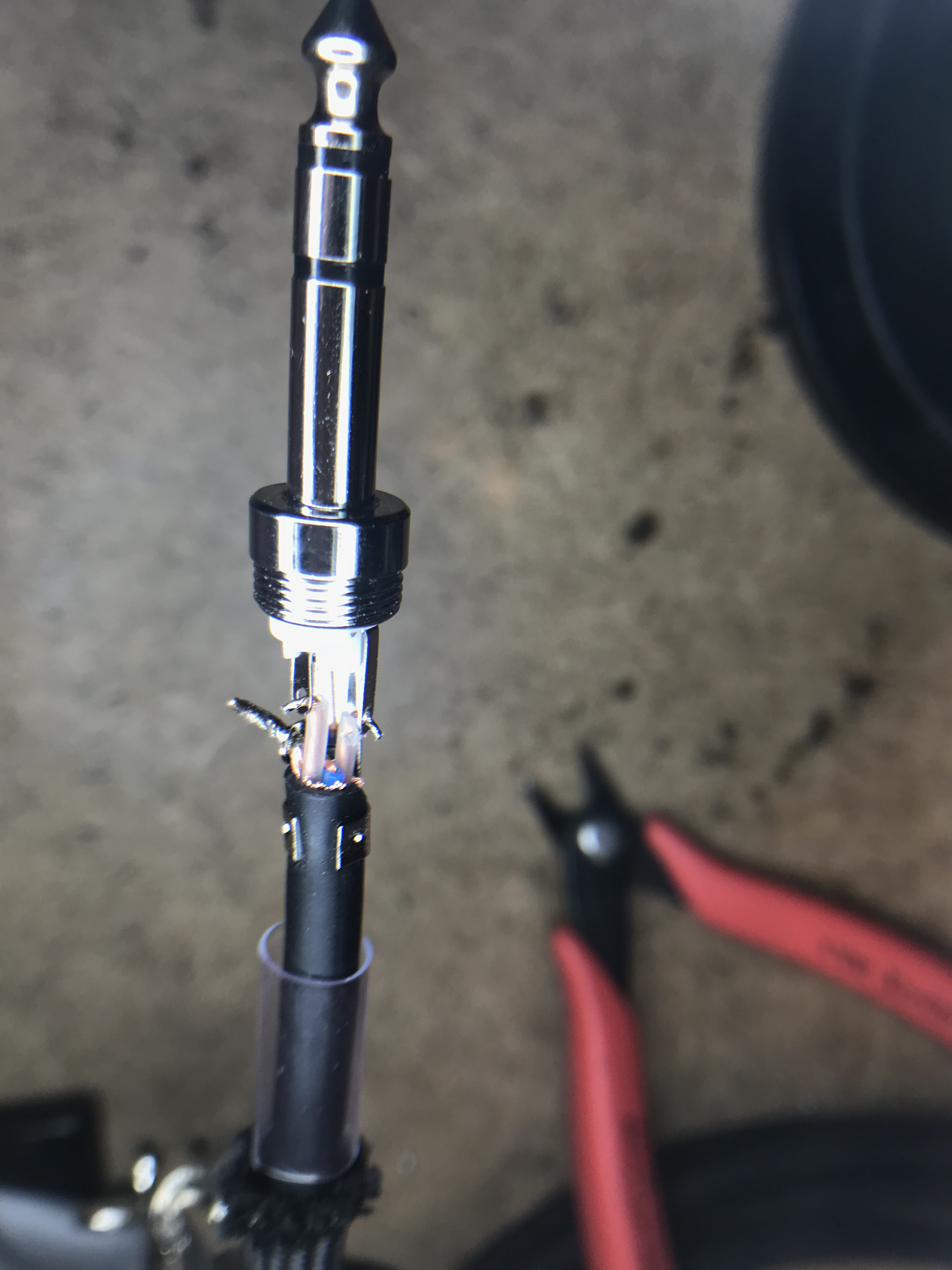
Solder and then trim the ends.
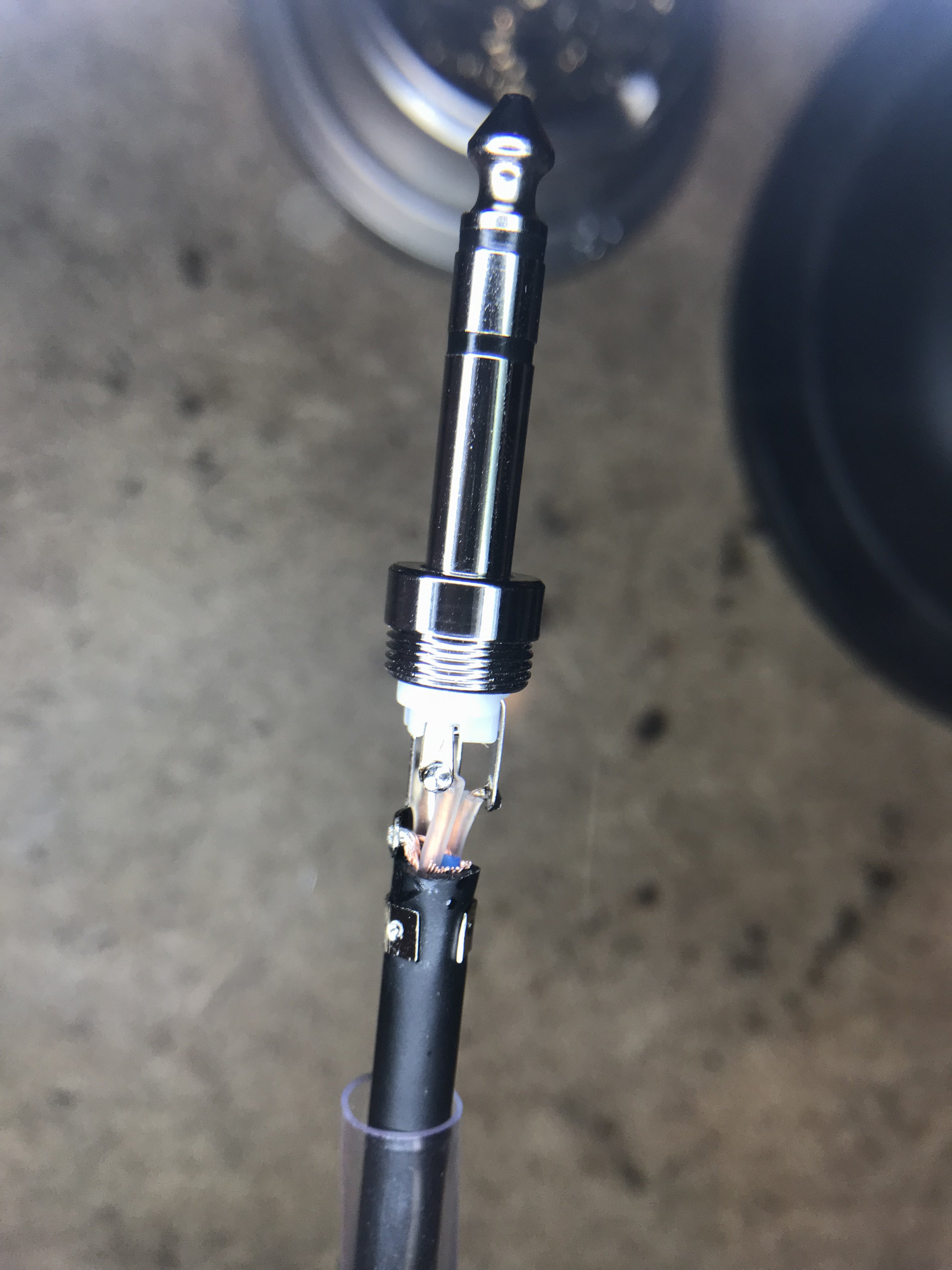
Pull up the clear insulator, pull up the techflex and heat up the first layer of heatshrink to hold it together.
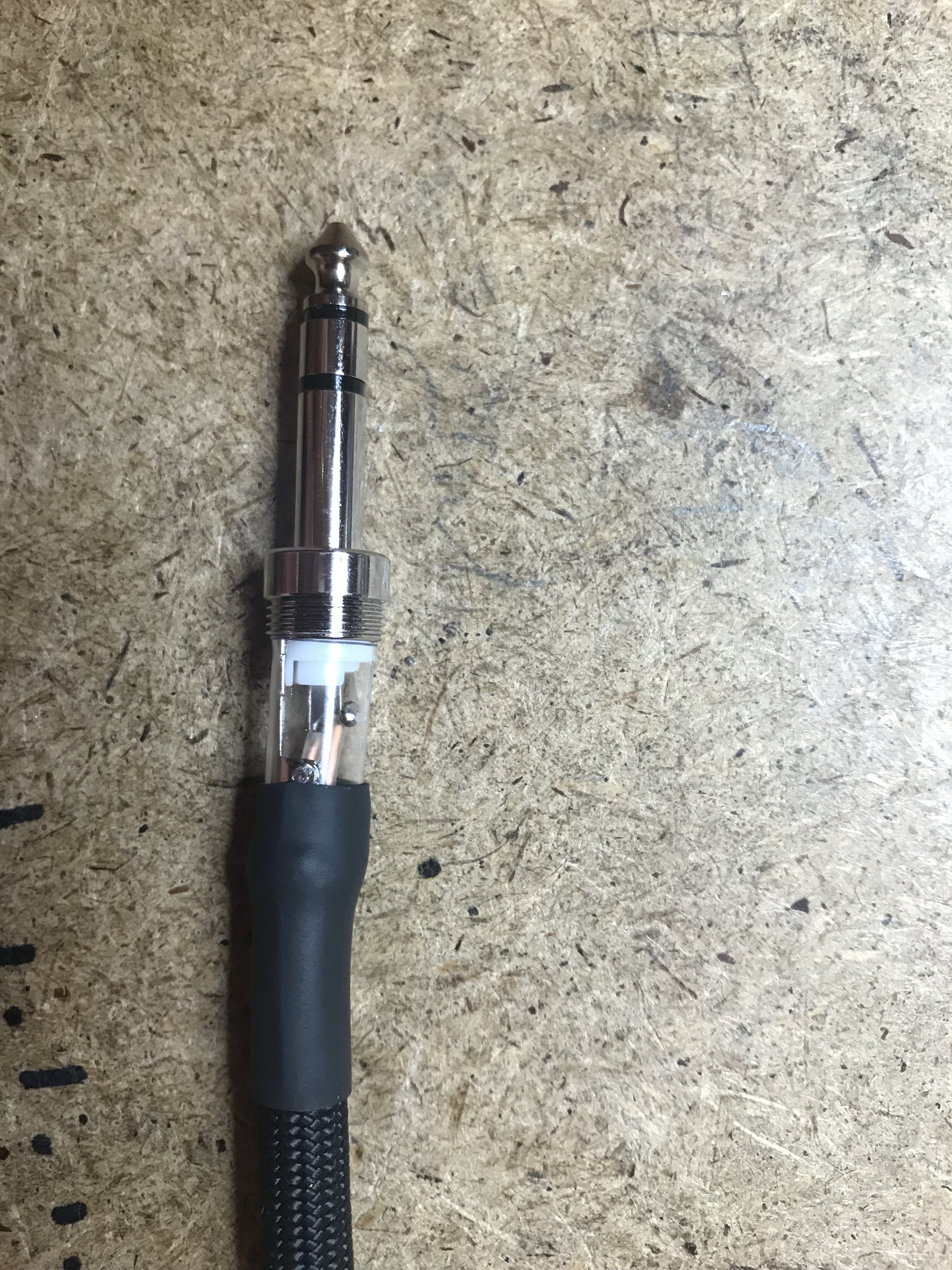
2nd layer of heatshrink and backshell.
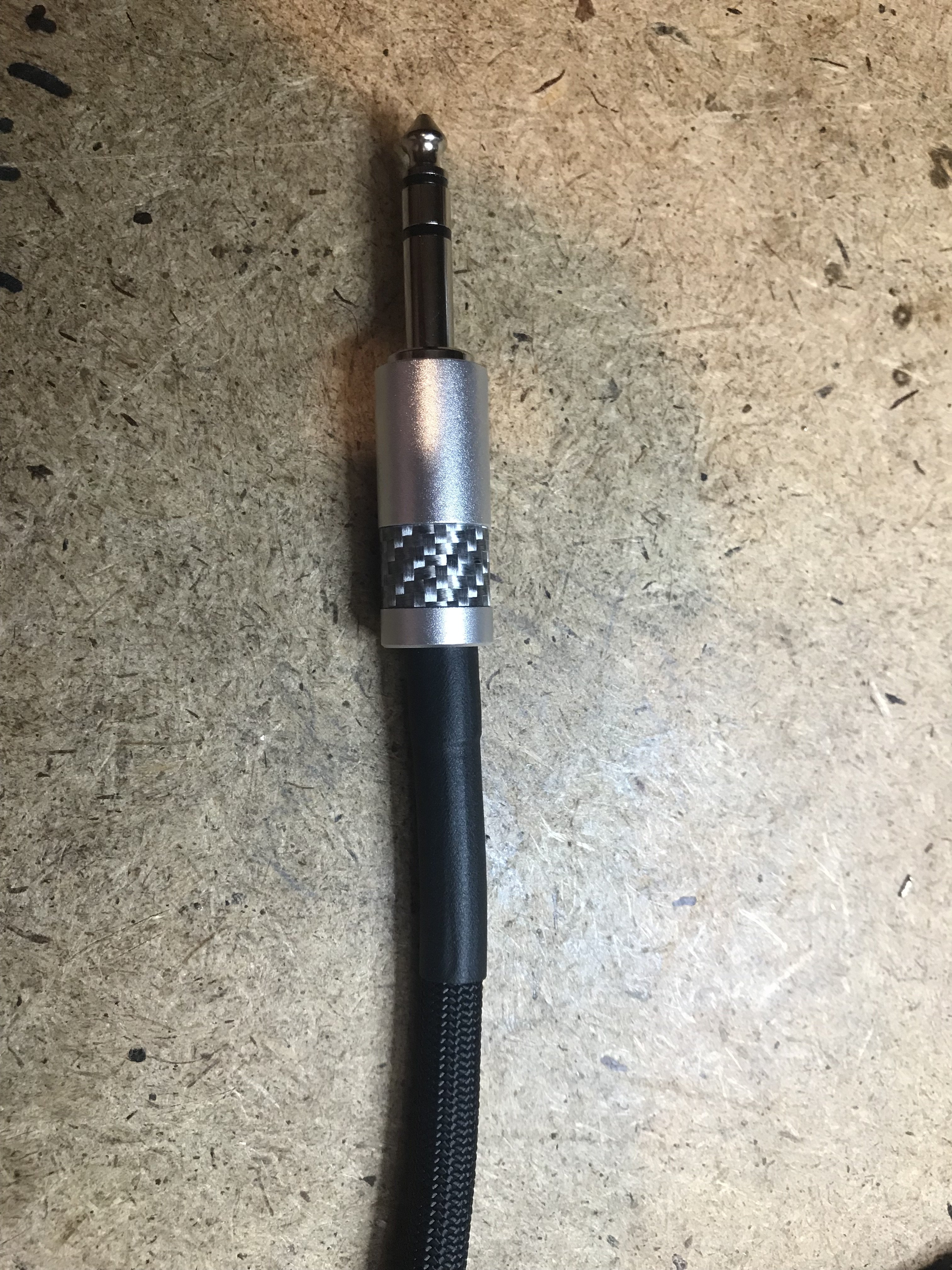
At the Y.
One layer of heat shrink to hold the techflex in place and then I worked the Y thing up and over it all. It fits tight but don't go yanking on this!!
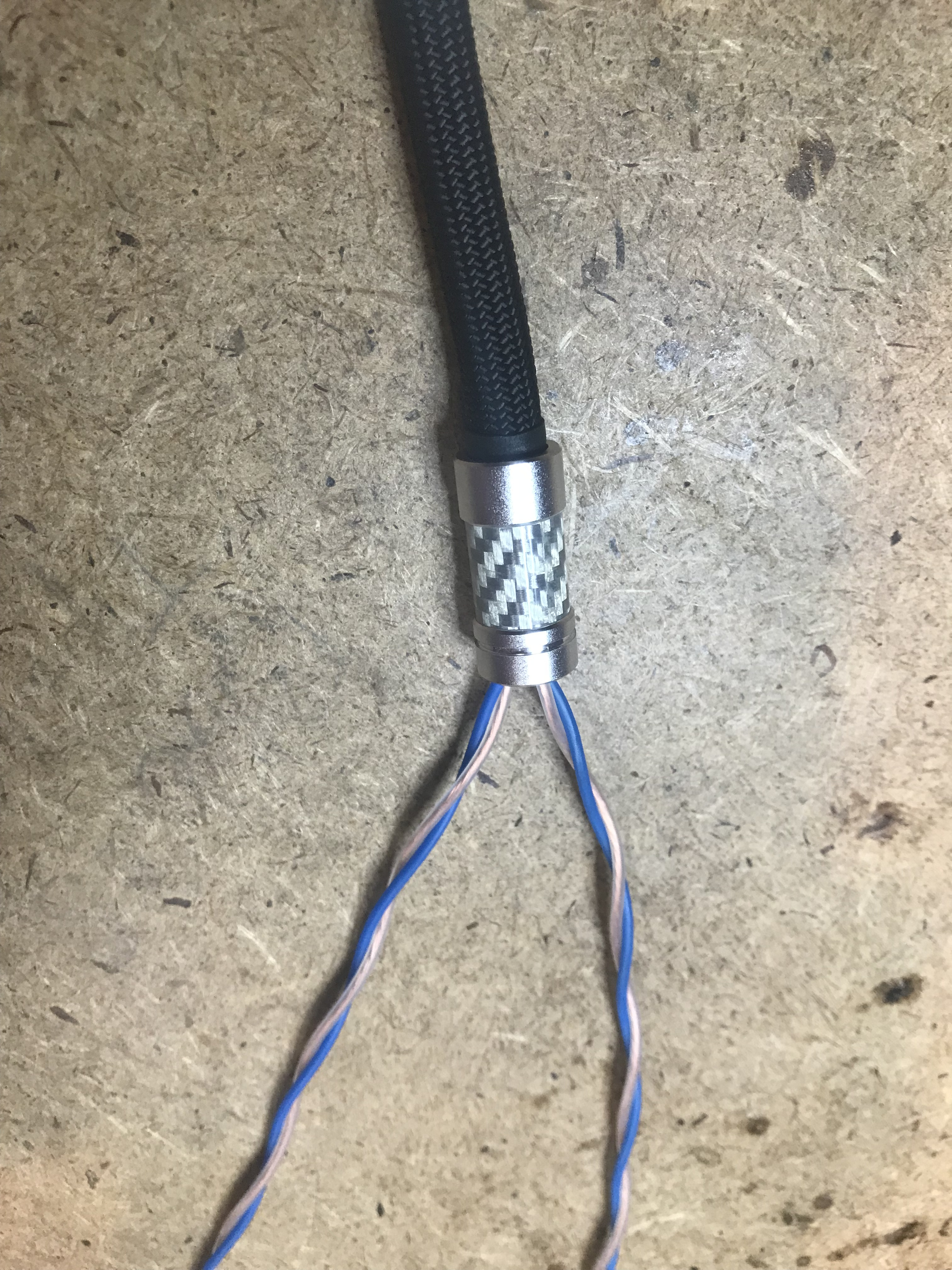
On to the hard end... Da parts:
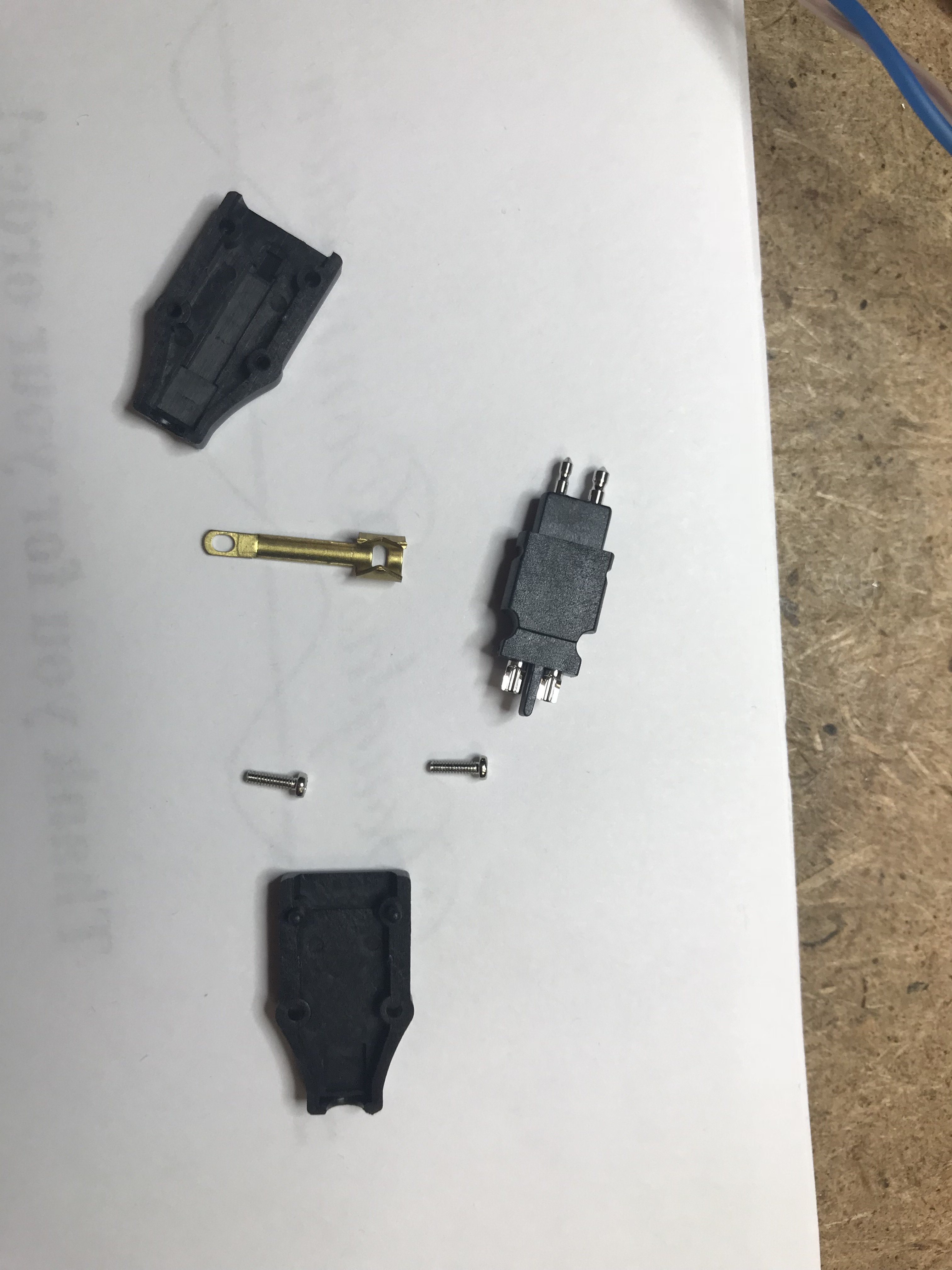
I followed roughly the same procedure - tin and fit. In this case I put some heatshrink on now so I can use the restraint clamp. You'll need to use an ohm meter to get your ends right. Tip is Left, Ring is Right. Small pin is signal (from tip or ring), large pin is ground.
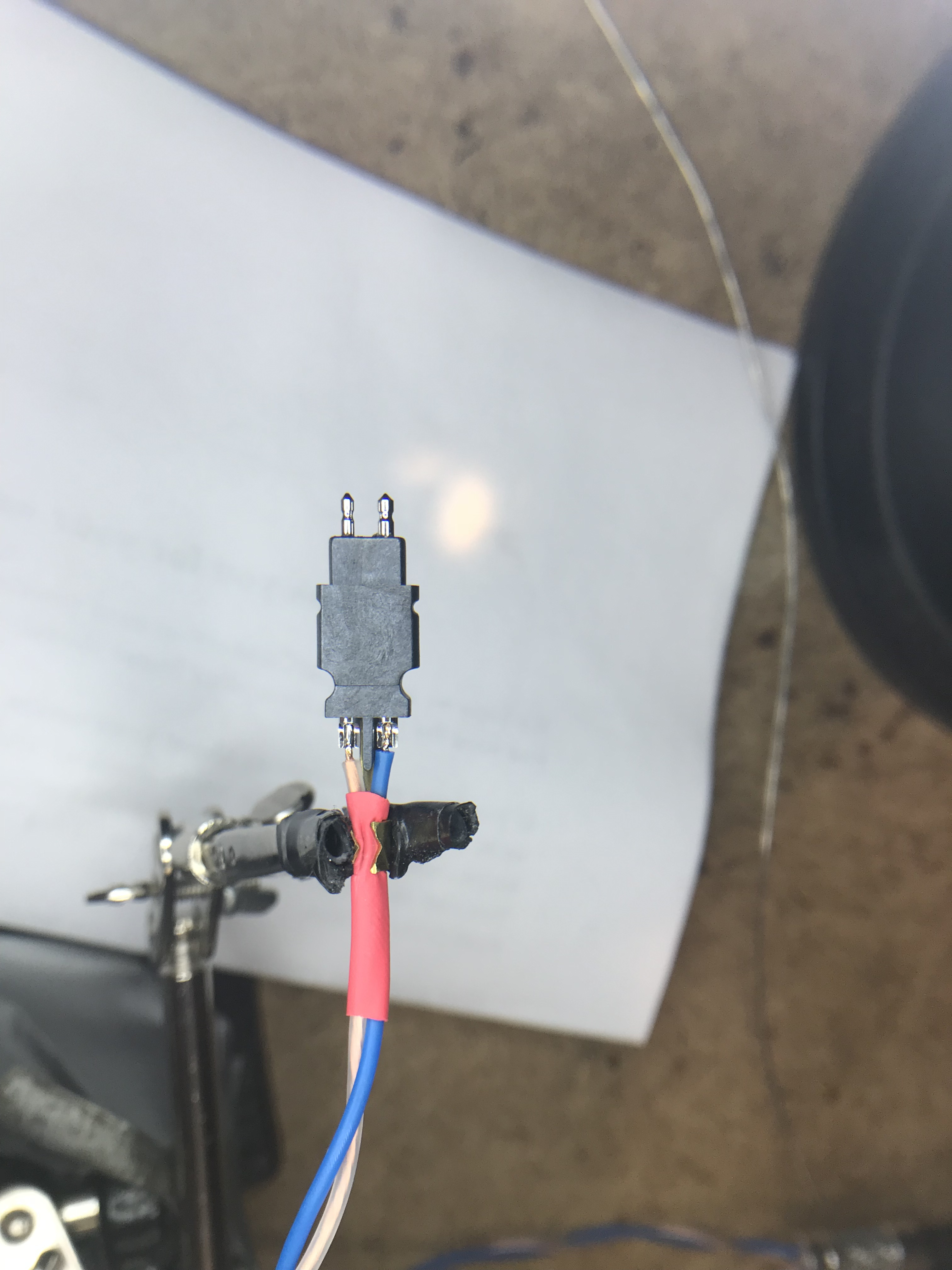
Soldered.

Finished.
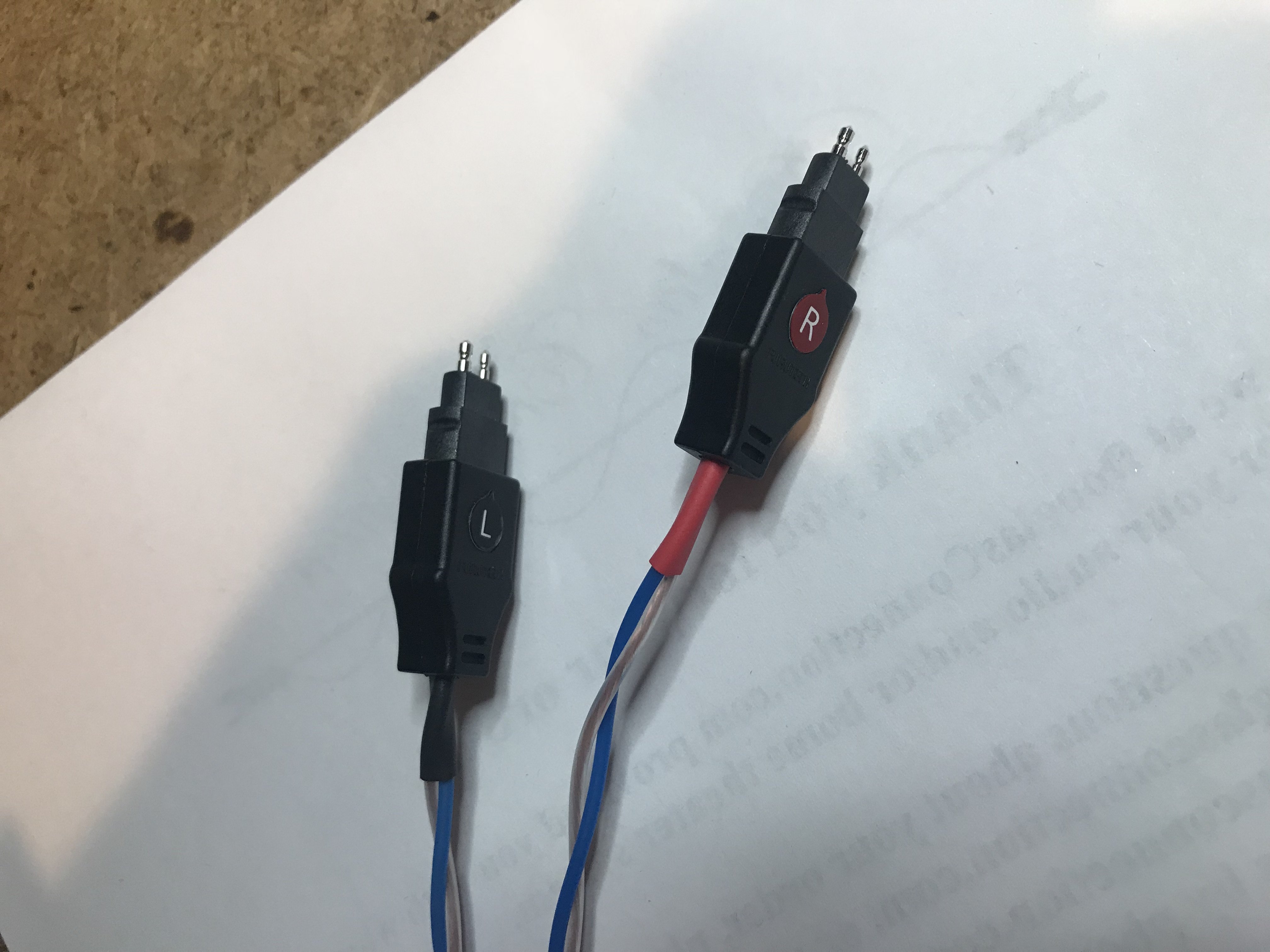
The works.
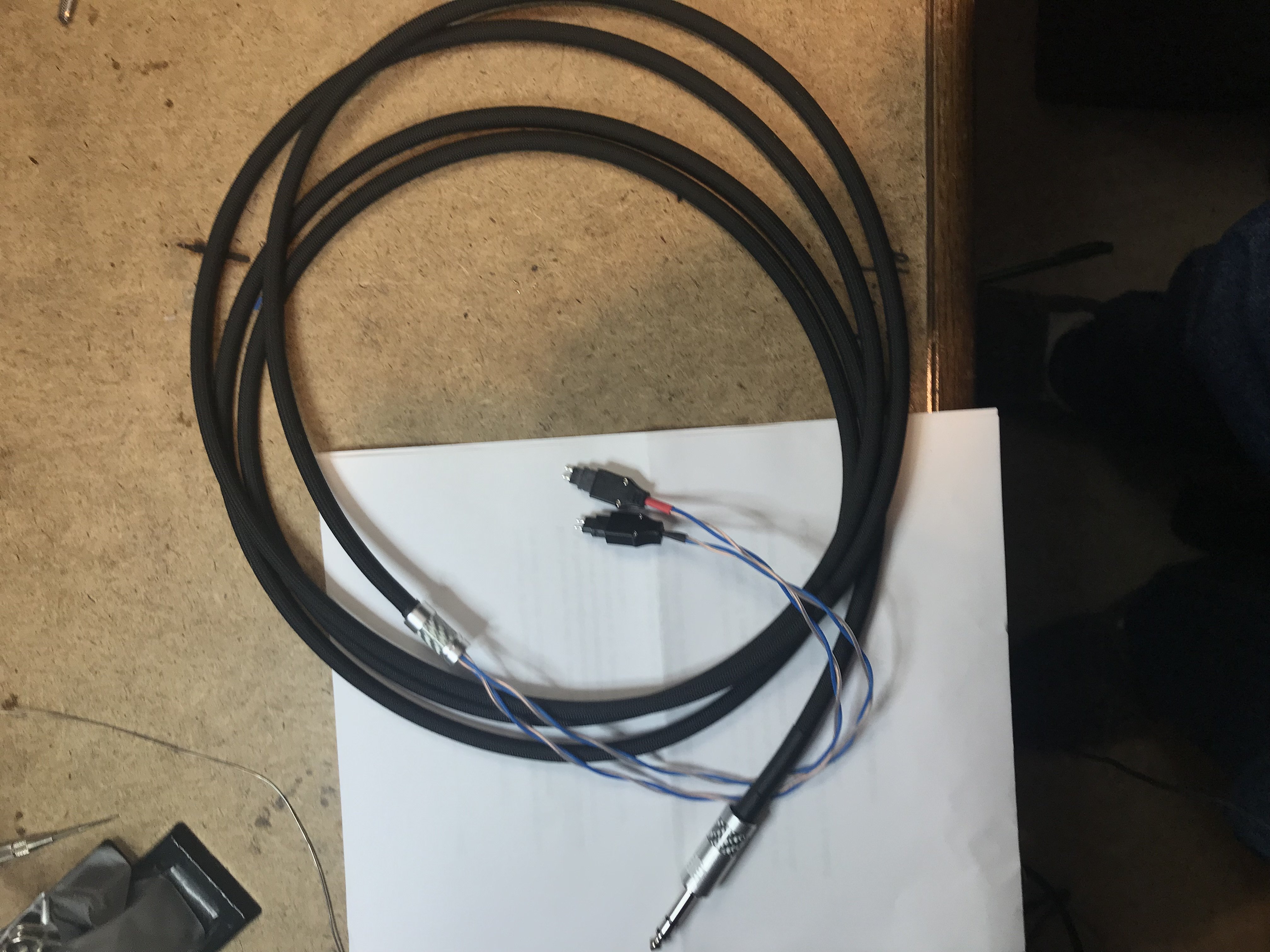
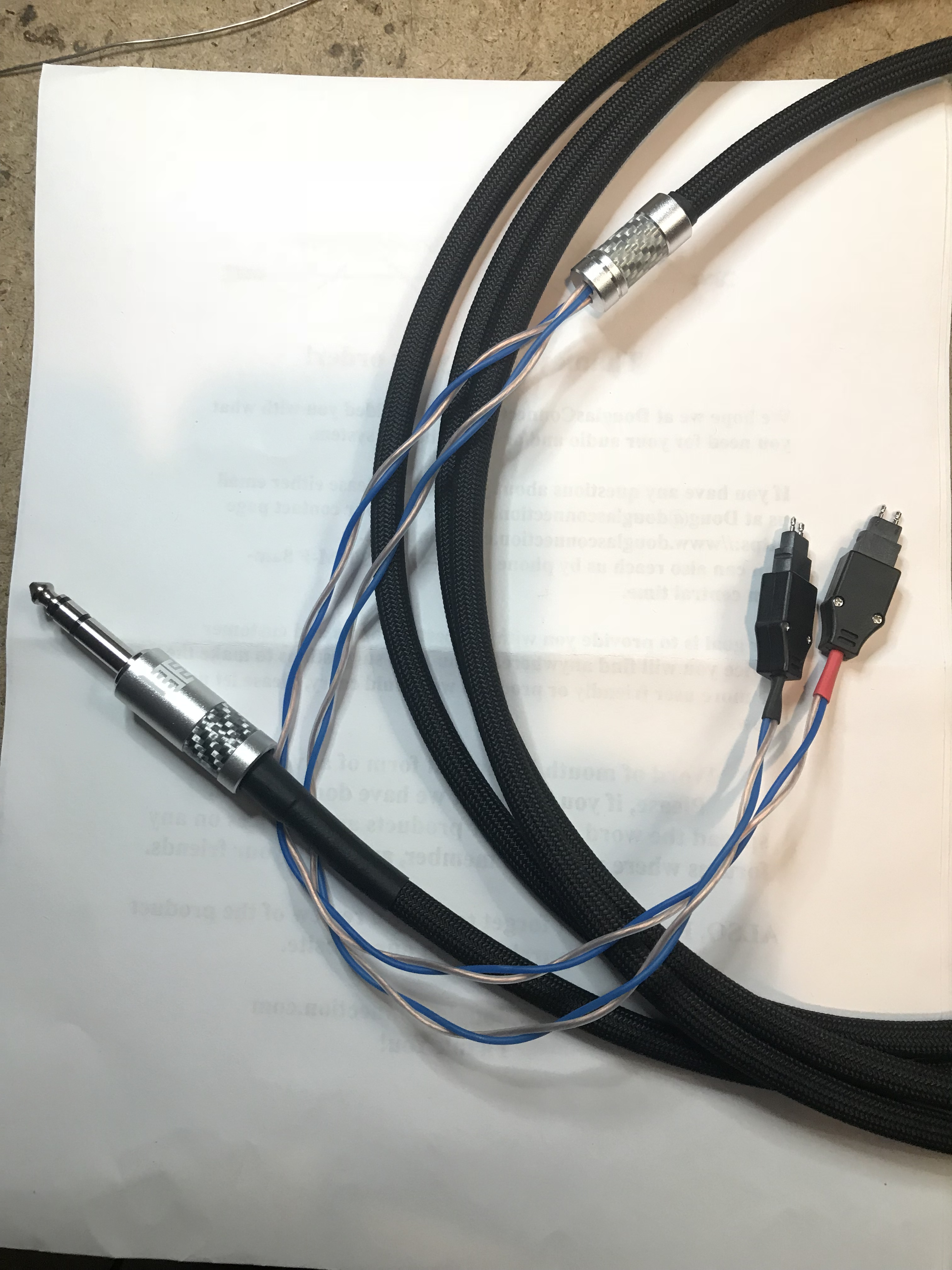
And the darn things work!
As a "service" I'll need to test these for at least 30 days and then the obligatory 90 day breakin period.
The Recipe:
Mogami W2534 cable - 11 feet
Soft techflex - about 10 feet
1/4" plug from Eidolic
Y thingy from Eidolic
Furutech FT-2PS headphone connector
various heatshrinks
The cotton stuff was not used, it just don't fit...
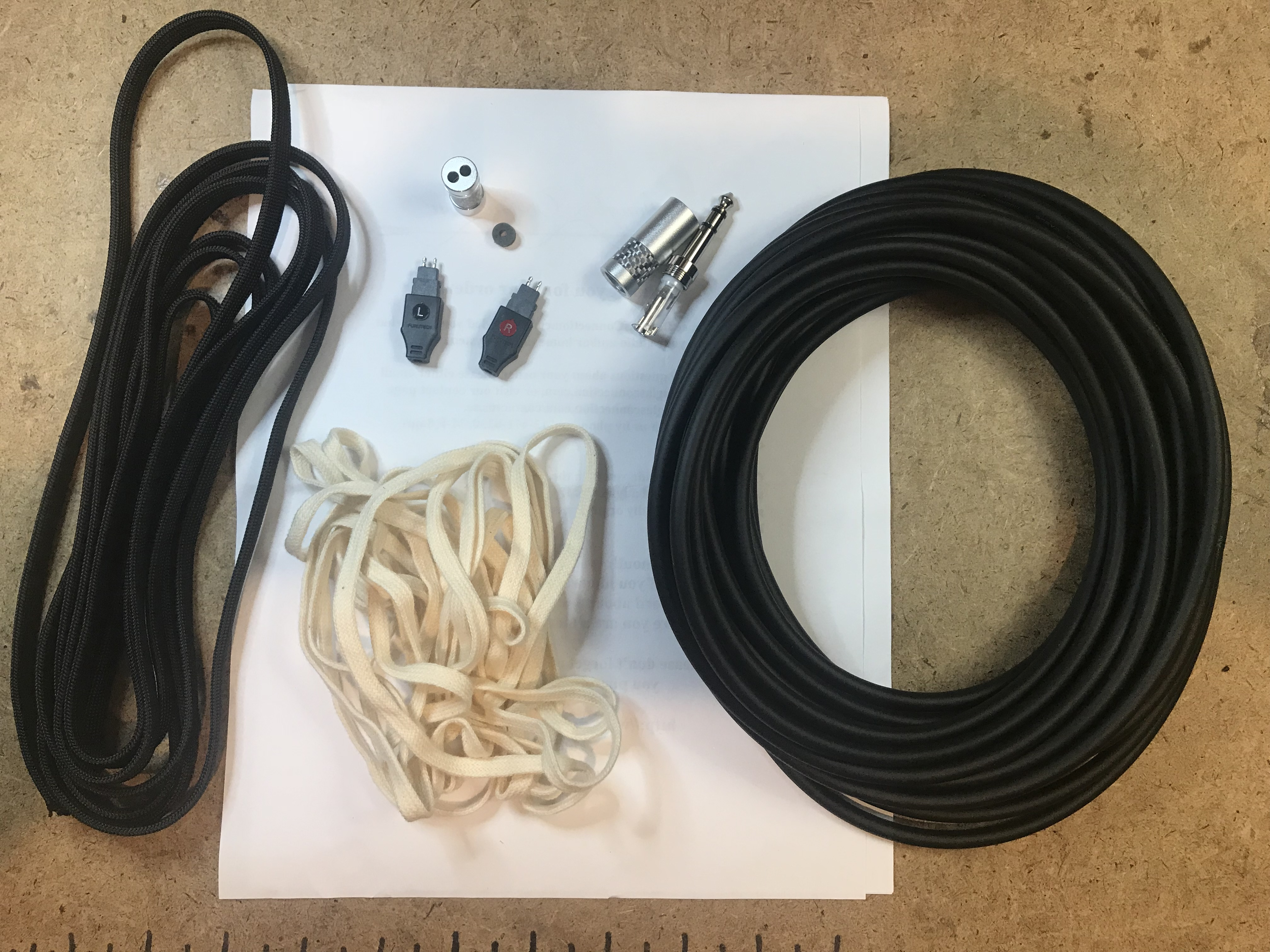
Tools:
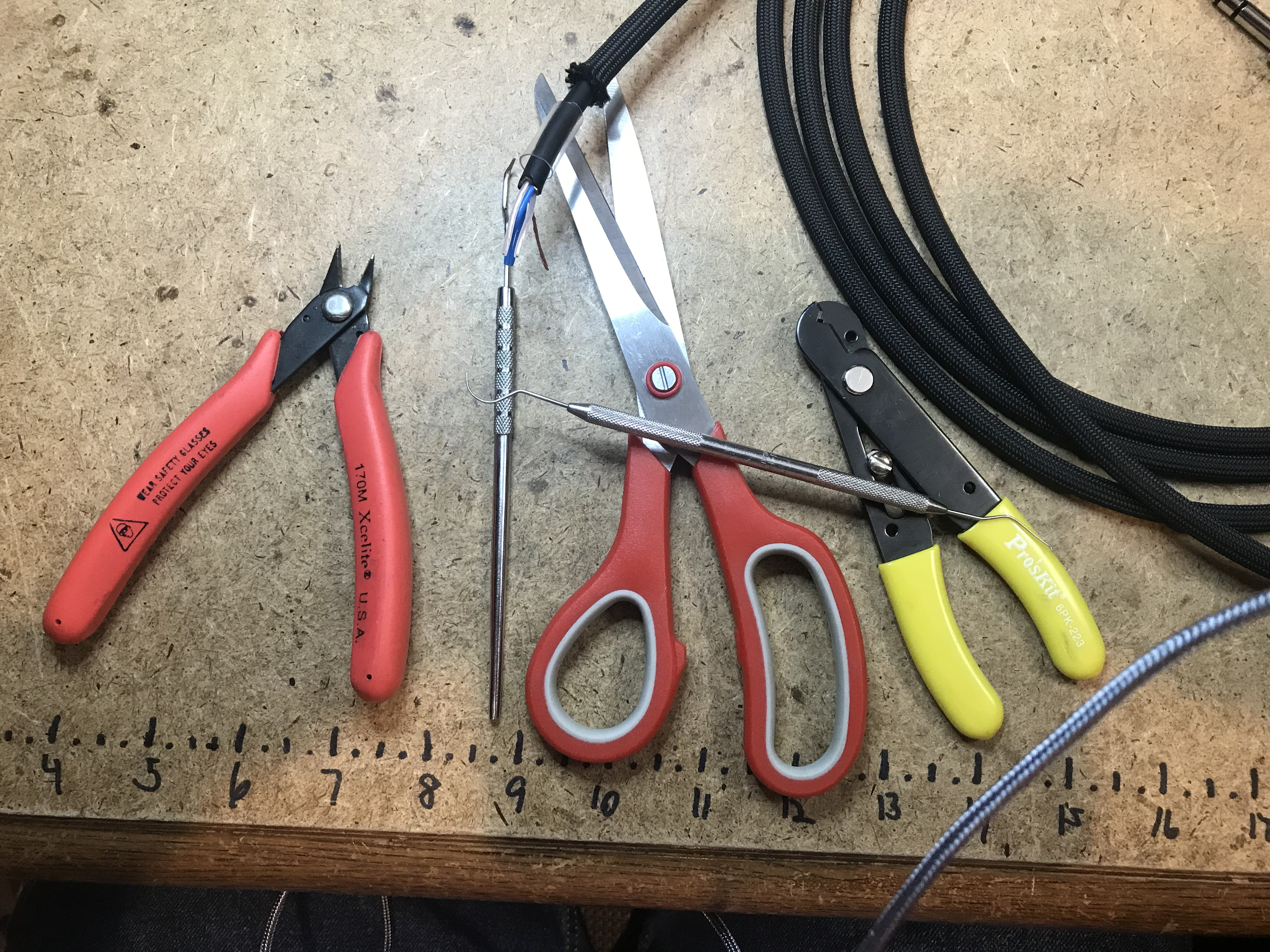
As mentioned in another thread the techflex is the softer cloth type but it doesn't "shrink" as you push it onto the cable so it does take some time and patience to get it threaded on. I pulled it through the entire cable, then sat and thought about it.
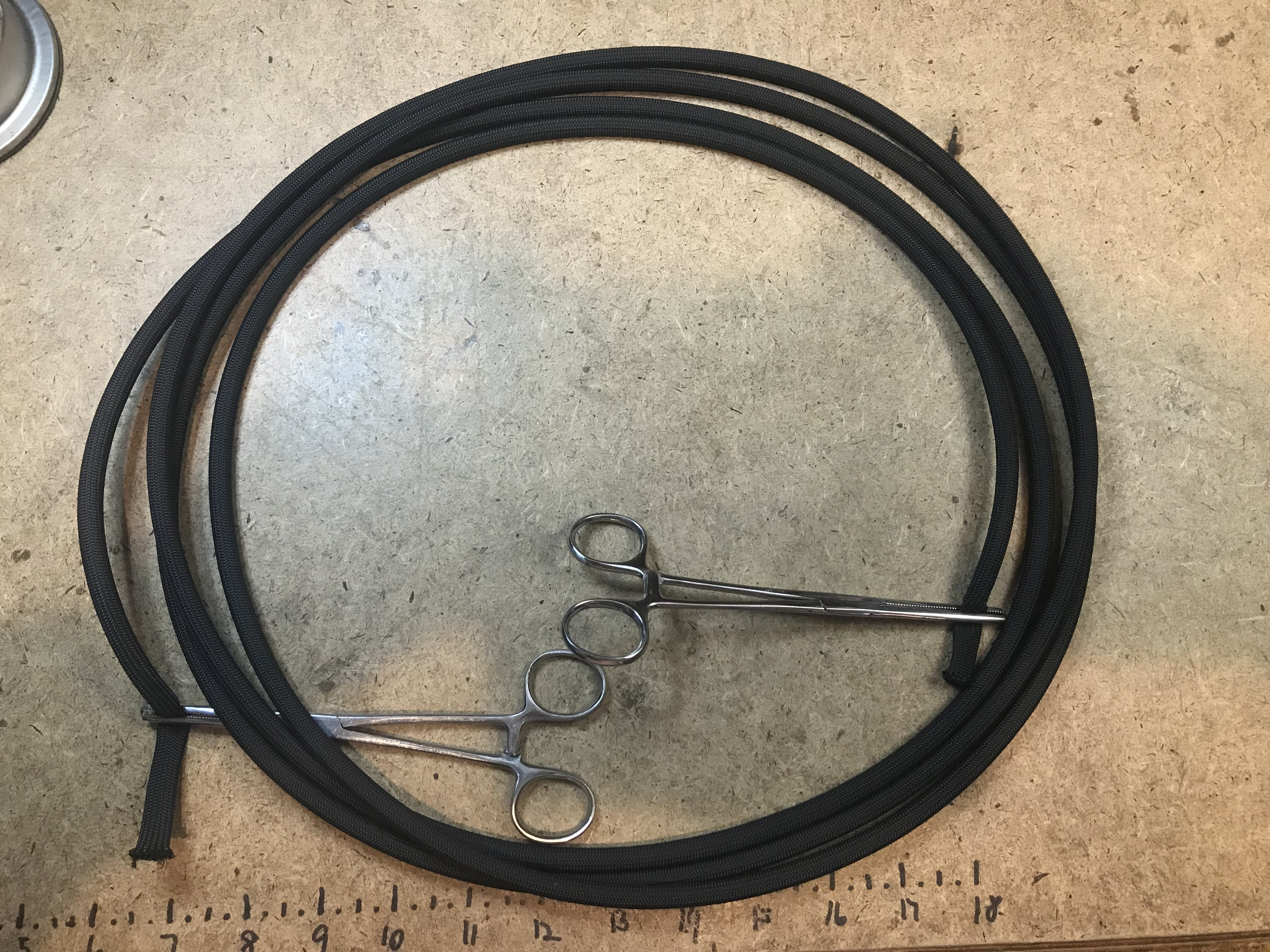
I measured the distance I needed the Y (about 14") + the amount I needed to clear on the 1/4 plug end (about 1 1/2) and pulled that amount back off and cut it. You'll need a good scissors. Then I pulled it back on to where I wanted it and left it alone.
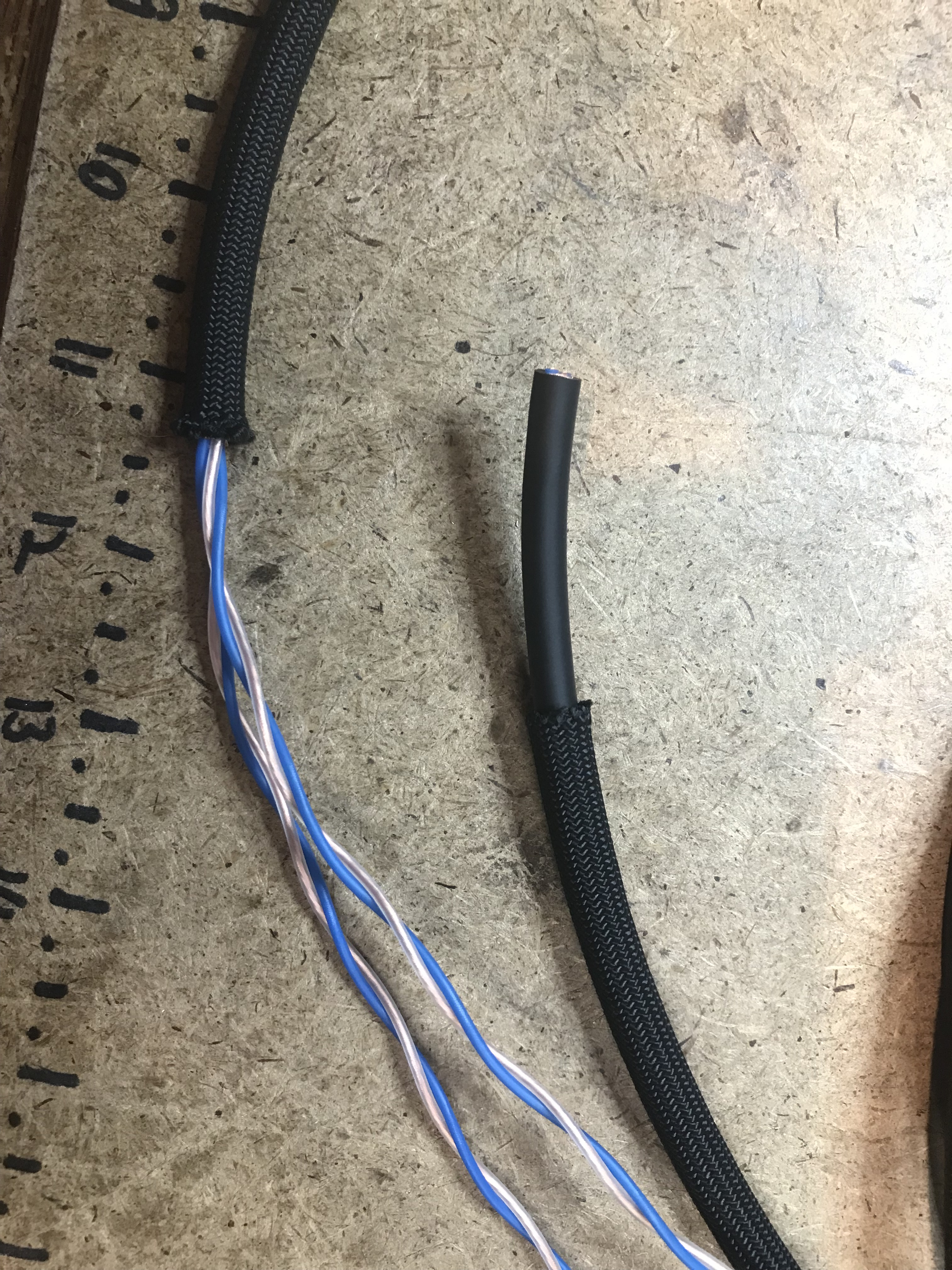
I stripped the Y end first and removed the shield but then moved to the easy end.
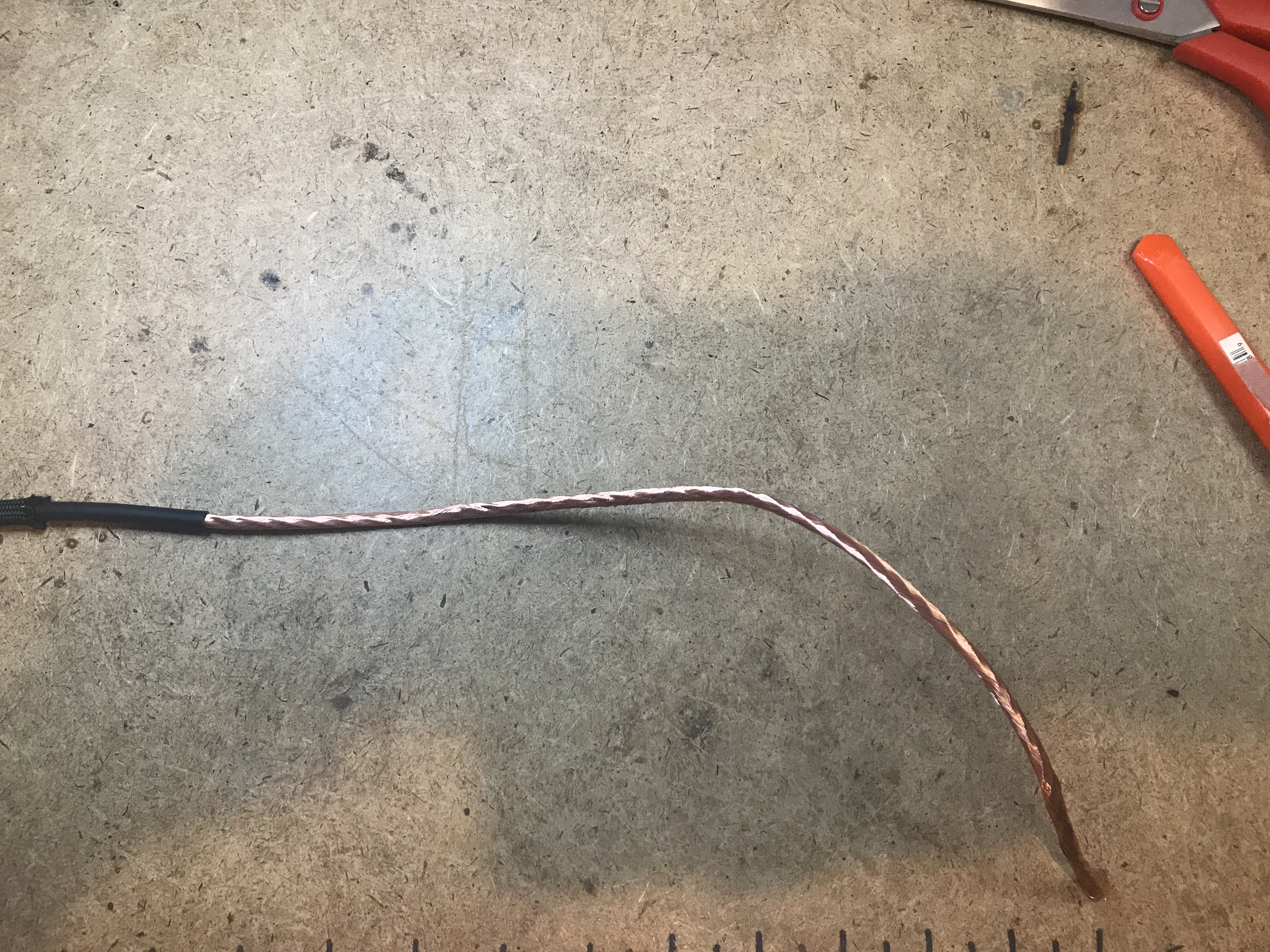
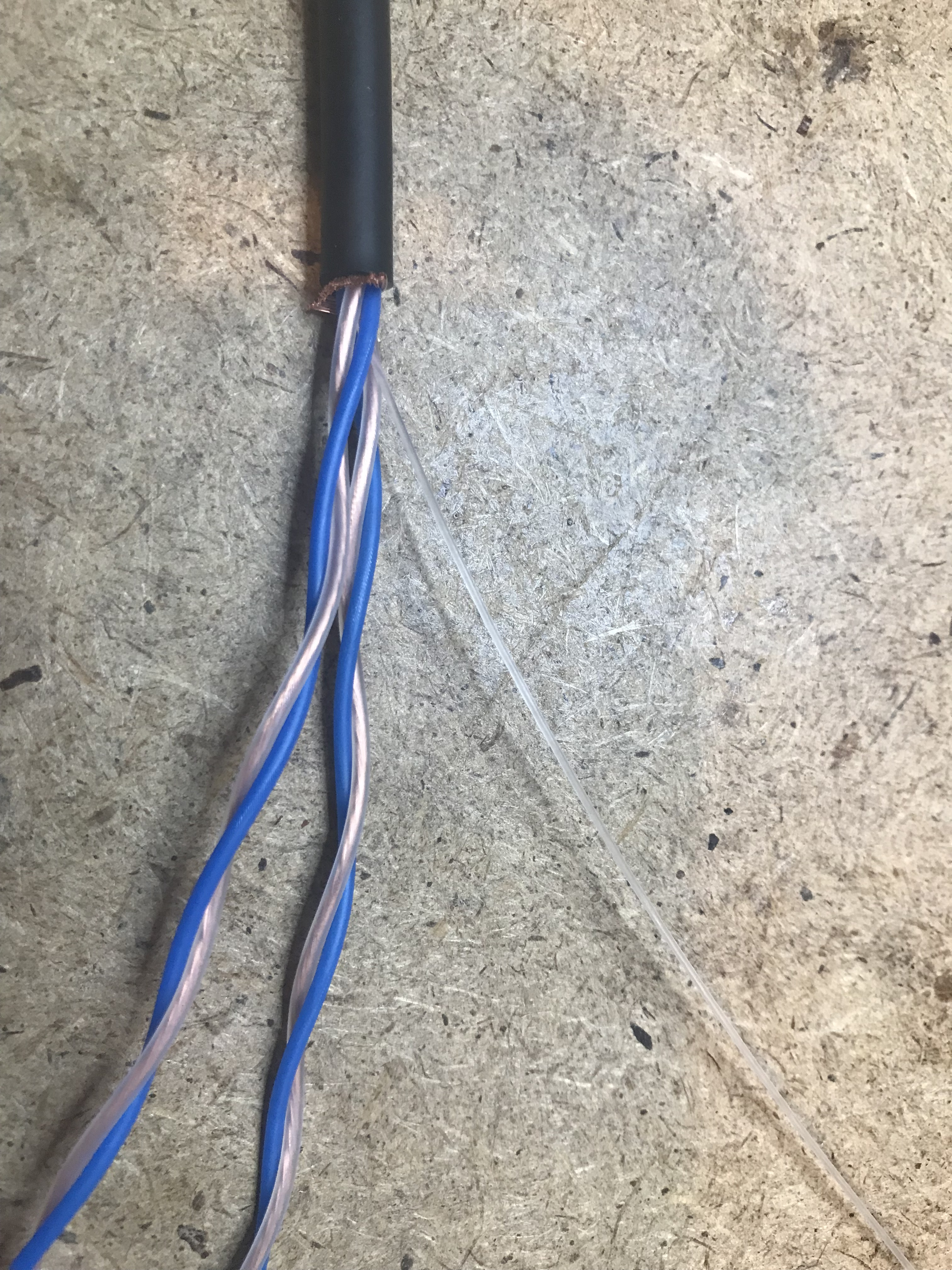
The Eidolic is a fairly easy connector to work with. I opened up the ground pole hole with a small file I use just for that purpose and got the tinned grounds through it with no issues.
Don't forget to thread on your backshell, heat shrink and the clear plastic insulator before soldering.
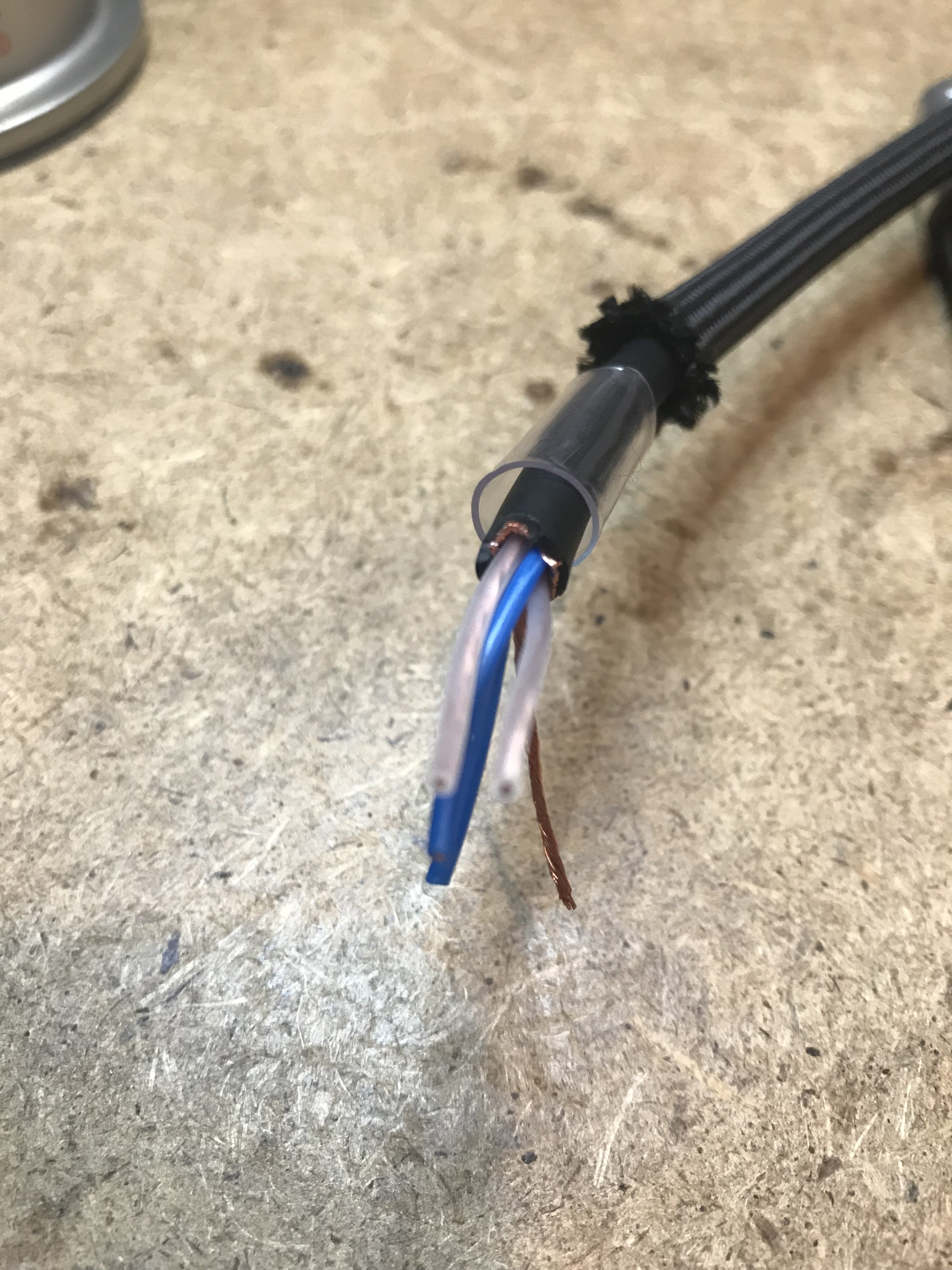
Tin the ends (solder together the naked copper wires). This will keep stray strands from escaping and shorting stuff out later. It also makes it much easier to solder this together.
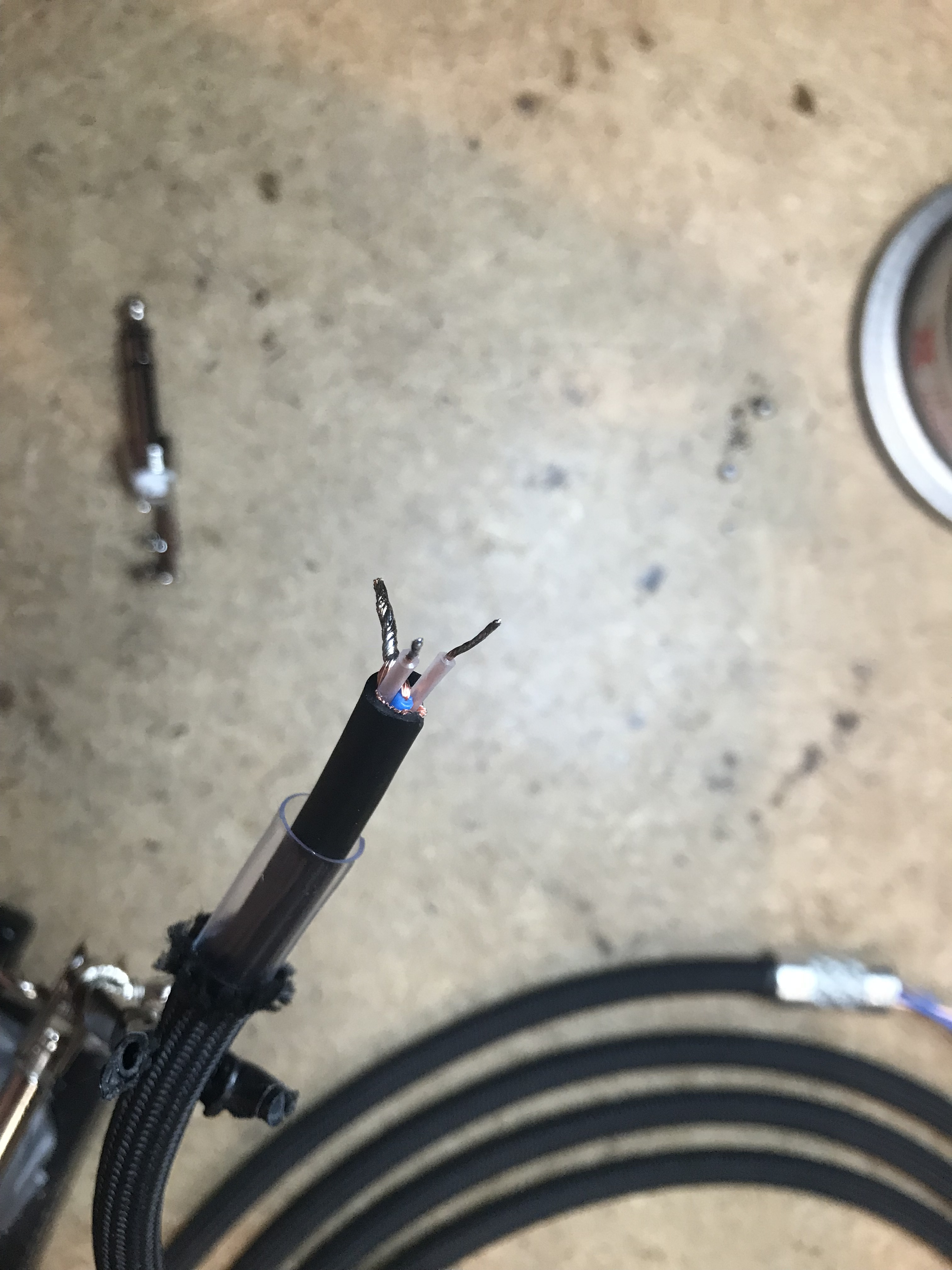
I put it all together before soldering. I do use a bit of shield combined with the grounds.
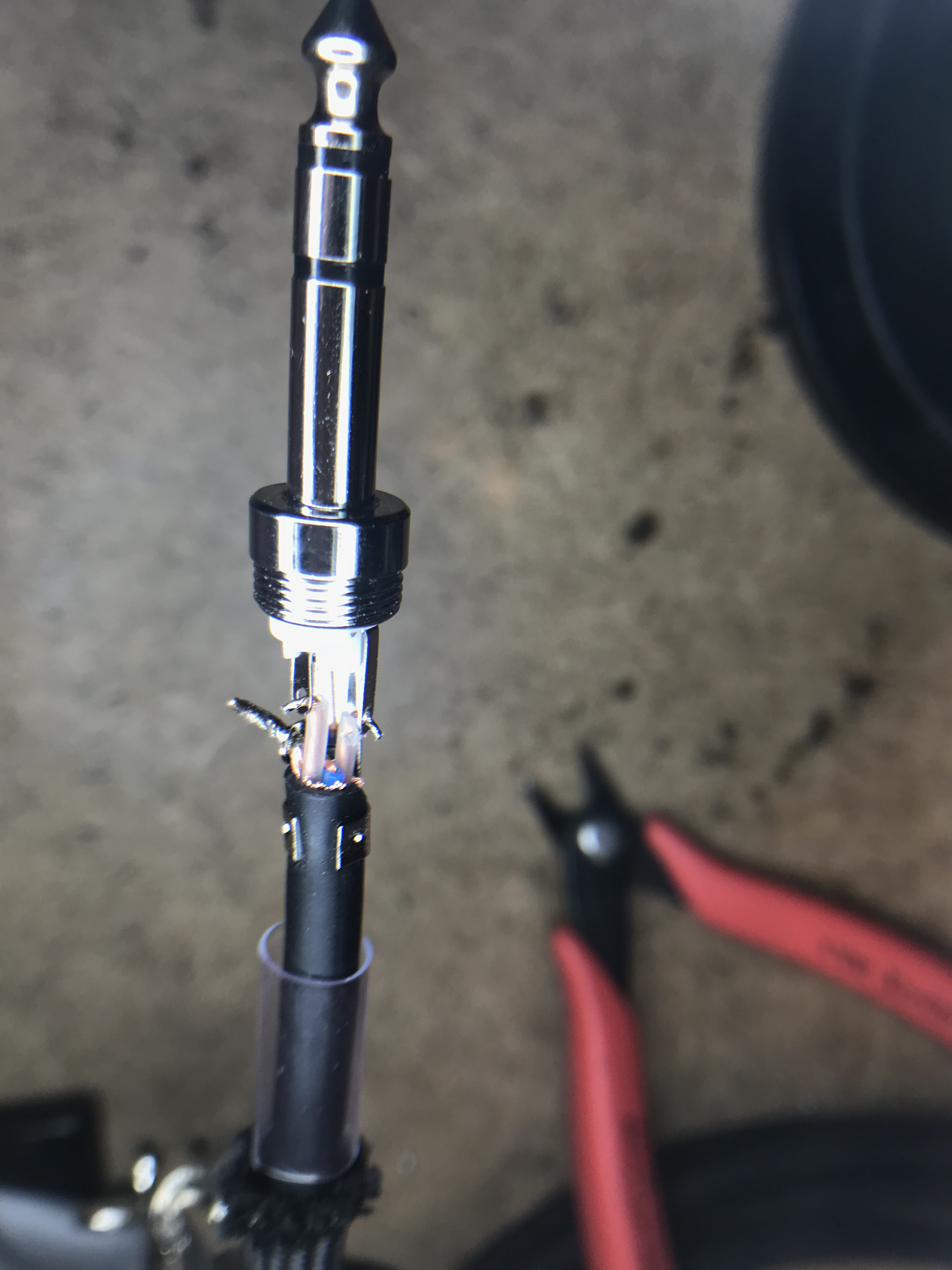
Solder and then trim the ends.
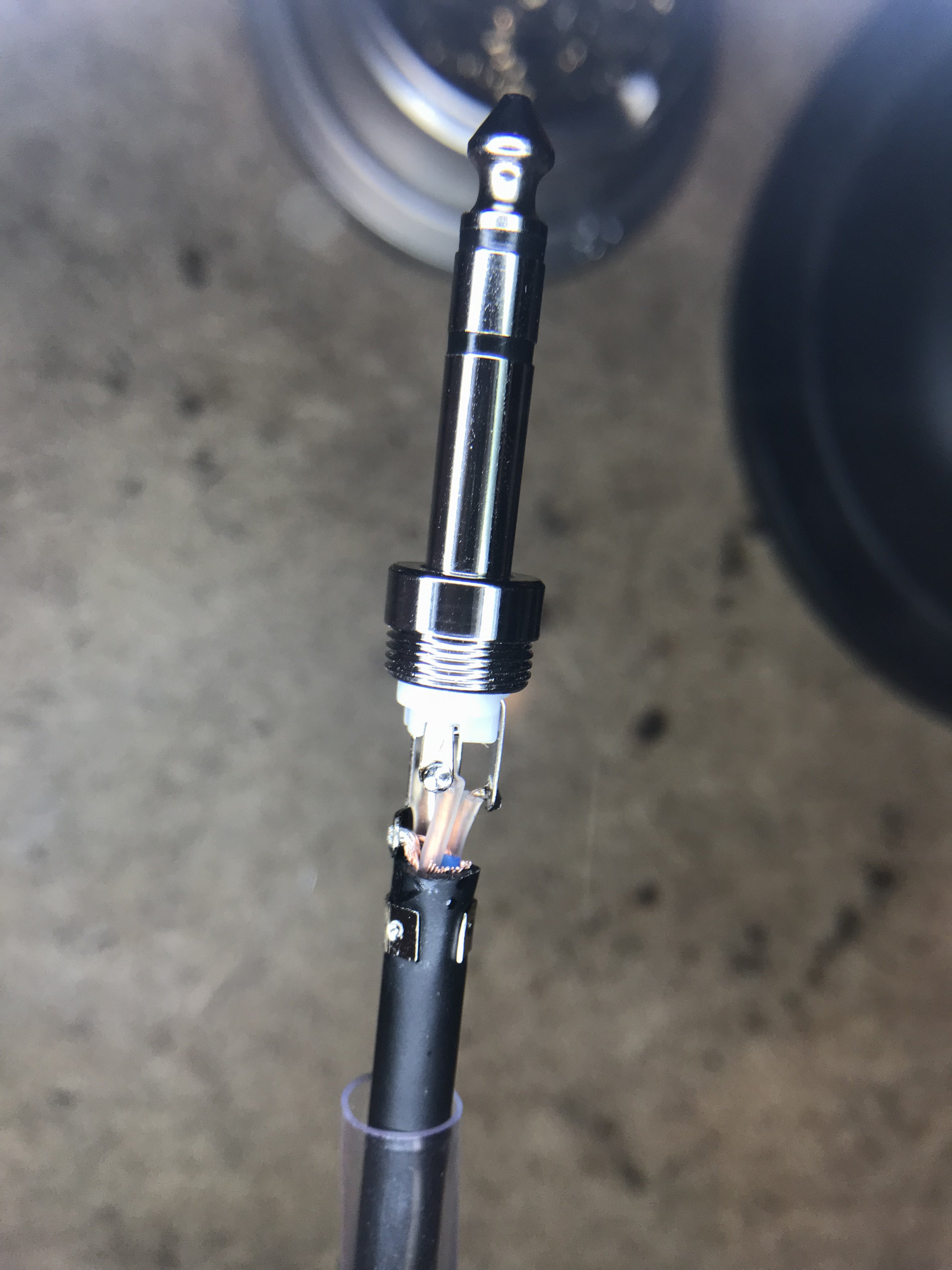
Pull up the clear insulator, pull up the techflex and heat up the first layer of heatshrink to hold it together.
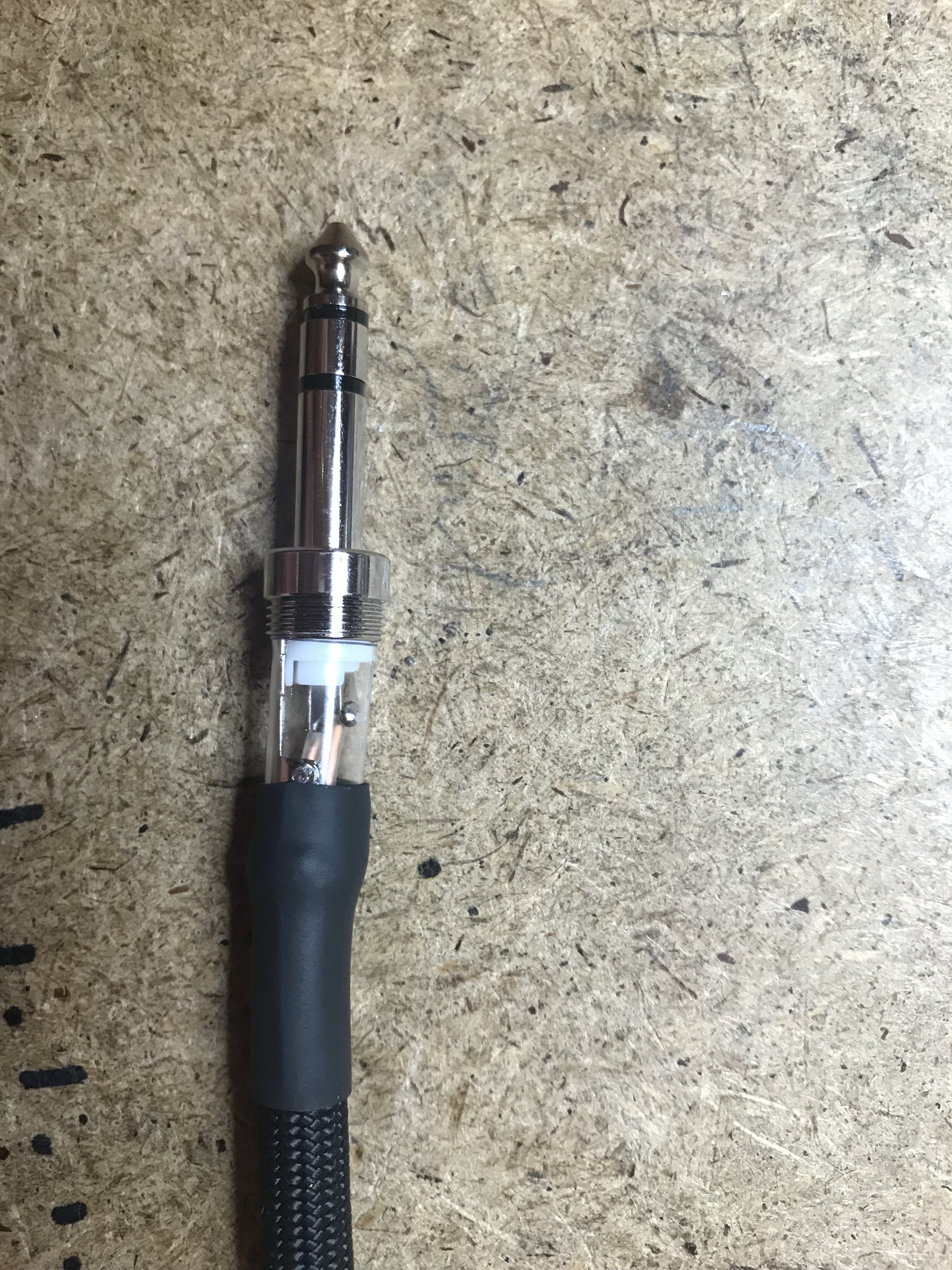
2nd layer of heatshrink and backshell.
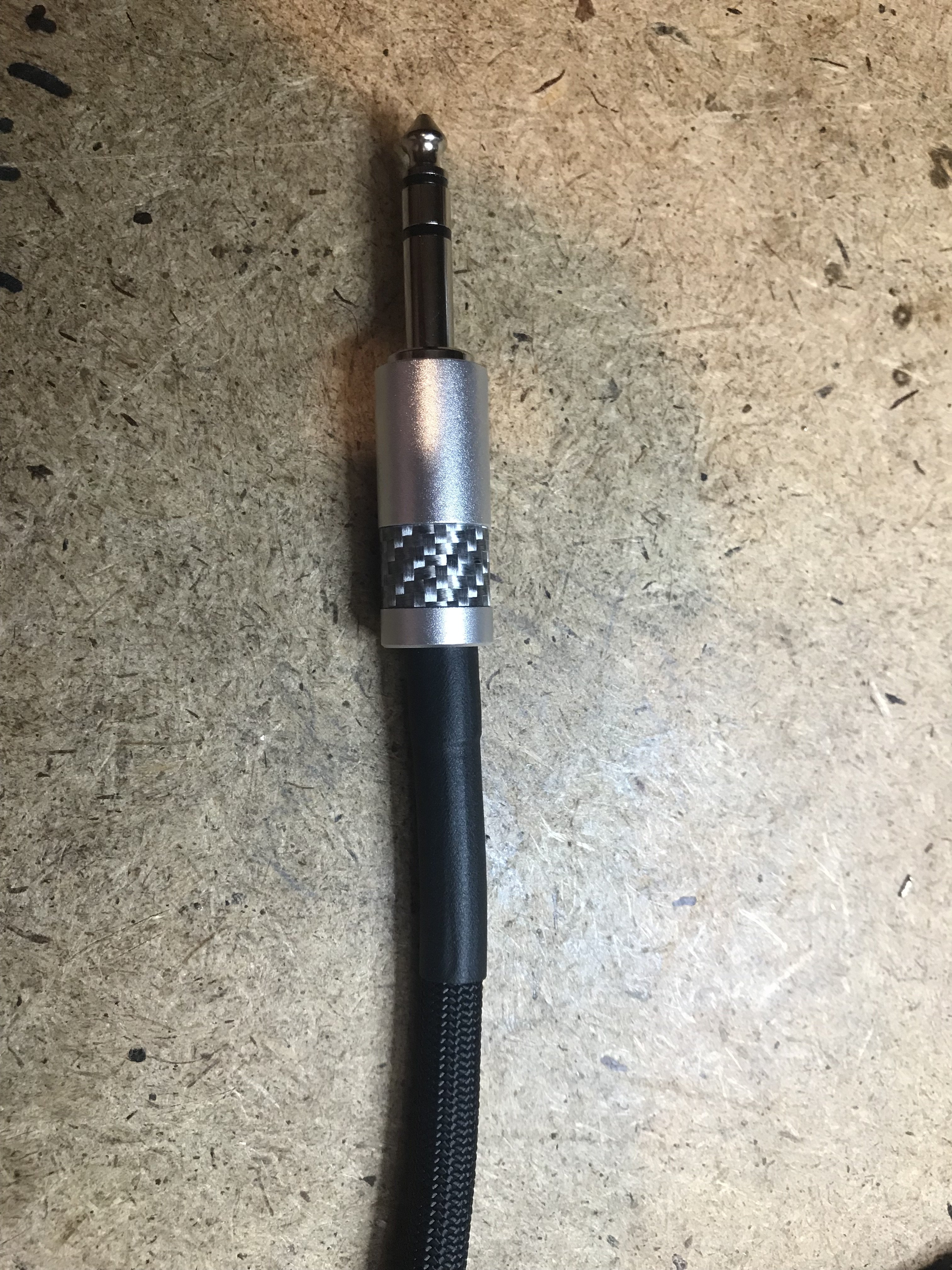
At the Y.
One layer of heat shrink to hold the techflex in place and then I worked the Y thing up and over it all. It fits tight but don't go yanking on this!!
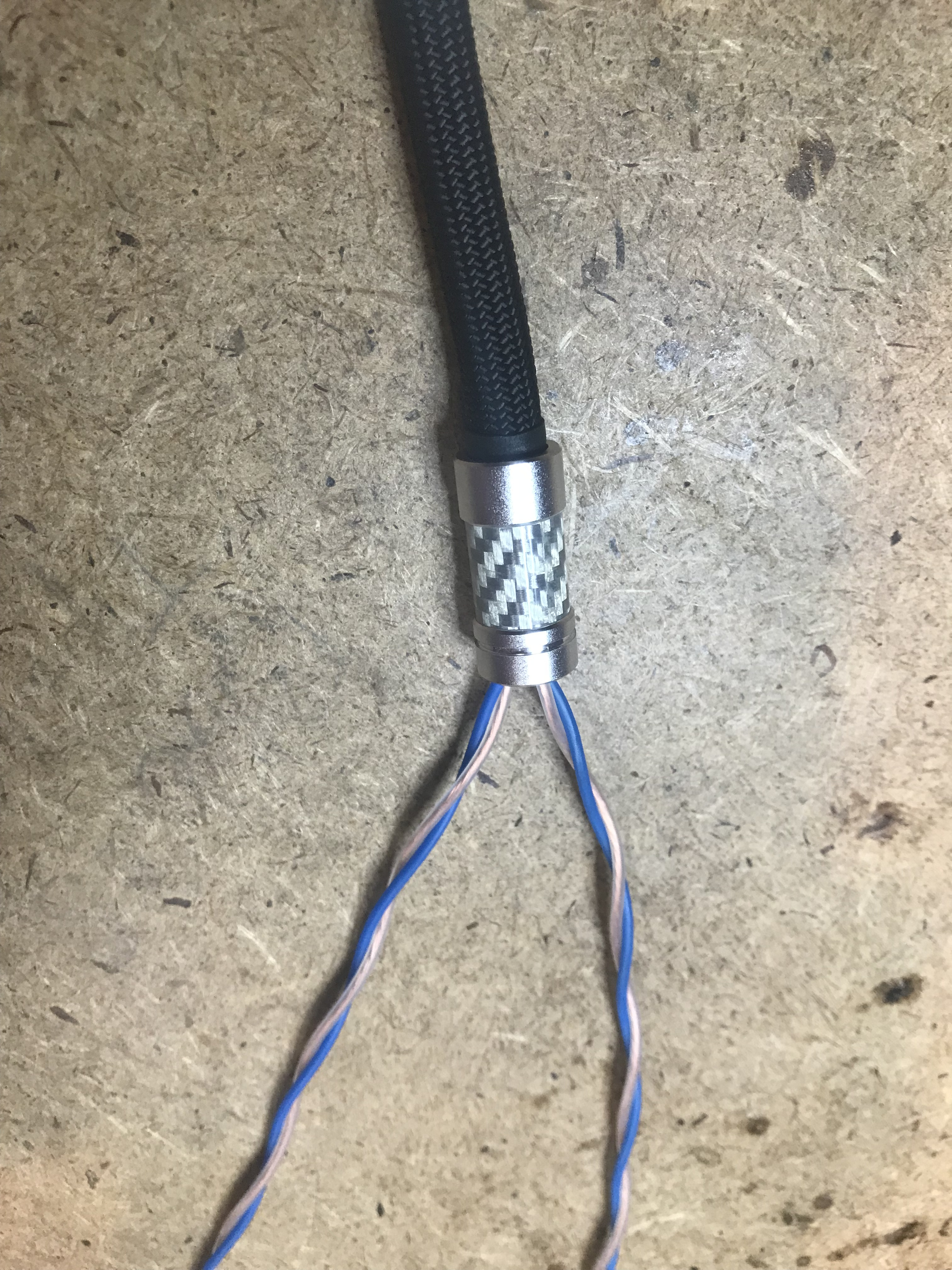
On to the hard end... Da parts:
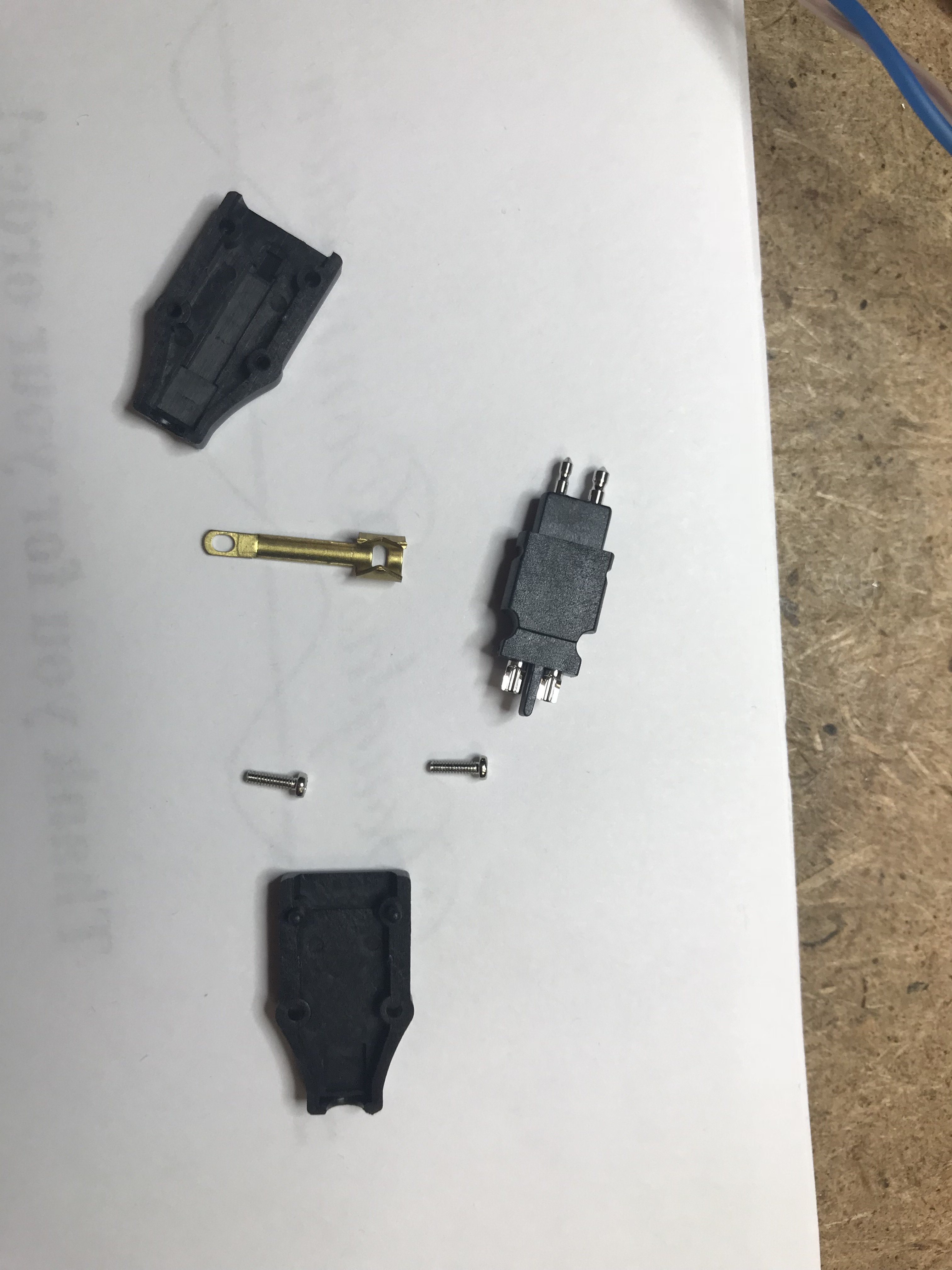
I followed roughly the same procedure - tin and fit. In this case I put some heatshrink on now so I can use the restraint clamp. You'll need to use an ohm meter to get your ends right. Tip is Left, Ring is Right. Small pin is signal (from tip or ring), large pin is ground.
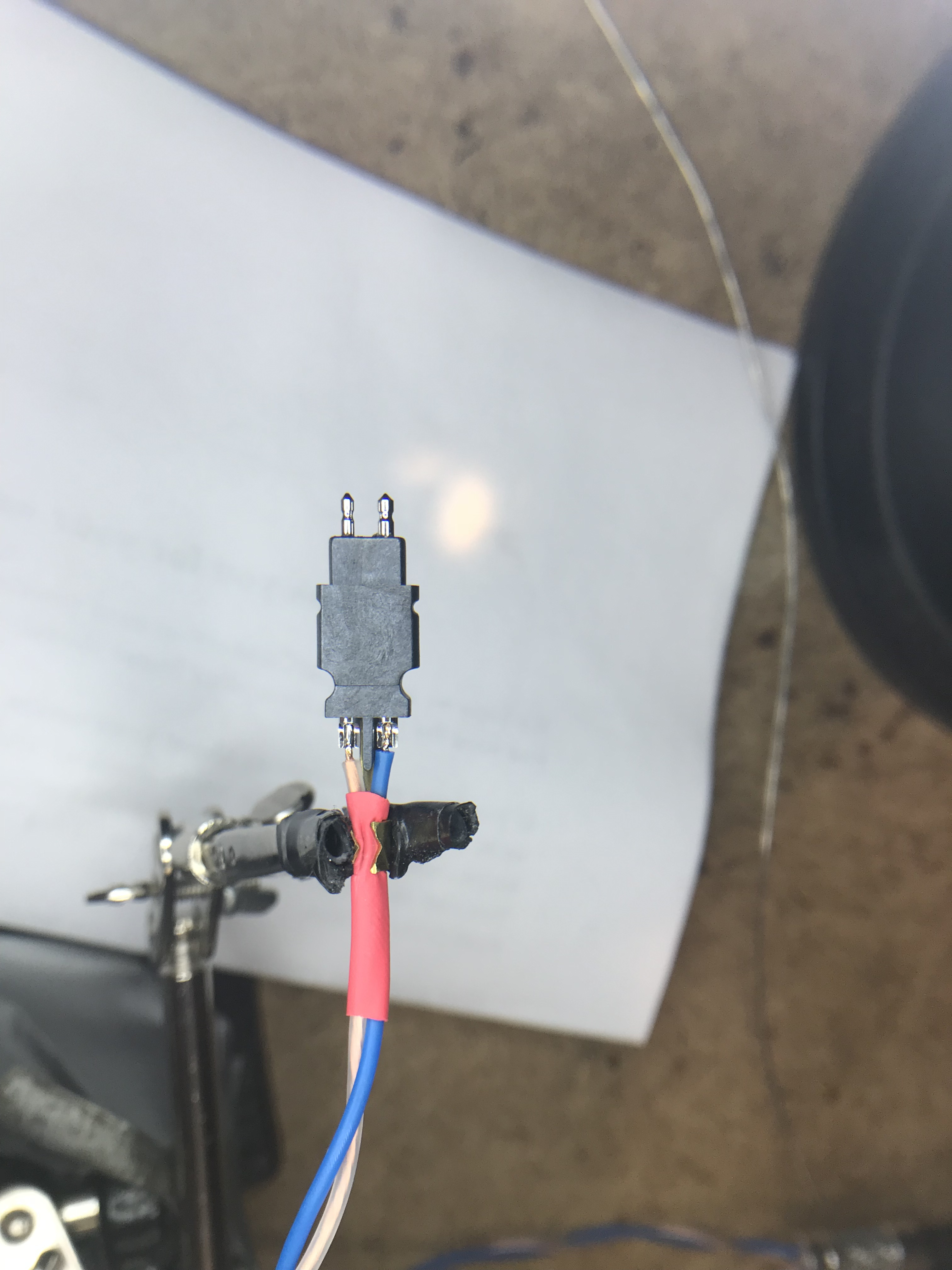
Soldered.

Finished.
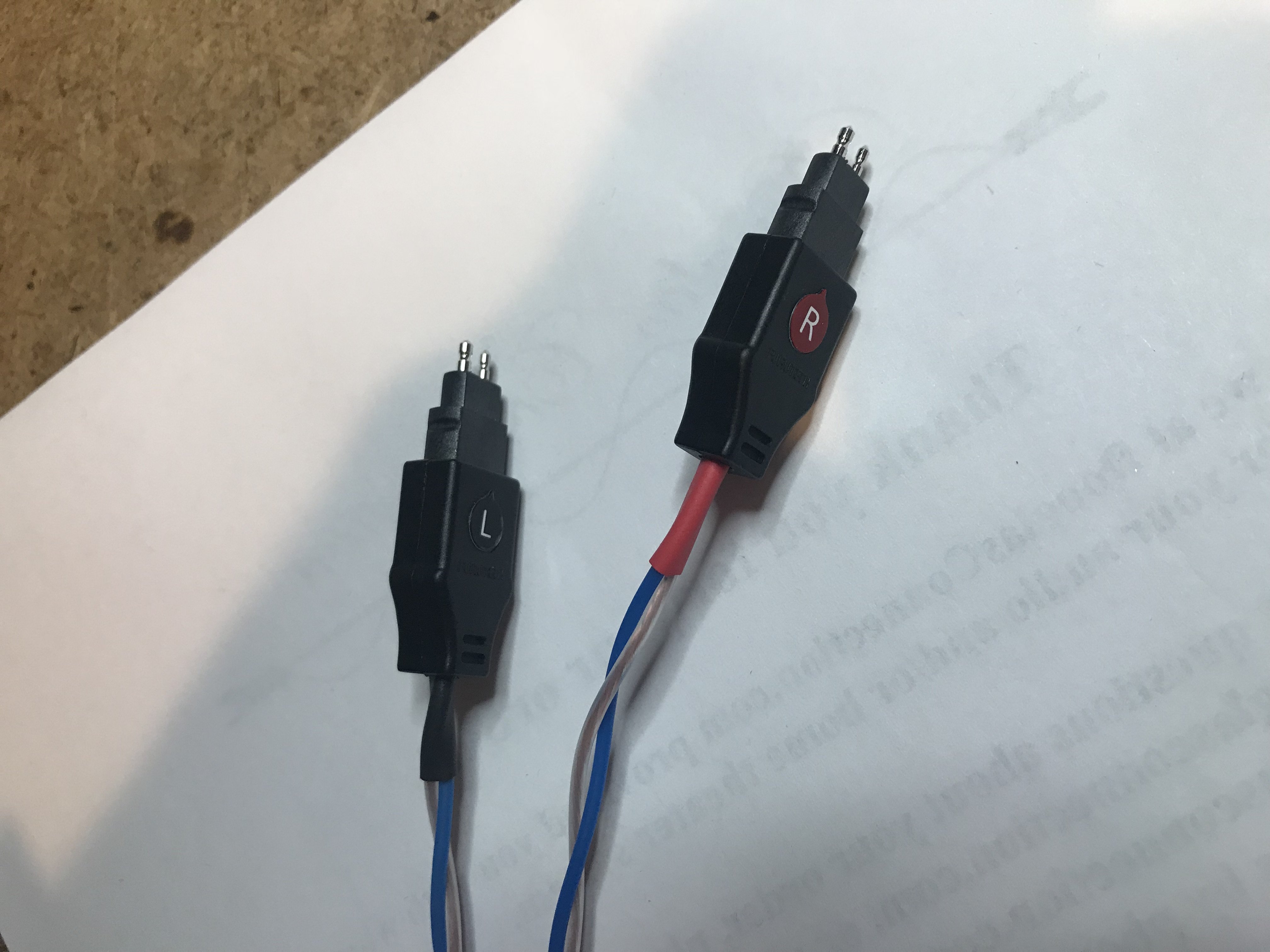
The works.
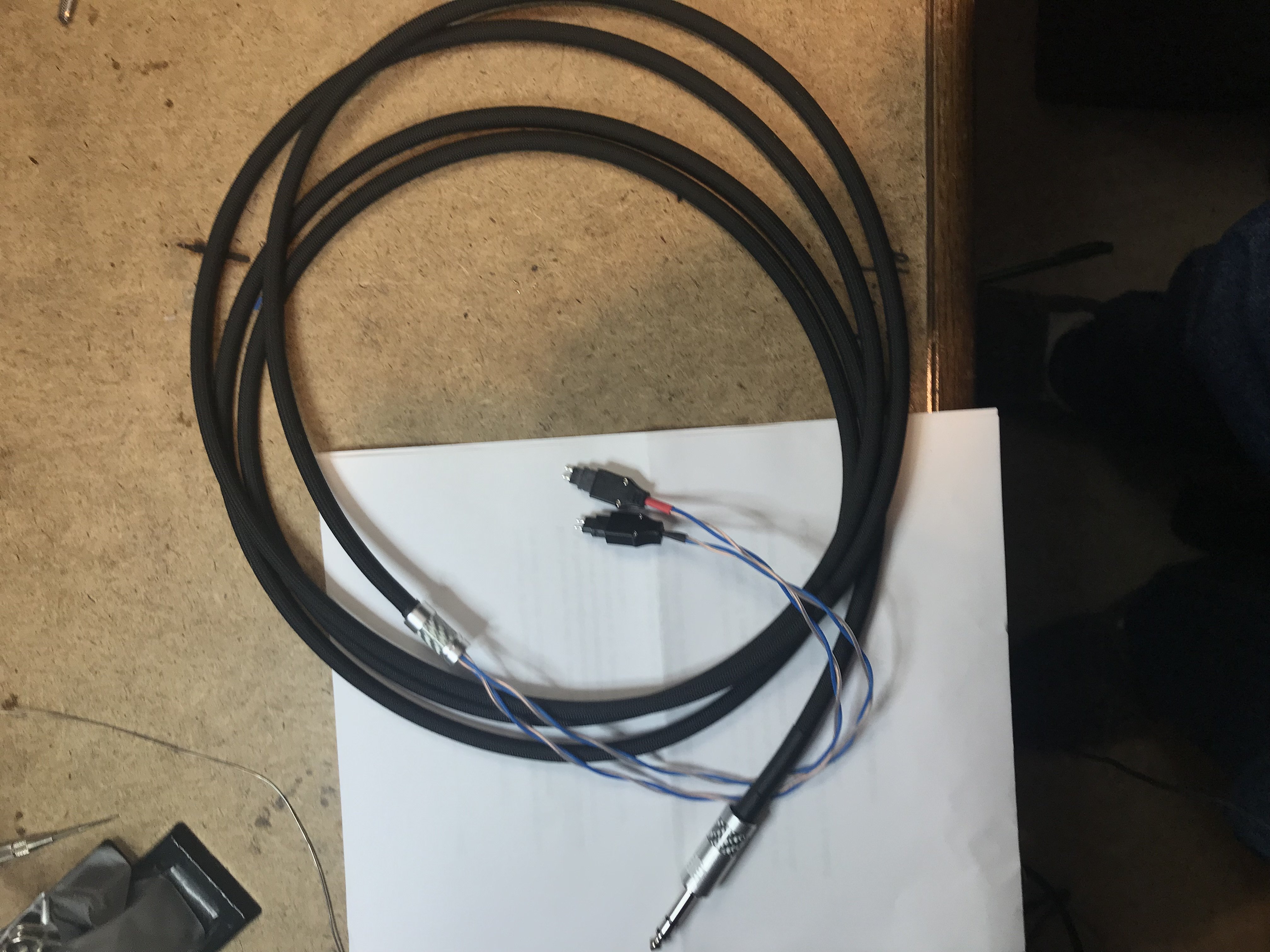
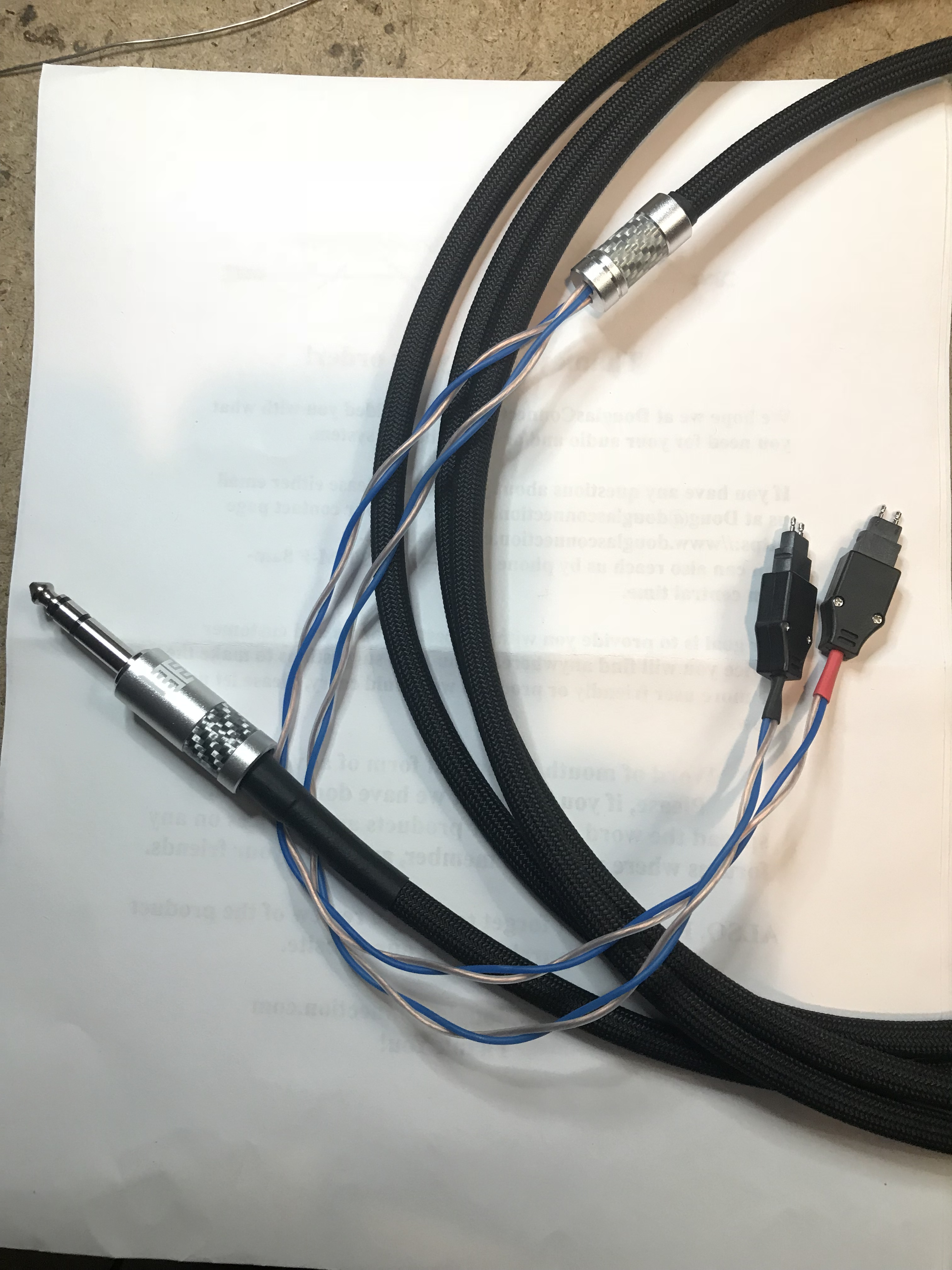
And the darn things work!
As a "service" I'll need to test these for at least 30 days and then the obligatory 90 day breakin period.
Aaron
Enabler Extraordinaire
Enabler Extraordinaire
Comments
-
Hmm....my solder kit doesn't contain hemostats.
Have I been demoted back to pre-beginner...?Where’s the KABOOM?!?! There’s supposed to be an Earth shattering KABOOM!!! -
My proctologist is missing his... Next visit I'll get you some.Aaron
Enabler Extraordinaire -
Those look familiar! I like 'em!Jay
SDA 2BTL * Musical Fidelity A5cr amp * Oppo BDP-93 * Modded Adcom GDA-600 DAC * Rythmik F8 (x2)
Micro Seiki DQ-50 * Hagerman Cornet 2 Phono * A hodgepodge of cabling * Belkin PF60
Preamp rotation: Krell KSL (SCompRacer recapped) * Manley Shrimp * PS Audio 5.0 -
My proctologist is missing his... Next visit I'll get you some.
I don't even want to know......
T EM EI T EM EI..... -
You have a stroke at the end there bro?"....not everything that can be counted counts, and not everything that counts can be counted." William Bruce Cameron, Informal Sociology: A Casual Introduction to Sociological Thinking (1963) -
EndersShadow wrote: »
Maybe:) -
Don't be such a baby. I'll wash 'em this time.
Aaron
Enabler Extraordinaire -
LOL -
Nice work, and great write-up!
Is Halo that guy who's been moving for the past year?
How does that "Soft Techflex" compare to the regular stuff? Is it clothy or something? I notice the regular stuff is stiff and scratchy and can be snaggy sometimes.
Is this cable heavy? Wondering whether we could find a cable/shirt-clip kind of thing. Maybe a chest harness.
I always keep some linguine handy when I'm building cables too. You just never know.I disabled signatures. -
I’ve used it before. It is cloth like so it doesn’t feel plasticy like the other texhflex. More like thin yarn. Feels very nice but it catches hair and stuff easier and it’s harder to get over the cable."....not everything that can be counted counts, and not everything that counts can be counted." William Bruce Cameron, Informal Sociology: A Casual Introduction to Sociological Thinking (1963)
-
Halo is on the move - I'll assume he's one in the same.
I refuse to use "regular" tech flex - it's nasty. This stuff is much more cloth like, hard to cut (just need a good sharp scissors, nothing fancy) but doesn't fray out as badly as some of the plastic stuff and is quiet. It is heavier than the plastic stuff, adds some weight to the cable, where with the plastic stuff you don't notice that. Next build I'll probably use it. It is harder to feed the cable through it compared to the plastic stuff but not impossible by any means.
Heavy...relative term... I sit and listen so weight doesn't really apply. As mentioned before - it does add some noticeable weight to the cable but nothing I'd be concerned with. If you're walking around with this stuff it could be uncomfortable - will add weight to the cans.
I clean my soldering iron on linguine, it makes the solder flow just that much better!Aaron
Enabler Extraordinaire -
Halo is on the move - I'll assume he's one in the same.I refuse to use "regular" tech flex - it's nasty. This stuff is much more cloth like, hard to cut (just need a good sharp scissors, nothing fancy) but doesn't fray out as badly as some of the plastic stuff and is quiet. It is heavier than the plastic stuff, adds some weight to the cable, where with the plastic stuff you don't notice that. Next build I'll probably use it. It is harder to feed the cable through it compared to the plastic stuff but not impossible by any means.
Heavy...relative term... I sit and listen so weight doesn't really apply. As mentioned before - it does add some noticeable weight to the cable but nothing I'd be concerned with. If you're walking around with this stuff it could be uncomfortable - will add weight to the cans.
Is this soft Techflex the same stuff you mentioned can take about 30 minutes to install on a cable? The plastic stuff, of course, zips right on.
Is there a reason for not encasing the y-wires in the same material?
I've been curious about Mogami wire. Have you used their stuff for anything else, like Interconnects or Speaker Cables?
My last question is, do you have any tricks for ensuring the y-wires are the same length? It seems that no matter how much care I take in equal measurement, when I have two wires like this, they almost always end up at slightly different lengths.I clean my soldering iron on linguine, it makes the solder flow just that much better!
I disabled signatures. -
Yep - about 1/2 inch at a time... slow but sure.
If you could find much smaller stuff it'll work. This stuff doesn't pull down to anything small like plastic techflex does (or my linguine). The adapter at the Y will determine what you can do. The one used here lets the wires through but there really isn't room to pass anything else through (even heat shrink) as I would like to do. My dream would be to use that cotton wrap (it pulls down tight to just one wire, two would work well also) and somehow secure it inside the Y thingy but there is no room to do that.
Mogami...rocks my universe. I've made speaker wire out of it, interconnects and use it liberally in building Bottlehead kits where shielded wire is needed. Used as speaker wire you have limits - I used the shield as one conductor and combined all four wires to get 18g total at the other conductor. It works well but don't push your 8000 watt amp through it.
Getting the Y wires straight with Mogami is fairly easy, I think that issue would be based on what wire you're using. I just rough cut insulation and shield and then just before striping the ends make sure they are all the same.Aaron
Enabler Extraordinaire -
Aaron: Were/are you happy with the Eidolic stuff?
For me, the "Y thingy" I wanted drove the purchase of the matching 1/4" plug, but I thought it was easy to work with/seemed like good quality. Nothing to compare it to, though.Jay
SDA 2BTL * Musical Fidelity A5cr amp * Oppo BDP-93 * Modded Adcom GDA-600 DAC * Rythmik F8 (x2)
Micro Seiki DQ-50 * Hagerman Cornet 2 Phono * A hodgepodge of cabling * Belkin PF60
Preamp rotation: Krell KSL (SCompRacer recapped) * Manley Shrimp * PS Audio 5.0 -
Halo deserves the best! Nice work Aaron. I think I have an Aaron-Mogami for my HD-650's.
Now I see where I have gone wrong...you remove that covering over the wire before soldering. Thanks! I can go back to rosin core now. Acid worked better with the insulation on.
Tin the ends (solder together the naked copper wires). This will keep stray strands from escaping and shorting stuff out later. It also makes it much easier to solder this together.
Salk SoundScape 8's * Audio Research Reference 3 * Bottlehead Eros Phono * Park's Audio Budgie SUT * Krell KSA-250 * Harmonic Technology Pro 9+ * Signature Series Sonore Music Server w/Deux PS * Roon * Gustard R26 DAC / Singxer SU-6 DDC * Heavy Plinth Lenco L75 Idler Drive * AA MG-1 Linear Air Bearing Arm * AT33PTG/II & Denon 103R * Richard Gray 600S * NHT B-12d subs * GIK Acoustic Treatments * Sennheiser HD650 * -
Were/are you happy with the Eidolic stuff?
Ya - it's decent quality. The 1/4" jack was very easy to put together. I like that they included the insulator with it.
The Y thing - it just happened to work with that cable/techflex and one layer of heatshrink - I pulled it all together and it fit very tightly. Another combination of things and it would have either not gone together or have been lose. I wish the exit holes were bigger. First time I've used such a thing although I have used the ViaBlue splitters on speaker cable. Normally it's cable pants or heatshrink.
Edit:
Other than the clampy thing on the 1/4" plug there is no strain relief - at the plug that's fine. you can't take that Y thing apart and, as they recommend, you either fill it with hot glue or figure out a way to jam the cable into it. A simple set screw would be nice on that.
Rich - here's how I normally remove the shield and insulation but because it was for someone I like I did it a different way. Feel free to use this method.
Aaron
Enabler Extraordinaire -
The short way breaks wire in quick too.Salk SoundScape 8's * Audio Research Reference 3 * Bottlehead Eros Phono * Park's Audio Budgie SUT * Krell KSA-250 * Harmonic Technology Pro 9+ * Signature Series Sonore Music Server w/Deux PS * Roon * Gustard R26 DAC / Singxer SU-6 DDC * Heavy Plinth Lenco L75 Idler Drive * AA MG-1 Linear Air Bearing Arm * AT33PTG/II & Denon 103R * Richard Gray 600S * NHT B-12d subs * GIK Acoustic Treatments * Sennheiser HD650 *
-
Yeah, on the Y I was curious how it would work out. I put an inch of clear heat shrink on the blue/white pairs at the split and it went thorough the hole with decent friction-fit; likewise the diameter of the sleeving offers a smidgeon of friction at the other end.
I won't be carrying my 'phones around by the Y jewelry, in any case.Jay
SDA 2BTL * Musical Fidelity A5cr amp * Oppo BDP-93 * Modded Adcom GDA-600 DAC * Rythmik F8 (x2)
Micro Seiki DQ-50 * Hagerman Cornet 2 Phono * A hodgepodge of cabling * Belkin PF60
Preamp rotation: Krell KSL (SCompRacer recapped) * Manley Shrimp * PS Audio 5.0 -
Rich - here's how I normally remove the shield and insulation but because it was for someone I like I did it a different way. Feel free to use this method.
Looks like a dim bulb tester.
As in: "Hey! Who's the dim bulb that thought it'd be OK to wire it like this?!Jay
SDA 2BTL * Musical Fidelity A5cr amp * Oppo BDP-93 * Modded Adcom GDA-600 DAC * Rythmik F8 (x2)
Micro Seiki DQ-50 * Hagerman Cornet 2 Phono * A hodgepodge of cabling * Belkin PF60
Preamp rotation: Krell KSL (SCompRacer recapped) * Manley Shrimp * PS Audio 5.0 -
The adapter at the Y will determine what you can do. The one used here lets the wires through but there really isn't room to pass anything else through (even heat shrink) as I would like to do.
My dream would be to use that cotton wrap (it pulls down tight to just one wire, two would work well also) and somehow secure it inside the Y thingy but there is no room to do that.
I get what you're saying though about not having much termination space inside the barrel; typically small and short. Thinking maybe you could skip the insert, possibly, or open it up to match whatever you have coming out? Maybe use heatshrink over the whole barrel, closing around the y-wires as much as possible?
I did this with adhesive heatshrink on speaker cables before. In this example, I think I shrunk it too much, but you can see where I used a pair of needle-nose pliers to pinch down between the wires to seal them and bond the Techflex inside.
Do you think you could maybe try something like this with adhesive backed heatshrink for inside the barrel to secure everything? Then maybe another piece of heatshrink to cover the barrel and close in around the ends? Or maybe fill the end of the barrel with something?I disabled signatures. -
Which one did you choose?
Did you choose wisely?For me, the "Y thingy" I wanted drove the purchase of the matching 1/4" plug, but I thought it was easy to work with/seemed like good quality. Nothing to compare it to, though.
I disabled signatures. -
Oh, you've seen my efforts: http://forum.polkaudio.com/discussion/comment/2371109#Comment_2371109
Yes, I've been happy with the results of my first cable-making foray.Jay
SDA 2BTL * Musical Fidelity A5cr amp * Oppo BDP-93 * Modded Adcom GDA-600 DAC * Rythmik F8 (x2)
Micro Seiki DQ-50 * Hagerman Cornet 2 Phono * A hodgepodge of cabling * Belkin PF60
Preamp rotation: Krell KSL (SCompRacer recapped) * Manley Shrimp * PS Audio 5.0 -
Yes, I've noticed this as well with those barrels' inserts with the predrilled holes. Depending on the size of the insert, could you widen the holes with Dremel so that heatshrink or sheathing could fit through?
I get what you're saying though about not having much termination space inside the barrel; typically small and short. Thinking maybe you could skip the insert, possibly, or open it up to match whatever you have coming out? Maybe use heatshrink over the whole barrel, closing around the y-wires as much as possible?
I did this with adhesive heatshrink on speaker cables before. In this example, I think I shrunk it too much, but you can see where I used a pair of needle-nose pliers to pinch down between the wires to seal them and bond the Techflex inside.
Do you think you could maybe try something like this with adhesive backed heatshrink for inside the barrel to secure everything? Then maybe another piece of heatshrink to cover the barrel and close in around the ends? Or maybe fill the end of the barrel with something?
The holes are so close that if you attempt to wide two holes I think you'll end up with one hole - now, that's not a bad thing, just something to watch for.
Cuteness is a major factor with this particular Y thing - covering it with heatshrink....heck, leave it out and just use heat shrink.
They do recommend filling the gap with some cotton and then finishing with hot glue but to do so you have to get into it - that's not easy with the main wire almost filling the big hole.
Adhesive heat shrink - that looks nice!Aaron
Enabler Extraordinaire -
Agreed, Aaron.
My guess (based on pictures from doublehelix website) is that the Eidolic Y is perhaps more designed towards receiving braided thin cables than the shielded & jacketed Mogami we're using.
It (the Y) came with a gasket whose inner diameter was just laughable compared to the relative girth of the Mogami. 'Twas good fortune that the Mogami/sleeving fills up the Y pretty completely as it gives a bit of a friction fit. Would be challenging to add additional cotton/glue as there's not much additional room in there.Jay
SDA 2BTL * Musical Fidelity A5cr amp * Oppo BDP-93 * Modded Adcom GDA-600 DAC * Rythmik F8 (x2)
Micro Seiki DQ-50 * Hagerman Cornet 2 Phono * A hodgepodge of cabling * Belkin PF60
Preamp rotation: Krell KSL (SCompRacer recapped) * Manley Shrimp * PS Audio 5.0 -
I like to use a variable speed drill to twist wires. Key words, variable and slow.
My replacement inexpensive or cheap hot air station....Jasper is responsible for this upgrade. Something about that hot air tube he couldn't resist, and I've been working a lot last several months. Cuts into his play time. Came with a few tips. I can do round, square and rectangle skin burns now....
Salk SoundScape 8's * Audio Research Reference 3 * Bottlehead Eros Phono * Park's Audio Budgie SUT * Krell KSA-250 * Harmonic Technology Pro 9+ * Signature Series Sonore Music Server w/Deux PS * Roon * Gustard R26 DAC / Singxer SU-6 DDC * Heavy Plinth Lenco L75 Idler Drive * AA MG-1 Linear Air Bearing Arm * AT33PTG/II & Denon 103R * Richard Gray 600S * NHT B-12d subs * GIK Acoustic Treatments * Sennheiser HD650 * -
Wow... odd, looks like my proctologist office...Aaron
Enabler Extraordinaire -
ROFLMAO
Looks very recital linear
-
Wow... odd, looks like my proctologist office...
It would cause far more problems than it could solve.....Salk SoundScape 8's * Audio Research Reference 3 * Bottlehead Eros Phono * Park's Audio Budgie SUT * Krell KSA-250 * Harmonic Technology Pro 9+ * Signature Series Sonore Music Server w/Deux PS * Roon * Gustard R26 DAC / Singxer SU-6 DDC * Heavy Plinth Lenco L75 Idler Drive * AA MG-1 Linear Air Bearing Arm * AT33PTG/II & Denon 103R * Richard Gray 600S * NHT B-12d subs * GIK Acoustic Treatments * Sennheiser HD650 * -
You like your Aoyue?
Daddy needs a new solder station, I don’t think I need hot air but they have some nice standard stations.Aaron
Enabler Extraordinaire -
You like your Aoyue?
Daddy needs a new solder station, I don’t think I need hot air but they have some nice standard stations.
Yeah it's decent. It has auto off so it cools down first. I've done some chip removal with it.
I'd avoid the cheap combo hot air/solder stations. My fav and still go to solder station is analog, WES51. Look at Hakko too.
Hakko FX888D is another well liked station.
Salk SoundScape 8's * Audio Research Reference 3 * Bottlehead Eros Phono * Park's Audio Budgie SUT * Krell KSA-250 * Harmonic Technology Pro 9+ * Signature Series Sonore Music Server w/Deux PS * Roon * Gustard R26 DAC / Singxer SU-6 DDC * Heavy Plinth Lenco L75 Idler Drive * AA MG-1 Linear Air Bearing Arm * AT33PTG/II & Denon 103R * Richard Gray 600S * NHT B-12d subs * GIK Acoustic Treatments * Sennheiser HD650 *