Custom Dual MM104 Box
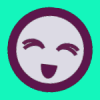
mtgcolwell
Posts: 4
Hey Polk Enthusiasts,
I have 2 Momo MM104s and a 92 Accord LX to put them in along with a nice Audiobahn 2ch 2150 Amp. I want to face them towards the front of the car and have a plexiglass window letting you see the nice Momo's thumping from the back. I want the inside of the box to look good with some sort of colored formica (spelling?) used on the interior of the box. I had this design quoted at one of the local car audio shops and they wanted $1400 for the install! I am not paying that. I am pretty handy with building stuff, so my buds and I going to try to build a box that I am dreaming of, but do not know the exact specs of what I want. Could anyone send me some great sub box plans? I am new to custom fabrication of audio components in my car and any advice is appreciated! Also, how much should materials cost?
I have 2 Momo MM104s and a 92 Accord LX to put them in along with a nice Audiobahn 2ch 2150 Amp. I want to face them towards the front of the car and have a plexiglass window letting you see the nice Momo's thumping from the back. I want the inside of the box to look good with some sort of colored formica (spelling?) used on the interior of the box. I had this design quoted at one of the local car audio shops and they wanted $1400 for the install! I am not paying that. I am pretty handy with building stuff, so my buds and I going to try to build a box that I am dreaming of, but do not know the exact specs of what I want. Could anyone send me some great sub box plans? I am new to custom fabrication of audio components in my car and any advice is appreciated! Also, how much should materials cost?
Post edited by mtgcolwell on
Comments
-
materials will usually run you 10-20% of the retail cost of a box -- least that's the trend i've noticed ... 1400 * .2 = 280
also -- i dont own your car. nor do i intend to spend xyz hours - yes hours - designing a box specific for your vehicle.
i spent an hour designing a rectangular box, just because i'm nit picky and wanted to see what different dimensions would do... do design a vehicle specific box of the extent you speak of is a several hour, or maybe even a day project.
you've got to do that yourself with a tape measure, a calculator, a pen and a pad...
as far as what materials to use, there i can help you.
the absolute most rigid and durable **** out there is cabinet grade baltic birch plywood... 40 - 50 dollars for a 4 foot by 8 foot sheet.
liquid nails or wood glue the joints (construction wood glue is good stuff - the maroon colored elmers stuff) and brad nail it... if you dont have a brad nailer (which i dont eitehr), predrill holes and use drywall screws.
if you wanna go cheap - MDF... 15 bucks for a sheet... it'll sound the same as the BP but its not going to be nearly as durable, rigid, or easy to work with... mdf splits... i've built enough mdf boxes to ahve come up with my own science for dealing with the ****... no glue, just 3/4" wide 1/8th inch thick foam weather stripping in the joints, and lots and lots of screws... and praying helps too i think.
a while ago another member of these boards enlightened me to the BP thing... i thought he was nuts -- then i just tried it cuz i was bored one day for a couple of 8's -- you can throw the box down the stairs and its fine...
now i refuse to use anything else for my equipment in the future.
far as the front panel -- 1" thick Plexiglass if its going to be a bandpass box and that's your "front panel" or whatever... go to a shop that builds industrial grade windows --- i was quoted like 100 bucks for two 18 x 14 pieces of precision cut 1" plexi with all the holes i wanted pre-drilled and counter sunk.
formica is a counter top / flooring material, why do u want that inside your box?
why not instead go with fleckstone, marbelized, or 'stone' paint ? unless you want to look like grandma's kitchen.
you could even do mirrors inside the interior walls... mirrored plexiglass is much safer (less chance of breakin on ya ) than glass mirrors, and its reasonably affordable for the really thin stuff... and that's all you'd need is somethin thin to panel the intrior with.
mirrored inside with a plexi front might look pretty prestigous.
also - the momo 10's call for a 0.66 cubic foot sealed inclosure for each ... or if you're doin bandpass - which it seems you are - you'll have to get ahold of kim or dig up some other older posts that give the bandpass specs and then adapt those to your box.The Artist formerly known as PoweredByDodge -
Don't use drywall screws, use wood screws if you are going to be using plywood. Wood screws are less likely to split wood and designed to hold onto wood better than other screws.Expert Moron Extraordinaire
You're just jealous 'cause the voices don't talk to you! -
Thanks PoweredByDodge -
I guess that formica crap you're talking about is what the installer was going to use on my box. I am definitely not going back there. I was going to use MDF, but I like the idea of the durable baltic birch plywood. Your idea of the mirrored interior of the box is quite good ... easier and much more appealing to the eye with the reflections of the MOMOs. How would I seal the plexiglass to the baltic birch plywood? I know the screws bolt the two together, but would I then use wood glue to seal it? -
well when mating plexi to wood, you'd have to rely on the 'trick' i got used to when making boxes out of MDF...
because liquid nails / wood glue tended to not hold up with mdf boxes (never knwew why, then jstas explained to me that the particles of the mdf get bonded, but since its particulated, it comes loose... like the crumbs of a cake... however since cabinet grade plywood is solid, once its bonded, its staying bonded).... i used to put 1/8" thick 3/4" wide foam weatherstripping between the joints of MDF boxes.
when bolting plexi to ply you'd want some (preferably black colored so it looks good) of that stuff... home depot or a hardware store usually sells enough to do a decent sized box for about 4 bucks. you'd stick it down to the wooden box part... since u'd use 3/4 inch wood.. 3/4 stripping would cover the joint perfect... and then lay the plexi (PREDRILLED!!!) down over the stripping... line it up good, and then carefully predrill your holes into the wood and sink in wood screws as jstas said...
he's prolly right -- i tend to use drywall screws as they are just easier to get moving really quickly, and dont leave a head (you can sink them flush)... but wood screws with a flat bottom probably have less likelyness to leave spurs of wood where the screw meets the wood... the way to make a woodscrew flush would just be to pilot drill then take a bit as large as the head of the screw and drill down like maybe 1/10" of an inch .. just some small indentation... then the head will sit in the hole.
cutting plexi and mirrored stuff may be a living nightmare... i've no idea, i never tried it... so unless somebody can give u tips on how to cut it, i suggest you build hte box with the use of that stuff in mind, then take exact measurements of where u want the mirrored stuff to go, and then have a local window/door/glass shop order and cut it for you. they'll usually do any straight cuts (even like angled stuff... as long as its not a round deal) for a reasonable price ( under 30) but once u start asking for funky stuff it'l go up.... i had wanted "Polk Audio" cut into the center of a 4 foot by 2 foot piece of mirrored plexi, but they wanted like 35 bucks for the sheet (ok not a problem...) and 150 to do the scroll cutting of the letters (... very NOT ok).The Artist formerly known as PoweredByDodge