Best Way To Fix a Loose Threaded Insert in a Speaker Baffle
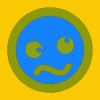
Stonecutter
Posts: 35
I have a pair of Nola Reference Viper III speakers. Recently I removed the tweeters to send them to the manufacturer to be upgraded.
The cap screws that fasten the tweeters to the baffle attach by way of threaded inserts. Two of these were loose. One came out with the cap screw. The other remained in the baffle, but was too loose for me to be able to torque the cap screw back into it.
I would be grateful for suggestions about how to rescuer these threaded inserts.
Thanks in advance.
The cap screws that fasten the tweeters to the baffle attach by way of threaded inserts. Two of these were loose. One came out with the cap screw. The other remained in the baffle, but was too loose for me to be able to torque the cap screw back into it.
I would be grateful for suggestions about how to rescuer these threaded inserts.
Thanks in advance.
Comments
-
I had this happen as well. If you can buy the size up hardware (threaded insert and screw) I would try to do that. The other thing I have done is to gorilla glue the old hardware back in its place. The gorilla glue expands and will anchor the threaded insert pretty well provided you do not over torque it.Shawn
AVR: Marantz SR-5011
Center Channel: Polk LsiM706c
Front: Polk LsiM703
Rear: LSI fx
Subwoofer: SVS 20-39pci
Television: Samsung UN58NU7100FXZA
DVD Player: Sony PS4 -
I should have included a second question in this thread:
The leads to the tweeters were soldered to the contacts.
I would prefer to simplify the tasks of replacing these tweeters and, perhaps, of removing them in the future by reinstalling them with insulated quick disconnects in the lead wires.
Would this approach diminish sound quality? -
I had this happen as well. If you can buy the size up hardware (threaded insert and screw) I would try to do that. The other thing I have done is to gorilla glue the old hardware back in its place. The gorilla glue expands and will anchor the threaded insert pretty well provided you do not over torque it.
Thank you.
I prefer not to "upsize" the insert and the cap screw. The tweeters (and other drivers) are exposed most of the time, and I want to avoid a "mismatch" in the appearance of the caps crews.
Do you think "coating" the inside of the hole in the baffle with a Plastic Wood-like product, then reinstalling the threaded insert would secure it?Post edited by Stonecutter on -
STOP, do not use Gorilla glue.Political Correctness'.........defined
"A doctrine fostered by a delusional, illogical minority and rabidly promoted by an unscrupulous mainstream media, which holds forth the proposition that it is entirely possible to pick up a t-u-r-d by the clean end."
President of Club Polk -
So, Gorilla glue is a polyurethane based product that cures by moisture. As it cures, it tends to expand due to the air bubbles created during the process. The last thing one wants is air bubbles in their glue as each air pocket is a weak spot. That crap should be removed from the market.
What you want to use is epoxy.
Political Correctness'.........defined
"A doctrine fostered by a delusional, illogical minority and rabidly promoted by an unscrupulous mainstream media, which holds forth the proposition that it is entirely possible to pick up a t-u-r-d by the clean end."
President of Club Polk -
Thank you, @Finut.
Having read several of your posts, you seem to have a lot of knowledge and experience with this sort of issue.
What do you recommend?
Because of the design of these speakers, hurricane nuts are to an option. -
Hurricane nutsSDA SRS 2.3TL's
Silk Audio MS-90-BT integrated tube amp
Yaqin MS-20L integrated tube amp
SDA 2B TL's -
michaeljhsda2 wrote: »Hurricane nuts
Unfortunately, the design of these open-baffle speakers precludes this option, which in other circumstances would be quick and simple and effective.
-
Ah, when I read your post "hurricane nuts are to an option" I just figured you left out the O on "to"...LOLSDA SRS 2.3TL's
Silk Audio MS-90-BT integrated tube amp
Yaqin MS-20L integrated tube amp
SDA 2B TL's -
What you want to use is epoxy.
Sorry, @F1nut, I missed your recommendation when I first read your post. I'll use JB Weld.
Thank you. -
I can't recommend JB Weld for this. You want a high grade epoxy, something that will soak into the MDF a bit to harden it as as well as hold the threaded insert securely. 5 minute epoxy is a better choice than JB Weld, but something like West Systems marine grade is the best.Political Correctness'.........defined
"A doctrine fostered by a delusional, illogical minority and rabidly promoted by an unscrupulous mainstream media, which holds forth the proposition that it is entirely possible to pick up a t-u-r-d by the clean end."
President of Club Polk -
I can't recommend JB Weld for this. You want a high grade epoxy, something that will soak into the MDF a bit to harden it as as well as hold the threaded insert securely. 5 minute epoxy is a better choice than JB Weld, but something like West Systems marine grade is the best.
Thanks for this advice, @F1nut.
I'll look for the West Systems product at our nearby West marine store.
I this the right stuff?
http://www.westmarine.com/buy/west-system--g-flex-655-8-epoxy-adhesive--15537087 -
I use the 105/205 combo, but you likely don't want to lay out that much cash for what little you'll use. So, I think your choice will be ok, but run it by the guys at West Marine first. They may recommend the liquid version of the G-flex, perhaps with one of the fillers.
The way I would do it is mix up some of the 105/205, then apply to the hole in the MDF letting it soak in. Next, I'd add one of the fillers to my mixed up batch, coat the threads and put some in the hole. Shove the insert into the hole, wipe off the excess and let cure for 24 hours. You may want to tape off the area around the hole to help prevent the epoxy from getting on the finish. Be sure to check none gets in the screw threads. If it does use a Q-tip or the like soaked with lacquer thinner to clean it out.Political Correctness'.........defined
"A doctrine fostered by a delusional, illogical minority and rabidly promoted by an unscrupulous mainstream media, which holds forth the proposition that it is entirely possible to pick up a t-u-r-d by the clean end."
President of Club Polk -
[quote="F1nut;2272481"
The way I would do it is mix up some of the 105/205, then apply to the hole in the MDF letting it soak in. Next, I'd add one of the fillers to my mixed up batch, coat the threads and put some in the hole. Shove the insert into the hole, wipe off the excess and let cure for 24 hours. You may want to tape off the area around the hole to help prevent the epoxy from getting on the finish. Be sure to check none gets in the screw threads. If it does use a Q-tip or the like soaked with lacquer thinner to clean it out. [/quote]
-
@F1nut,
Thank you for the more detailed information.
I definitely do not want to get any of the epoxy on the finish, which is really beautiful. It would be a disaster to get the threaded insert epoxied into the hole only to discover the threads had been covered with the epoxy. Good warnings!
I'll see what the guys at West marine recommend.
Do you have an opinion about my other question, which was whether installing quick disconnects in the leads to the tweeters to facilitate reinstallation and future removal would be a good idea?
Would this solution compromise sound quality?
The leads were soldered to the tweeter contacts. I cut the leads rather than trying to desolder the connections. The desoldering operation would have been in close quarters with the speaker cabinets, and I was concerned about potential damage to the finish. I was also concerned about soldering the leads when reinstalling the tweeters. -
The rest of the story:
I took the advice of @F1nut and purchased West Marine's "Six10" adhesive, which comes in a tube for use in a caulking gun. The resin and hardener are mixed as the material is forced through a removable tip. It's a good system.
With that said, however, I found that I didn't need to use it.
When I started working on the speakers I found that the threaded inserts had been driven too deeply into the holes. I gently backed them out with a hex wrench, and they were secure enough to use without the epoxy.
Had I not been worried about damaging the finish or getting epoxy in the threads, I would likely have used the epoxy anyway -- just in case. But I was worried.
I also decided to bite the bullet and solder the leads back on to the tweeters. I devised a "jig" to hold the tweeters securely while I soldered the leads to the contacts. This enabled me to do the job, even with my amateur-caliber skills without damaging the finish.
Thanks again for your advice, which gave me confidence to do this job.