SRS 2.3 Mechanical Upgrades with Hurricane Nuts
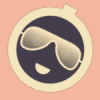
scottie
Posts: 10
After finding this forum, I was inspired to start upgrading my speakers. I'm starting with the mechanical upgrades. Dynamat Xtreme, Hurricane Nuts, replaced 2 binding posts that had broken off in a recent move. I wanted to use Larry's rings because I think they would be easier, but my amps are coming back from the repair shop soon and I wanted to finish the mechanical upgrades sometime around the time they arrived.
So I assembled some supplies.
Loctite Power grab, Armacell, JB Weld Steel Stick, Dynamat xtreme, Hurricane nuts, button head cap screws. There are other discussions that talk about the use of these products, except, I didn't find anything on the hurricane nuts.
I thought I'd share my experience with the hurricane nuts since I didn't find much information on this forum on installing them, or what size to use. So far I have only completed 1 speaker.
I used the 8-32 hurricane nuts from parts express. I felt this size would better reflect the size of the wood screws that came out of there. Turns out, this was a perfect size for this application. I ordered 2 packs of 50 for the SRS 2.3's 48 per speaker is what's needed. 2 nuts were messed up (by me), so 2 extra is cutting it close.
I purchased 1 1/4" 8-32 button head cap screws. The button head cap screws I used were black and matched the outside of the baskets nicely. I think 1 inch would be better except for the 4 holding the binding post plate. 1 1/4" seemed good for those. I may replace the others sometime with 1" screws.
All the holes on my first speaker were in a good location for the baskets so I just chased those holes with a 3/16" drill. My drill has a level on it which is a nice feature for this. Trying to muscle these speakers onto a drill press by myself didn't seem like an option (they are close to 150 lbs).
Once all the holes were enlarged, I cleaned the fronts and backs around the holes with a real sharp chisel. It turns out that the original screws pushed out the mdf on the backside and I wanted this flat for the hurricane nuts. Now for the trick that I eventually discovered help me get the threads started later. I used a woodworking deburring tool that i use to clean up holes when drilling in the shop. This also removes the slight bulge that the drill makes as it enters the mdf. At first I just used the chisel and cleaned this up, but cleaning out the hole after i used the chisel seemed to keep less dust from entering the threads when I inserted the screws.
I then pressed the hurricane nuts into the holes with a C-clamp. I carefully threaded the screws into the hurricane nuts to ensure they would start prior to installing the drivers. Getting the hurricane nuts to lay flat is important here to keep from cross threading when starting. Thats how I messed up 2 of them. There is also the possibility of glue from when the case was manufactured in the way in a few areas. this excess glue will need to be removed -sharp chisel wins here too. A couple of braces between the tweeters needed to have the edges shaved and any excess glue removed in order for the hurricane nuts to be installed - sharp chisel wins again.
I then installed the newly Dynamat clad baskets back into the holes with the new fasteners. A very nice positive mount is achieved with these.
Now I can get back into these speakers anytime I need to without having to worry about stripping the screws out on the drivers.
Next time into this speaker will be when I replace the capacitors and resistors.
So I assembled some supplies.
Loctite Power grab, Armacell, JB Weld Steel Stick, Dynamat xtreme, Hurricane nuts, button head cap screws. There are other discussions that talk about the use of these products, except, I didn't find anything on the hurricane nuts.
I thought I'd share my experience with the hurricane nuts since I didn't find much information on this forum on installing them, or what size to use. So far I have only completed 1 speaker.
I used the 8-32 hurricane nuts from parts express. I felt this size would better reflect the size of the wood screws that came out of there. Turns out, this was a perfect size for this application. I ordered 2 packs of 50 for the SRS 2.3's 48 per speaker is what's needed. 2 nuts were messed up (by me), so 2 extra is cutting it close.
I purchased 1 1/4" 8-32 button head cap screws. The button head cap screws I used were black and matched the outside of the baskets nicely. I think 1 inch would be better except for the 4 holding the binding post plate. 1 1/4" seemed good for those. I may replace the others sometime with 1" screws.
All the holes on my first speaker were in a good location for the baskets so I just chased those holes with a 3/16" drill. My drill has a level on it which is a nice feature for this. Trying to muscle these speakers onto a drill press by myself didn't seem like an option (they are close to 150 lbs).
Once all the holes were enlarged, I cleaned the fronts and backs around the holes with a real sharp chisel. It turns out that the original screws pushed out the mdf on the backside and I wanted this flat for the hurricane nuts. Now for the trick that I eventually discovered help me get the threads started later. I used a woodworking deburring tool that i use to clean up holes when drilling in the shop. This also removes the slight bulge that the drill makes as it enters the mdf. At first I just used the chisel and cleaned this up, but cleaning out the hole after i used the chisel seemed to keep less dust from entering the threads when I inserted the screws.
I then pressed the hurricane nuts into the holes with a C-clamp. I carefully threaded the screws into the hurricane nuts to ensure they would start prior to installing the drivers. Getting the hurricane nuts to lay flat is important here to keep from cross threading when starting. Thats how I messed up 2 of them. There is also the possibility of glue from when the case was manufactured in the way in a few areas. this excess glue will need to be removed -sharp chisel wins here too. A couple of braces between the tweeters needed to have the edges shaved and any excess glue removed in order for the hurricane nuts to be installed - sharp chisel wins again.
I then installed the newly Dynamat clad baskets back into the holes with the new fasteners. A very nice positive mount is achieved with these.
Now I can get back into these speakers anytime I need to without having to worry about stripping the screws out on the drivers.
Next time into this speaker will be when I replace the capacitors and resistors.
Comments
-
Nice write up, thanks for posting.
Since the OD of the Hurricane nut shaft (not the burrs) is 7/32 I use the same size drill bit.I then pressed the hurricane nuts into the holes with a C-clamp.
Most have found that instead of pressing them in it's better to use a screw with a washer to pull them in, which causes the nut to twist into place.I carefully threaded the screws into the hurricane nuts to ensure they would start prior to installing the drivers.
An excellent tip and one I strongly recommend. Another tip I recommend is to apply a dab or two of epoxy to the flange of the nut.Political Correctness'.........defined
"A doctrine fostered by a delusional, illogical minority and rabidly promoted by an unscrupulous mainstream media, which holds forth the proposition that it is entirely possible to pick up a t-u-r-d by the clean end."
President of Club Polk -
Thanks for the comment F1. I'll find a box of 7/16 holes instead. I really like the washer screw idea. I'll do that on the next one. Do you apply the epoxy to the underside of the flange or slightly into the hole?
-
I'll find a box of 7/16 holes instead.
Not following you on that one.Do you apply the epoxy to the underside of the flange or slightly into the hole?
I've put it on the flange only not wanting to get any in the threads.
Political Correctness'.........defined
"A doctrine fostered by a delusional, illogical minority and rabidly promoted by an unscrupulous mainstream media, which holds forth the proposition that it is entirely possible to pick up a t-u-r-d by the clean end."
President of Club Polk -
I'll find a box of 7/16 holes instead.
Not following you on that one.i used 3/16 holes, I thought I'd use 7/16s next time. I eyeballed it at 3/16 but found it a bit tight. Figured I'd order a box of 7/16's holes for the job.
-
7/16 holes? Really? I think the head of the screw would fit through a 7/16 hole. You must mean 7/32.
- SDA 2BTL · Sonicaps · Mills resistors · RDO-198s · New gaskets · H-nuts · Erse inductors · BH5 · Dynamat
- Crossover upgrades by westmassguy
- Marantz 1504 AVR (front speaker pre-outs to Adcom 555)
- Adcom GFA-555 amp · Upgrades & speaker protection added by OldmanSRS
- Pioneer DV-610AV DVD/CD player
- SDA CRS+ · Hidden away in the closet
- SDA 2BTL · Sonicaps · Mills resistors · RDO-198s · New gaskets · H-nuts · Erse inductors · BH5 · Dynamat
-
Yeah, definitely 7/32.Political Correctness'.........defined
"A doctrine fostered by a delusional, illogical minority and rabidly promoted by an unscrupulous mainstream media, which holds forth the proposition that it is entirely possible to pick up a t-u-r-d by the clean end."
President of Club Polk -
sorry, i think i started that silliness. 7/32 makes more sense. 3/16 was just a tad tight.